Optical substrate, semiconductor light-emitting element, and manufacturing method for same
A technology for light-emitting elements and light-emitting semiconductor layers, which is applied in the fields of semiconductor devices, semiconductor/solid-state device testing/measurement, electrical components, etc., and can solve problems such as the reduction of external quantum efficiency EQE, the reduction of internal quantum efficiency IQE, and the reduction of light extraction efficiency, etc. Achieve the effect of improving light extraction efficiency and electron injection efficiency EIE
- Summary
- Abstract
- Description
- Claims
- Application Information
AI Technical Summary
Problems solved by technology
Method used
Image
Examples
Embodiment 1
[0653]
[0654] An optical substrate PP having a pattern X drawn on its surface was produced, and a semiconductor light emitting element (LED) was produced using the substrate PP, and the efficiency of the LED was compared.
[0655] In the following studies, first (1) a cylindrical master mold was fabricated, and (2) a phototransfer method was applied to the cylindrical master mold to fabricate a resin mold. (3) Next, the resin mold is processed into a sheet for nanofabrication. Next, (4) A processing mask is formed on the optical substrate using a sheet for nanofabrication, dry etching is performed through the obtained processing mask, and an optical substrate PP having a concave-convex structure PP on the surface is produced. Finally, (5) using the obtained optical substrate PP, a semiconductor light-emitting element was produced, and performance was evaluated.
[0656] (a) Production of cylindrical master mold
[0657] A fine structure is formed on the cylindr...
Embodiment 2
[0746]
[0747] An optical substrate D having a concavo-convex structure D on the surface was prepared, and a semiconductor light emitting element (LED) was fabricated using the optical substrate D, and the efficiency of the LED was compared. At this time, the arrangement or shape of the concavo-convex structure is changed and controlled (standard deviation / arithmetic mean).
[0748] In the same manner as in Example 1, (1) a cylindrical mother mold was produced, and (2) a resin mold was produced. (3) Then, using a resin mold, a member for nanofabrication (sheet for nanofabrication) is produced. Next, (4) Using the sheet for nanofabrication, a concavo-convex structure is formed on the surface of the optical substrate. Finally, (5) using the obtained optical substrate D having the concavo-convex structure D, a semiconductor light-emitting element was produced, and performance was evaluated. In addition, the (standard deviation / arithmetic mean) of the concave-convex str...
Embodiment 3
[0772]
[0773] (Production of cylindrical master mold)
[0774] As the base material of the cylindrical master mold, a cylindrical quartz glass roll with a diameter of 80 mm and a length of 50 mm was used. On the surface of this cylindrical quartz glass roll, a fine structure (fine concavo-convex structure) was formed by a direct write lithography method using a semiconductor pulse laser as follows.
[0775] First, a resist layer is formed on the fine structure of the quartz glass surface by a sputtering method. The sputtering method was performed using CuO (containing 8 atm% Si) as a target (resist layer) and with RF 100W power. The film thickness of the resist layer after film formation was 20 nm. The cylindrical mold produced as above was exposed on the following conditions while rotating at a linear velocity s=1.0 m / sec.
[0776] Semiconductor laser wavelength for exposure: 405nm
[0777] Exposure laser power: 3.5mW
[0778] X-axis pitch Px: 398nm
...
PUM
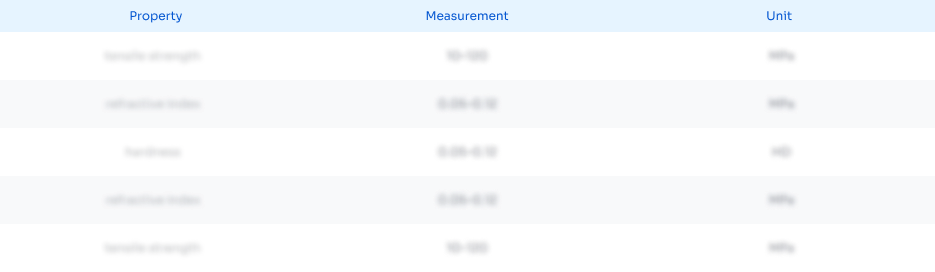
Abstract
Description
Claims
Application Information

- R&D
- Intellectual Property
- Life Sciences
- Materials
- Tech Scout
- Unparalleled Data Quality
- Higher Quality Content
- 60% Fewer Hallucinations
Browse by: Latest US Patents, China's latest patents, Technical Efficacy Thesaurus, Application Domain, Technology Topic, Popular Technical Reports.
© 2025 PatSnap. All rights reserved.Legal|Privacy policy|Modern Slavery Act Transparency Statement|Sitemap|About US| Contact US: help@patsnap.com