A preparation method of light rare earth complex modified sintered samarium cobalt magnet
A technology of samarium-cobalt magnets and complexes, applied in the fields of magnetic objects, inductors/transformers/magnets, magnetic materials, etc., can solve the problems of restricting industrial development, reducing coercive force value, and limited improvement of magnetic properties, reaching Cellular organization, improved magnetic performance, and improved magnetic energy product
- Summary
- Abstract
- Description
- Claims
- Application Information
AI Technical Summary
Problems solved by technology
Method used
Examples
Embodiment 1
[0017] 1) Smelting: Using samarium, cobalt, iron, copper, and zirconium with a purity greater than 99.94% as raw materials, under the protection of an inert gas, smelting to prepare an alloy composition of Sm: 18.5wt.%, Co: 62.6wt.%, Fe: 6.0 wt.%, Cu: 7.2wt.%, Zr: 5.7wt.% Sm-Co-Fe-Cu-Zr master alloy ingot;
[0018] 2) Powder making: crush the samarium-cobalt ingot into 160μm alloy coarse powder by jaw crusher and disc mill, and then crush the alloy coarse powder into 5μm samarium-cobalt alloy powder by jet milling method. While crushing, add the mixture of 2,5-di-tert-butylhydroquinone and tert-butylhydroxyanisole into the jet mill chamber by pouring, and the 2,5-di-tert-butylhydroquinone The weight ratio with tert-butyl hydroxyanisole is 1:0.2, and the blending amount of this mixture accounts for 0.1% of the total weight of samarium cobalt powder;
[0019] 3) Mixing material: the quaternary complex of lanthanide light rare earth (La, Pr) (NO 3 ) 2 (phen) 2 (CH 3 COCHCOCH...
Embodiment 2
[0029] 1) Smelting: Using samarium, cobalt, iron, copper, and zirconium with a purity greater than 99.94% as raw materials, under the protection of an inert gas, smelting to prepare an alloy composition of Sm: 21.0wt.%, Co: 60.1wt.%, Fe: 6.0 wt.%, Cu: 7.2wt.%, Zr: 5.7wt.% Sm-Co-Fe-Cu-Zr master alloy ingot;
[0030] 2) Powder making: crush the samarium-cobalt ingot into 180μm alloy coarse powder by jaw crusher and disc mill, and then crush the alloy coarse powder into 8μm samarium-cobalt alloy powder by jet mill While crushing, add the mixture of 2,5-di-tert-butylhydroquinone and isooctyl propionate into the jet mill chamber by pouring, 2,5-di-tert-butylhydroquinone The weight ratio with isooctyl propionate is 1:0.4, and the blending amount of this mixture accounts for 0.7% of the total weight of samarium cobalt powder;
[0031] 3) Mixing material: the non-methenyl light rare earth complex (Ce, Pm) (odpp) 3 (thf) 2 The mixed liquid with methyl acetate is added to the samariu...
Embodiment 3
[0041] 1) Smelting: Using samarium, cobalt, iron, copper, and zirconium with a purity greater than 99.94% as raw materials, under the protection of an inert gas, smelting to prepare an alloy composition of Sm: 23.5wt.%, Co: 57.6wt.%, Fe: 6.0 wt.%, Cu: 7.2wt.%, Zr: 5.7wt.% Sm-Co-Fe-Cu-Zr master alloy ingot;
[0042] 2) Powder making: crush the samarium-cobalt ingot into 200μm alloy coarse powder by jaw crusher and disc mill, and then crush the alloy coarse powder into 11μm samarium-cobalt alloy powder by jet mill While crushing, the mixture of 2,5-di-tert-butyl hydroquinone and pentaerythritol diphosphite is added to the jet mill chamber in a pouring manner, and 2,5-di-tert-butyl hydroquinone and The weight ratio of pentaerythritol diphosphite is 1:0.6, and the blending amount of this mixture accounts for 1.3% of the samarium cobalt powder gross weight;
[0043] 3) Mixing material: the lanthanide light rare earth quaternary complex (Nd,Eu)(NO 3 ) 2 (phen) 2 (CH 3 COCHCOCH ...
PUM
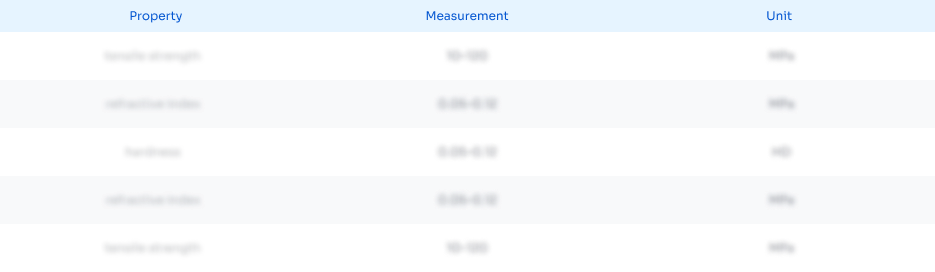
Abstract
Description
Claims
Application Information

- R&D
- Intellectual Property
- Life Sciences
- Materials
- Tech Scout
- Unparalleled Data Quality
- Higher Quality Content
- 60% Fewer Hallucinations
Browse by: Latest US Patents, China's latest patents, Technical Efficacy Thesaurus, Application Domain, Technology Topic, Popular Technical Reports.
© 2025 PatSnap. All rights reserved.Legal|Privacy policy|Modern Slavery Act Transparency Statement|Sitemap|About US| Contact US: help@patsnap.com