Sludge treatment method and treatment system
A sludge treatment and sludge technology, applied in the field of sludge treatment methods and treatment systems, can solve the problems of inability to decompose, increase the humidity of cement kiln flue gas, secondary water pollution, etc., and achieve the suppression of odor and Harmful and toxic gases, eliminating the effects of odor and harmful and toxic gases, and eliminating the hazards of secondary pollution
- Summary
- Abstract
- Description
- Claims
- Application Information
AI Technical Summary
Problems solved by technology
Method used
Image
Examples
Embodiment 1
[0069] Such as Figure 1~2 As shown, the present invention provides a sludge treatment system, including a closed pretreatment station, a sludge-derived cement raw material preparation system, a drying and grinding system, and a cement kiln system;
[0070] The cement kiln system includes a cement kiln tail dust collection system, a cement kiln tail smoke chamber, etc.;
[0071] The closed pretreatment station is provided with a sludge storage tank 1, a sludge mixer 2, and a belt conveyor in sequence according to the sludge treatment process; the discharge port of the sludge storage tank 1 is connected with the sludge pump 4 and the conveying pipe The inlet of the sludge mixer 2 is connected; the outlet of the sludge mixer 2 is connected to the sludge-derived cement raw material preparation system through a belt conveyor; the inlet of the sludge mixer 2 is also connected with a strengthening modifier The outlet of the silo 6, the raw meal silo 7 is connected; the air outlet of the...
PUM
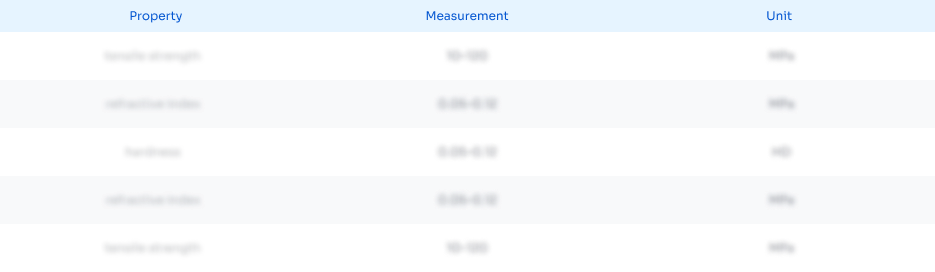
Abstract
Description
Claims
Application Information

- R&D Engineer
- R&D Manager
- IP Professional
- Industry Leading Data Capabilities
- Powerful AI technology
- Patent DNA Extraction
Browse by: Latest US Patents, China's latest patents, Technical Efficacy Thesaurus, Application Domain, Technology Topic, Popular Technical Reports.
© 2024 PatSnap. All rights reserved.Legal|Privacy policy|Modern Slavery Act Transparency Statement|Sitemap|About US| Contact US: help@patsnap.com