A kind of preparation method of copper-coated graphene reinforced copper-based electrical contact material
A technology of copper-coated graphene and electrical contact materials, which is applied to contact parts, metal/alloy conductors, non-metallic conductors, etc., can solve the problem of reducing the electrical and thermal conductivity of copper contact materials, and the difficulty in obtaining comprehensive performance of copper-based contacts Material and other issues, to achieve high hardness, improve interface wettability, high wear resistance
- Summary
- Abstract
- Description
- Claims
- Application Information
AI Technical Summary
Problems solved by technology
Method used
Image
Examples
Embodiment 1
[0028] (1) Copper-plated graphene is prepared by depositing metallic copper on the surface of graphene (layers 1-10) by DC magnetron sputtering. The copper target with a purity of 99.99% was ground with fine sandpaper to remove the surface oxide film before installation, then cleaned with acetone, dried, and pre-sputtered for 5 minutes before DC magnetron sputtering deposition to remove the metal oxide on the surface of the target. and other impurities to ensure the purity of the copper film deposited on the surface of the subsequent graphene. The process parameters of DC magnetron sputtering are: when the vacuum degree reaches 0.1*10 -3 When Pa, argon gas with a purity of 99.99% was introduced, the working pressure was 0.8Pa, the sputtering power was 80W, and the deposition time was 30min.
[0029] (2) Copper with a purity of 99.9% is smelted in an intermediate frequency furnace, and 0.05% rare earth cerium and 0.5% metal zinc are added to the copper melt. Below the surfac...
Embodiment 2
[0033] (1) Copper-plated graphene is made by depositing metallic copper on the surface of graphene (layers 1-10) by DC magnetron sputtering. The copper target with a purity of 99.99% was ground with fine sandpaper to remove the surface oxide film before installation, then washed with acetone, dried, and pre-sputtered for 5 minutes before DC magnetron sputtering deposition to remove the metal oxide on the surface of the target. and other impurities to ensure the purity of the copper film deposited on the surface of the subsequent graphene. The process parameters of DC magnetron sputtering are: when the vacuum degree reaches 1*10 -3 When Pa, argon gas with a purity of 99.99% was introduced, the working pressure was 1.5Pa, the sputtering power was 160W, and the deposition time was 5min.
[0034] (2) Copper with a purity of 99.9% is smelted in an intermediate frequency furnace, and the copper melt is added with 2.0% rare earth lanthanum and 5.0% metal zinc by weight. Below the ...
Embodiment 3
[0038] (1) Copper-plated graphene is made by depositing metallic copper on the surface of graphene (layers 1-10) by DC magnetron sputtering. The copper target with a purity of 99.99% was ground with fine sandpaper to remove the surface oxide film before installation, then washed with acetone, dried, and pre-sputtered for 5 minutes before DC magnetron sputtering deposition to remove the metal oxide on the surface of the target. and other impurities to ensure the purity of the copper film deposited on the surface of the subsequent graphene. The process parameters of DC magnetron sputtering are: when the vacuum degree reaches 0.3*10 -3 When Pa, argon gas with a purity of 99.99% was introduced, the working pressure was 1.0Pa, the sputtering power was 100W, and the deposition time was 15min.
[0039] (2) Copper with a purity of 99.9% is smelted in an intermediate frequency furnace. The copper melt is added with 0.5% rare earth lanthanum and 1.0% metal zinc by weight. The rare ear...
PUM
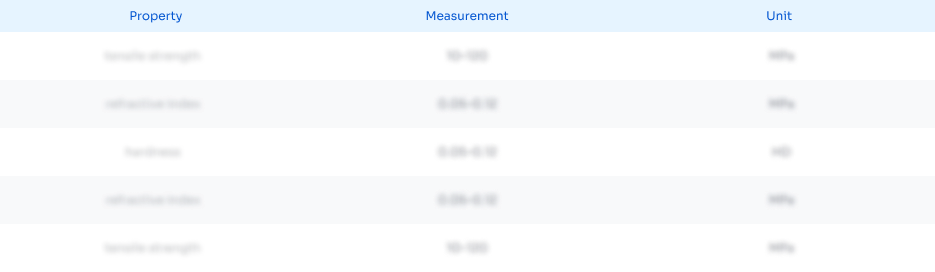
Abstract
Description
Claims
Application Information

- Generate Ideas
- Intellectual Property
- Life Sciences
- Materials
- Tech Scout
- Unparalleled Data Quality
- Higher Quality Content
- 60% Fewer Hallucinations
Browse by: Latest US Patents, China's latest patents, Technical Efficacy Thesaurus, Application Domain, Technology Topic, Popular Technical Reports.
© 2025 PatSnap. All rights reserved.Legal|Privacy policy|Modern Slavery Act Transparency Statement|Sitemap|About US| Contact US: help@patsnap.com