Halogen-free flame retardant high-tear-resistance wire and cable compound for electric vehicles and wire and cable production method
A wire and cable material and electric vehicle technology, applied in the direction of plastic/resin/wax insulators, organic insulators, etc., can solve the problems of loss of cable flexibility, cracking of cable sheath, and insufficient production efficiency, and achieve extrusion processing performance improvement, anti-corrosion Improved tear performance and reduced irreversible deformation
- Summary
- Abstract
- Description
- Claims
- Application Information
AI Technical Summary
Problems solved by technology
Method used
Examples
Embodiment 1
[0030] The formula consists of the following:
[0031] 100 copies of SEBS;
[0032] 30 parts of polypropylene;
[0033] POE15 copies;
[0034] Metallocene polyethylene (mPE) 5 parts;
[0035] Melamine cyanurate (MCA) 40 parts;
[0036] 25 parts of organic hypophosphite;
[0037] BDP35 copies;
[0038] Antioxidant 1010+1681 parts;
[0039] 2 parts of simethicone;
[0040] 40 parts of white oil.
[0041] The preparation steps are as follows:
[0042] Weigh the components according to the above formula, add them into a high-speed mixer, stir evenly, and then discharge to obtain a mixed material. The mixture is melt-extruded at 175-210°C through a twin-screw extruder with a relatively large length and diameter, drawn, cooled, and granulated to obtain a finished masterbatch of high tear-resistant halogen-free flame-retardant electric vehicle wire and cable material. The finished wire and cable material is extruded through a twin-screw extruder and a conductor (metal condu...
Embodiment 2
[0044] The formula consists of the following:
[0045] 100 copies of SEBS;
[0046] 60 parts of polypropylene;
[0047] POE10 copies;
[0048] 70 parts of organic hypophosphite;
[0049] RDP25 copies;
[0050] Antioxidant 10102 parts;
[0051] 3 parts of simethicone;
[0052] 65 parts of white oil.
[0053] The preparation steps are as follows:
[0054] Weigh the components according to the above formula, add them into a high-speed mixer, stir evenly, and then discharge to obtain a mixed material. The mixture is melt-extruded at 175-210°C through a twin-screw extruder with a relatively large length and diameter, drawn, cooled, and granulated to obtain a finished masterbatch of high tear-resistant halogen-free flame-retardant electric vehicle wire and cable material. The finished wire and cable material is extruded through a twin-screw extruder and a conductor (metal conductor such as copper or aluminum), and the obtained wire is irradiated and cross-linked by an electr...
Embodiment 3
[0056] The formula consists of the following:
[0057] 100 copies of SEBS;
[0058] 30 parts of polypropylene;
[0059] 10 copies of EVA;
[0060] mPE10 copies
[0061] MCA60 copies;
[0062] RDP30 copies;
[0063] Antioxidant 10101 parts;
[0064] 1.5 parts of polyethylene wax;
[0065] 30 parts of white oil.
[0066] The preparation steps are as follows:
[0067] Weigh the components according to the above formula, add them into a high-speed mixer, stir evenly, and then discharge to obtain a mixed material. The mixture is melt-extruded at 175-210°C through a twin-screw extruder with a relatively large length and diameter, drawn, cooled, and granulated to obtain a finished masterbatch of high tear-resistant halogen-free flame-retardant electric vehicle wire and cable material. The finished wire and cable material is extruded through a twin-screw extruder and a conductor (metal conductor such as copper or aluminum), and the obtained wire is irradiated and cross-linked b...
PUM
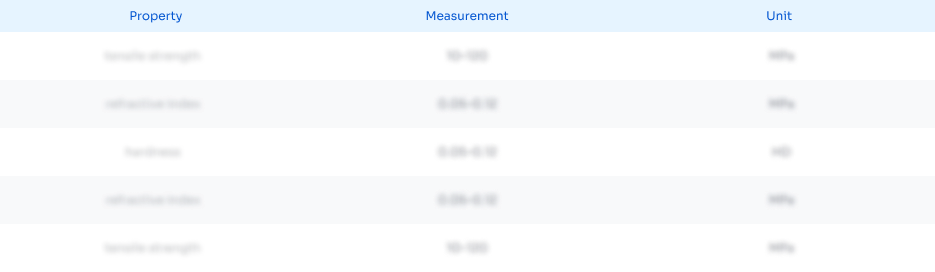
Abstract
Description
Claims
Application Information

- R&D Engineer
- R&D Manager
- IP Professional
- Industry Leading Data Capabilities
- Powerful AI technology
- Patent DNA Extraction
Browse by: Latest US Patents, China's latest patents, Technical Efficacy Thesaurus, Application Domain, Technology Topic, Popular Technical Reports.
© 2024 PatSnap. All rights reserved.Legal|Privacy policy|Modern Slavery Act Transparency Statement|Sitemap|About US| Contact US: help@patsnap.com