Long-life and low-foam emulsion for aluminium alloy cutting
A cutting and long-life technology, applied in the petroleum industry, lubricating compositions, etc., can solve the problems of poor corrosion inhibition effect of non-phosphorus and non-silicon aluminum corrosion inhibitors, increased cutting fluid foam, frequent alarms of machine tools, etc., to achieve improved Effects of aluminum corrosion inhibition ability and service life, improvement of lubricating ability, and improvement of alkali retention ability
- Summary
- Abstract
- Description
- Claims
- Application Information
AI Technical Summary
Problems solved by technology
Method used
Image
Examples
Embodiment 1
[0033] Add 1.5% of monoethanolamine, 13.5% of triethanolamine, 1% of isopropanolamine, 5% of diethanolamine borate, 1% of organic tribasic acid, 0.5% of aliphatic phosphate, silicon-containing aluminum corrosion inhibitor while stirring at room temperature. 0.2% of solvent, 8% of tap water, after stirring for 20 minutes, add 41% of naphthenic oil, 1% of inactive sulfurized olefin, 2% of fatty acid isopropanol ester, 2% of fatty alcohol polyoxyethylene ether (5EO / 2EO), 2% of sulfurized fat Ester 2.3% polyisobutylene succinamide 4%, castor oil polyoxyethylene ether 3%, Siben-80 6.1%, benzotriazole 0.1%, morpholine derivatives 4%, iodopropynylamino 0.5% butyl formate, 1.5% diethylene glycol ethyl ether, 1.5% dipropylene glycol methyl ether, after stirring for 20 minutes, add 0.3% of modified silicone defoamer, and stir for 30 minutes to obtain the finished product.
[0034] The emulsion prepared in this embodiment complies with the JB / T 7453 standard. This product has excellent ...
Embodiment 2
[0036] Add 2% of monoethanolamine, 9% of triethanolamine, 1% of isopropanolamine, 5% of diethanolamine borate, 0.5% of fatty phosphate, 0.2% of silicon-containing aluminum corrosion inhibitor, and 8% of tap water while stirring at room temperature After stirring for 20 minutes, add naphthenic oil 45%, inactive sulfurized olefin 1%, pentaerythritol tetraoleate 3%, fatty alcohol polyoxyethylene ether (5EO / 2EO) 5%, polyisobutylene succinic acid amide 4%, Castor oil polyoxyethylene ether 3%, Siben-80 5.4%, benzotriazole 0.1%, morpholine derivatives 4%, iodopropynyl butyl carbamate 0.5%, diethylene glycol ethyl ether 1.5% %, 1.5% of dipropylene glycol methyl ether, after stirring for 20 minutes, add 0.3% of modified silicone defoamer, and stir for 30 minutes to obtain the finished product.
[0037] The emulsion prepared in this embodiment complies with the JB / T 7453 standard. This product has excellent lubricating performance, and the tapping torque value is better than similar co...
PUM
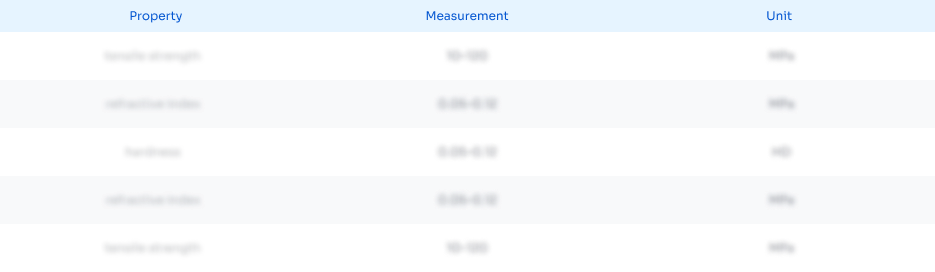
Abstract
Description
Claims
Application Information

- R&D
- Intellectual Property
- Life Sciences
- Materials
- Tech Scout
- Unparalleled Data Quality
- Higher Quality Content
- 60% Fewer Hallucinations
Browse by: Latest US Patents, China's latest patents, Technical Efficacy Thesaurus, Application Domain, Technology Topic, Popular Technical Reports.
© 2025 PatSnap. All rights reserved.Legal|Privacy policy|Modern Slavery Act Transparency Statement|Sitemap|About US| Contact US: help@patsnap.com