Ceramized polyolefin material and preparation method thereof
A technology for ceramicizing polyolefin and ceramic powder, applied in the field of wire and cable materials, can solve the problems of high processing temperature, low residual strength, unfavorable enlargement production, etc. Effect
- Summary
- Abstract
- Description
- Claims
- Application Information
AI Technical Summary
Problems solved by technology
Method used
Image
Examples
Embodiment 1
[0020] 100 parts of ethylene-α-propylene copolymer weighed in parts by weight, porcelain powder A is attapulgite 180 parts, porcelain powder B is 15 parts of borax and ammonium borate 15 parts, porcelain powder C is gas phase white 120 parts of carbon black, 8 parts of stearic acid as lubricant and 10100.3 parts of antioxidant are put into the internal mixer for mixing (also called banburying). Introduce the twin-screw extruder to melt extrusion, the temperature of the first zone to the ninth zone of the twin-screw extruder is 60°C in the first zone, 70°C in the second zone, 80°C in the third zone, 85°C in the fourth zone, and 90°C in the fifth zone. The sixth zone is 90°C, the seventh zone is 90°C, the eighth zone is 95°C, the ninth zone is 95°C, and the head temperature is 100°C. After exiting the twin-screw extruder, the ceramic polyolefin material is obtained by cold cutting.
Embodiment 2
[0022] 50 parts of ethylene-alpha-butene copolymer, 25 parts of ethylene-alpha-octene copolymer, 25 parts of ethylene-alpha-hexene copolymer, 50 parts of vitrified powder A, namely glass fiber, weighed in parts by weight , 50 parts of alumina nanotubes and 50 parts of calcium carbonate whiskers, porcelain powder B is 60 parts of borax, porcelain powder C is high-purity quartz powder and quartz glass powder 100 parts each, lubricant is calcium stearate and hard 20 parts of zinc fatty acid, 0.5 parts of antioxidant 168 and 0.5 parts of antioxidant 300 are put into the internal mixer for mixing (also called banburying). Introduce twin-screw extruder for melt extrusion, the temperature of zone 1 to zone 9 of twin-screw extruder is 50°C in zone 1, 65°C in zone 2, 70°C in zone 3, 80°C in zone 4, 95°C in zone 5, The sixth zone is 95°C, the seventh zone is 95°C, the eighth zone is 95°C, the ninth zone is 90°C, and the head temperature is 95°C. After exiting the twin-screw extruder, it...
Embodiment 3
[0024] 100 parts of ethylene-α-octene copolymer weighed in parts by weight, porcelain powder A is 50 parts of sericite, 25 parts of muscovite and 25 parts of phlogopite, porcelain powder B is low-melting phosphate glass powder Or 100 parts of low-melting borate glass powder, 100 parts of porcelain powder C, that is, precipitated white carbon black, 2.5 parts of lubricant, namely octyl stearate, 2.5 parts of liquid paraffin and 10760.3 parts of antioxidant, are put into the internal mixer for mixing (It can also be called internal mixing). When the temperature is 105°C, the material is discharged and introduced into the twin-screw extruder through the conical feeding hopper for melt extrusion. The temperatures of the first to ninth areas of the twin-screw extruder are respectively one Zone 55°C, Zone 2 60°C, Zone 3 75°C, Zone 4 90°C, Zone 5 92°C, Zone 6 92°C, Zone 7 92°C, Zone 8 92°C, Zone 9 92°C, Head Temperature 98°C, After exiting the twin-screw extruder, it is cold-cut to o...
PUM
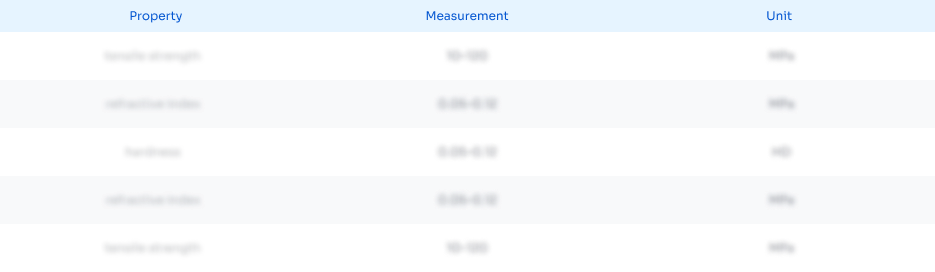
Abstract
Description
Claims
Application Information

- Generate Ideas
- Intellectual Property
- Life Sciences
- Materials
- Tech Scout
- Unparalleled Data Quality
- Higher Quality Content
- 60% Fewer Hallucinations
Browse by: Latest US Patents, China's latest patents, Technical Efficacy Thesaurus, Application Domain, Technology Topic, Popular Technical Reports.
© 2025 PatSnap. All rights reserved.Legal|Privacy policy|Modern Slavery Act Transparency Statement|Sitemap|About US| Contact US: help@patsnap.com