Preparation method of carbon fiber liquid molded carbon fiber composite material with no halogen, low toxicity and high flame resistance
A technology of liquid molding and composite materials, which is applied in the field of preparation of halogen-free high flame-retardant resin-based carbon fiber composite materials, can solve the problems of flammability, large quantities, harmful gases, etc., and achieve the effect of excellent mechanical properties
- Summary
- Abstract
- Description
- Claims
- Application Information
AI Technical Summary
Problems solved by technology
Method used
Image
Examples
Embodiment 1
[0022] Option A
[0023] Add hexaphenoxycyclotriphosphazene into bisphenol F epoxy and novolac epoxy mixture and stir at 90±5°C until completely dissolved. After cooling to room temperature, add bisphenol A bis(diphenyl phosphate), m-benzene Stir the diphenol bis(diphenyl phosphate) and o-cresyl glycidyl ether until they are evenly mixed, and finally add the curing agent isophorone diamine, and mix evenly to obtain the resin system a.
[0024] The amount of each component in the resin system a:
[0025]
[0026] The composite material sheet was prepared by vacuum introduction process.
[0027] The carbon fiber twill fabric with an area density of 200gsm is selected as the reinforcement material; the carbon fiber fabric is cut and laid according to the requirements, and the auxiliary materials are laid and then vacuum bagged, vacuumed and the vacuum retention rate of the vacuum bag is tested. When the vacuum degree meets the requirements, carry out Glue injection.
[0028...
Embodiment 2
[0042] Plan C
[0043] Weigh bisphenol F epoxy and o-cresyl glycidyl ether, stir until mixed evenly, add curing agent isophorone diamine, mix evenly, and obtain resin system c.
[0044] The amount of each component in the resin system c:
[0045]
[0046] Composite sheets were prepared by RTM molding process.
[0047] The reinforcing material is carbon fiber twill fabric with an area density of 200gsm; the fabric is shaped by epoxy setting agent (the amount of epoxy setting agent per square meter is 50g), and the shaped carbon fiber fabric is cut and laid according to the requirements to make a prefabricated body, and According to the requirements of RTM process, the plastic injection plate is made.
[0048] After injection, heat up and solidify. The curing system is 50°C for 2h+120°C for 3h, and the heating rate is 1-2°C / min.
[0049] Plan D
[0050] Preparation of flame-retardant setting powder: Add ammonium molybdate, ammonium polyphosphate, zinc borate, and epoxy s...
PUM
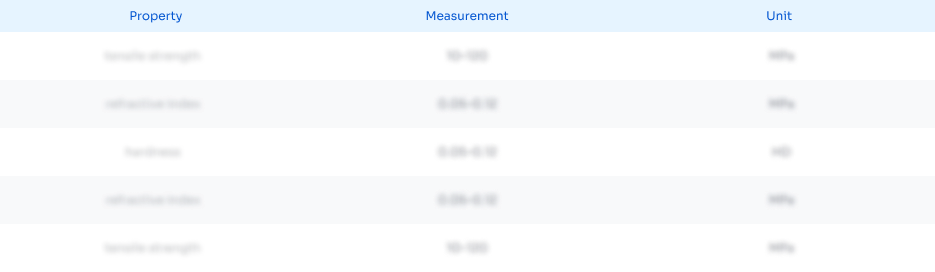
Abstract
Description
Claims
Application Information

- R&D
- Intellectual Property
- Life Sciences
- Materials
- Tech Scout
- Unparalleled Data Quality
- Higher Quality Content
- 60% Fewer Hallucinations
Browse by: Latest US Patents, China's latest patents, Technical Efficacy Thesaurus, Application Domain, Technology Topic, Popular Technical Reports.
© 2025 PatSnap. All rights reserved.Legal|Privacy policy|Modern Slavery Act Transparency Statement|Sitemap|About US| Contact US: help@patsnap.com