Antiwear antifriction composite additive for lubricating oil (grease)
A technology of grease and composite powder, which is applied in the field of nano-rare earth oxide-coated ultrafine muscovite composite powder and its preparation, can solve problems such as unstable surface friction performance, achieve chemical reaction speed, increase surface area, The effect of increasing the diffusion speed
- Summary
- Abstract
- Description
- Claims
- Application Information
AI Technical Summary
Problems solved by technology
Method used
Image
Examples
Embodiment 1
[0030] In this embodiment, 800 mesh muscovite is used as raw material, the reaction system is cerium chloride, and the ligand is oxalic acid. The process flow is as follows figure 1 As shown, there are the following steps in sequence:
[0031] 1. Ingredients
[0032] Weigh 0.95mol muscovite, 0.05mol cerium chloride, 0.1mol oxalic acid
[0033] 2. Mixing
[0034] Mix the weighed muscovite, cerium chloride and oxalic acid until uniform;
[0035] 3. Preparation of precursors by ball milling chemical reaction at room temperature
[0036]The uniformly mixed muscovite, cerium chloride and oxalic acid are ball milled at room temperature and normal pressure, so that they react to form precursors under the mechanical shear force and impact force generated during the ball milling process. The speed of the ball mill is 300 rpm Minutes, ball milling for 60 minutes can completely react cerium chloride and oxalic acid to form the precursor cerium oxalate, which is evenly distributed on ...
Embodiment 2
[0046] In this embodiment, 800 mesh muscovite is used as raw material, the reaction system is lanthanum chloride, and the ligand is oxalic acid. The process flow is as follows figure 1 As shown, there are the following steps in sequence
[0047] 1. Ingredients
[0048] Weigh 0.98mol muscovite, 0.02mol lanthanum chloride, 0.06mol oxalic acid
[0049] 2. Mixing
[0050] Mix the weighed muscovite, lanthanum chloride and oxalic acid until uniform;
[0051] 3. Preparation of precursors by ball milling chemical reaction at room temperature
[0052] The uniformly mixed muscovite, lanthanum chloride and oxalic acid are ball milled at room temperature and normal pressure, so that they react to form precursors under the mechanical shear force and impact force generated during the ball milling process. The speed of the ball mill is 400 rpm. Minutes, 40 minutes of ball milling can make lanthanum chloride and oxalic acid completely react to form precursor lanthanum oxalate, which is ev...
Embodiment 3
[0062] In this embodiment, 800 mesh muscovite is used as raw material, the reaction system is cerium nitrate, and the ligand is ammonium bicarbonate. The process flow is as follows figure 1 As shown, there are the following steps in sequence
[0063] 1. Ingredients
[0064] Weigh 0.90mol muscovite, 0.10mol cerium nitrate, 0.6mol ammonium bicarbonate
[0065] 2. Mixing
[0066] Mix the weighed muscovite, cerium nitrate and ammonium bicarbonate until uniform;
[0067] 3. Preparation of precursors by ball milling chemical reaction at room temperature
[0068] The uniformly mixed muscovite, cerium nitrate and ammonium bicarbonate are ball milled at room temperature and normal pressure, so that they react to form precursors under the action of mechanical shear force and impact force generated during the ball milling process. The speed of the ball mill is 250 rpm / min, 80 minutes of ball milling can make cerium nitrate and ammonium bicarbonate completely react to form precursor ...
PUM
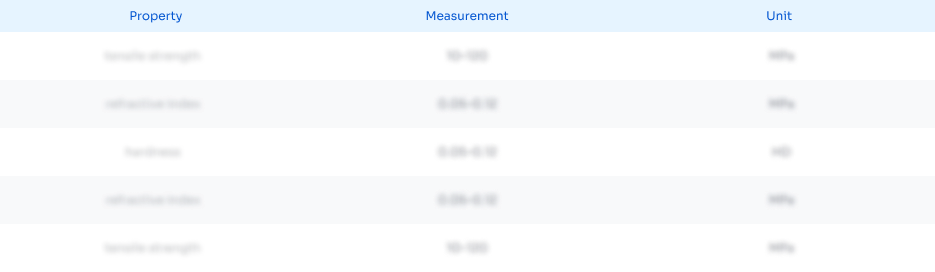
Abstract
Description
Claims
Application Information

- R&D
- Intellectual Property
- Life Sciences
- Materials
- Tech Scout
- Unparalleled Data Quality
- Higher Quality Content
- 60% Fewer Hallucinations
Browse by: Latest US Patents, China's latest patents, Technical Efficacy Thesaurus, Application Domain, Technology Topic, Popular Technical Reports.
© 2025 PatSnap. All rights reserved.Legal|Privacy policy|Modern Slavery Act Transparency Statement|Sitemap|About US| Contact US: help@patsnap.com