Thermoplastic abrasive for polishing hard alloy and manufacture method thereof
A technology of hard alloys and manufacturing methods, applied in chemical instruments and methods, and other chemical processes, can solve the problems of complex manufacturing process, long production cycle, and low production efficiency, and achieve simple preparation process, short production cycle, and easy cleaning easy effect
- Summary
- Abstract
- Description
- Claims
- Application Information
AI Technical Summary
Problems solved by technology
Method used
Image
Examples
Embodiment 1
[0045] (1) Surface treatment of abrasives: Add 1 part of coupling agent γ-(2,3-glycidoxy)propyltrimethoxysilane to 100 parts of industrial alcohol and mix evenly, add it to a mixer, and oxidize 60 parts Add aluminum (500 mesh) into the mixer, heat and stir in a constant temperature water bath, the heating temperature is 60°C, the stirring speed is 80 r / min., and the stirring time is 40min. After the alcohol is evaporated to dryness, the material is dried, and the drying temperature is 100°C. The drying time is 7h;
[0046] (2) Add the alumina after the surface treatment in step (1) into the banburying-granulation machine and preheat while stirring. The preheating temperature is 110°C, the rotating speed is 10r / min, and the preheating time is 5min;
[0047] (3) 35 parts of polypropylene, 1.5 parts of stearic acid, 1 part of polyethylene wax, 0.75 parts of antioxidant β-(3,5-di-tert-butyl-4-hydroxyphenyl) propionate n-octadecyl Alcohol ester and 0.75 parts of tris(2,4-di-tert-b...
Embodiment 2
[0053] (1) Surface treatment of abrasives: Add 0.8 parts of coupling agent γ-aminopropyltriethoxysilane to 80 parts of industrial alcohol and mix evenly, add to the mixer, and add 80 parts of diamond (800 mesh) to the mixer , heating and stirring in a constant temperature water bath, the heating temperature is 70°C, the stirring speed is 60r / min., and the stirring time is 50min. After the alcohol evaporates to dryness, the material is dried, the drying temperature is 90°C, and the drying time is 8h;
[0054] (2) Add the diamond after surface treatment in step (1) into the banburying-granulation machine and preheat while stirring. The preheating temperature is 120°C, the rotating speed is 15r / min, and the preheating time is 4min;
[0055] (3) 18 parts of polyamide 6, 0.3 part of pentaerythritol stearate, 0.6 part of microcrystalline wax, 0.15 part of antioxidant tetrakis [β-(3,5-di-tert-butyl-4-hydroxyphenyl) propane Ester] pentaerythritol ester and 0.15 parts of dilauryl thiod...
Embodiment 3
[0061] (1) Surface treatment of abrasives: add 2.4 parts of coupling agent isopropyl trioleate acyloxy titanate to 240 parts of industrial alcohol and mix evenly, add to the mixer, add 68 parts of white corundum (1500 mesh) Put it into the mixer, heat and stir in a constant temperature water bath, the heating temperature is 80°C, the stirring speed is 70r / min., and the stirring time is 60min. After the alcohol evaporates to dryness, the material is dried, the drying temperature is 110°C, and the drying time is 6h;
[0062] (2) Add the diamond after surface treatment in step (1) into the banburying-granulation machine and preheat while stirring. The preheating temperature is 130°C, the rotating speed is 20r / min, and the preheating time is 3min;
[0063] (3) 27 parts of polybutylene terephthalate, 0.6 part of ethylene bisstearamide, 1 part of polyester wax, 0.5 part of antioxidant triethylene glycol bis[β-(3-tert Butyl-5-methyl-4-hydroxyphenyl) propionate] and 0.5 parts of bis(3...
PUM
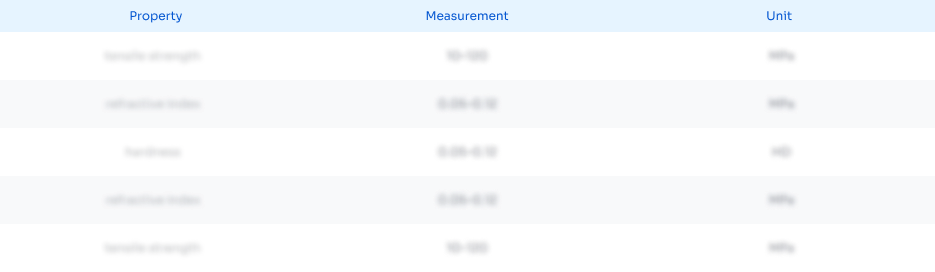
Abstract
Description
Claims
Application Information

- R&D
- Intellectual Property
- Life Sciences
- Materials
- Tech Scout
- Unparalleled Data Quality
- Higher Quality Content
- 60% Fewer Hallucinations
Browse by: Latest US Patents, China's latest patents, Technical Efficacy Thesaurus, Application Domain, Technology Topic, Popular Technical Reports.
© 2025 PatSnap. All rights reserved.Legal|Privacy policy|Modern Slavery Act Transparency Statement|Sitemap|About US| Contact US: help@patsnap.com