Corrugated roller machining method
A processing method and technology for corrugated rollers, applied in the processing field of corrugated rollers, can solve the problems of increased gear grinding workload, shortened service life, large internal stress of the corrugated roller, etc. The effect of solution strengthening
- Summary
- Abstract
- Description
- Claims
- Application Information
AI Technical Summary
Problems solved by technology
Method used
Examples
Embodiment 1
[0020] A processing method for a corrugated roller, the specific steps are as follows:
[0021] (1) Weigh by weight: 200 parts of alcohol, 60 parts of bentonite, 50 parts of silicon carbide, 10 parts of chromium oxide, 10 parts of rosin, 10 parts of silicon dioxide, 3 parts of titanium nitride, and 1 part of cerium dioxide;
[0022] (2) The roll body of the corrugated roll is quenched and tempered with 48CrMo material, the welding shaft head and the outer circle are rough-machined, and the diameter of the outer circle rough-machined is left with a margin of 0.4mm;
[0023] (3) Dissolve rosin in 80 parts of alcohol solution;
[0024] (4) Process bentonite, silicon carbide, chromium oxide, silicon dioxide, titanium nitride and cerium oxide into powders, the particle size of which is 0.05 μm, and put them into a mixer, add step (3) to get The rosin solution, then add the remaining alcohol and stir until the coating is evenly obtained;
[0025] (5) Use a spray gun to evenly spra...
Embodiment 2
[0030] A processing method for a corrugated roller, the specific steps are as follows:
[0031] (1) Weigh by weight: 210 parts of alcohol, 65 parts of bentonite, 55 parts of silicon carbide, 11 parts of chromium oxide, 10.5 parts of rosin, 11 parts of silicon dioxide, 3.5 parts of titanium nitride, and 1.2 parts of cerium oxide;
[0032] (2) The roller body of the corrugated roller is tempered with 48CrMo material, the welding shaft head and the outer circle are rough-machined, and the diameter of the outer circle rough-machined is left with a margin of 0.45mm;
[0033] (3) Dissolve rosin in 90 parts of alcohol solution;
[0034] (4) Process bentonite, silicon carbide, chromium oxide, silicon dioxide, titanium nitride, and cerium oxide into powders with a particle size of 0.2 μm, put them into a mixer, and add them to step (3) to obtain The rosin solution, then add the remaining alcohol and stir until the coating is evenly obtained;
[0035] (5) Use a spray gun to evenly spr...
Embodiment 3
[0040] A processing method for a corrugated roller, the specific steps are as follows:
[0041] (1) Weigh by weight: 220 parts of alcohol, 70 parts of bentonite, 60 parts of silicon carbide, 12 parts of chromium oxide, 12 parts of silicon dioxide, 11 parts of rosin, 4 parts of titanium nitride, and 1.5 parts of cerium dioxide;
[0042] (2) The roll body of the corrugated roll is quenched and tempered with 48CrMo material, the welding shaft head and the outer circle are rough-machined, and the diameter of the outer circle rough-machined is left with a margin of 0.5mm;
[0043] (3) Dissolve rosin in 100 parts of alcohol solution;
[0044] (4) Process bentonite, silicon carbide, chromium oxide, silicon dioxide, titanium nitride and ceria into powder, the particle size of which is 1.2 μm, and put it into the mixer, add step (3) to get The rosin solution, then add the remaining alcohol and stir until the coating is evenly obtained;
[0045] (5) Use a spray gun to evenly spray the...
PUM
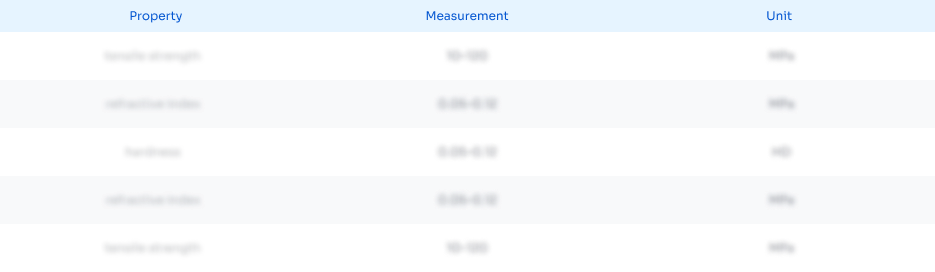
Abstract
Description
Claims
Application Information

- R&D
- Intellectual Property
- Life Sciences
- Materials
- Tech Scout
- Unparalleled Data Quality
- Higher Quality Content
- 60% Fewer Hallucinations
Browse by: Latest US Patents, China's latest patents, Technical Efficacy Thesaurus, Application Domain, Technology Topic, Popular Technical Reports.
© 2025 PatSnap. All rights reserved.Legal|Privacy policy|Modern Slavery Act Transparency Statement|Sitemap|About US| Contact US: help@patsnap.com