A preparation process for zrcrfe/alcrfetizr composite gradient alloy coating for anti-high temperature oxidation on the surface of zirconium alloy
A technology of anti-high temperature oxidation and gradient alloy, which is applied in the direction of metal material coating process, coating, vacuum evaporation plating, etc., can solve problems such as explosion and inability to guarantee structural integrity, achieve mature technology, and improve high temperature oxidation resistance , the effect of superior toughness
- Summary
- Abstract
- Description
- Claims
- Application Information
AI Technical Summary
Problems solved by technology
Method used
Image
Examples
Embodiment 1
[0022] a. Clean the substrate material: use water sandpaper with different roughness to zirconium alloy (Zr 4Alloy) substrate for grinding and polishing; then use acetone and ethanol as solvents to degrease and degrease and clean in an ultrasonic instrument; then clean with deionized water, dry and put into a vacuum chamber, and the vacuum degree is -4 Pa;
[0023] b. Treatment of the substrate before deposition: keep the vacuum chamber vacuum -4 Under the condition of Pa, the reverse sputtering was used for 10 minutes to clean the zirconium alloy substrate; the reverse sputtering bias voltage was -500V; the reverse sputtering gas was Ar; the reverse sputtering pressure in the vacuum chamber was 3.0 Pa;
[0024] c. Pre-sputtering: Keep the vacuum chamber vacuum -4 Under the condition of Pa, pre-sputtering is used to clean each target for 15 minutes, the purpose is to remove impurities on the surface of the target; the pre-sputtering power is 110W; the pre-sputtering bias is -1...
Embodiment 2
[0028] a. Clean the substrate material: use water sandpaper with different roughness to zirconium alloy (Zr 4 Alloy) substrate for grinding and polishing; then use acetone and ethanol as solvents to degrease and degrease and clean in an ultrasonic instrument; then clean with deionized water, dry and put into a vacuum chamber, and the vacuum degree is -4 Pa;
[0029] b. Treatment of the substrate before deposition: keep the vacuum chamber vacuum -4 Under the condition of Pa, the reverse sputtering was used for 10 minutes to clean the zirconium alloy substrate; the reverse sputtering bias voltage was -500V; the reverse sputtering gas was Ar; the reverse sputtering pressure in the vacuum chamber was 3.0 Pa;
[0030] c. Pre-sputtering: Keep the vacuum chamber vacuum -4 Under the condition of Pa, pre-sputtering is used to clean each target for 15 minutes, the purpose is to remove impurities on the surface of the target; the pre-sputtering power is 110W; the pre-sputtering bias is -...
Embodiment 3
[0033] a. Clean the substrate material: use water sandpaper with different roughness to zirconium alloy (Zr 4 Alloy) substrate for grinding and polishing; then use acetone and ethanol as solvents to degrease and degrease and clean in an ultrasonic instrument; then clean with deionized water, dry and put into a vacuum chamber, and the vacuum degree is -4 Pa;
[0034] b. Treatment of the substrate before deposition: keep the vacuum chamber vacuum -4 Under the condition of Pa, the reverse sputtering was used for 10 minutes to clean the zirconium alloy substrate; the reverse sputtering bias voltage was -500V; the reverse sputtering gas was Ar; the reverse sputtering pressure in the vacuum chamber was 3.0 Pa;
[0035] c. Pre-sputtering: Keep the vacuum chamber vacuum -4 Under the condition of Pa, pre-sputtering is used to clean each target for 15 minutes, the purpose is to remove impurities on the surface of the target; the pre-sputtering power is 110W; the pre-sputtering bias is -...
PUM
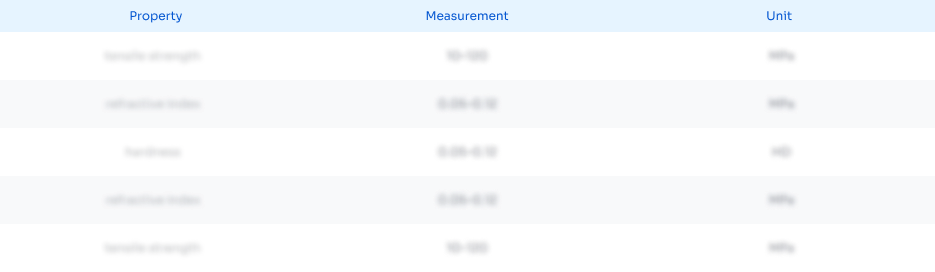
Abstract
Description
Claims
Application Information

- R&D
- Intellectual Property
- Life Sciences
- Materials
- Tech Scout
- Unparalleled Data Quality
- Higher Quality Content
- 60% Fewer Hallucinations
Browse by: Latest US Patents, China's latest patents, Technical Efficacy Thesaurus, Application Domain, Technology Topic, Popular Technical Reports.
© 2025 PatSnap. All rights reserved.Legal|Privacy policy|Modern Slavery Act Transparency Statement|Sitemap|About US| Contact US: help@patsnap.com