Preparation method of yttrium tungstate powder as negative expanding material
A negative expansion material, yttrium tungstate technology, applied in chemical instruments and methods, tungsten compounds, inorganic chemistry, etc., can solve the problems of unsuitability for large-scale production, complex synthesis process, high equipment requirements, etc., to achieve the purity of green products, Simple synthesis process and simple equipment requirements
- Summary
- Abstract
- Description
- Claims
- Application Information
AI Technical Summary
Problems solved by technology
Method used
Image
Examples
Embodiment 1
[0023] The preparation method of the present embodiment comprises the following steps:
[0024] Step 1. Mix 22.6g of yttrium oxide powder and 69.6g of tungsten trioxide powder evenly by wet ball milling, dry and grind to obtain a raw material mixture; the wet ball milling method is: add yttrium oxide powder and tungsten trioxide After adding ethanol to the tungsten powder, wet mix it in a planetary ball mill for 3 hours, the ball-to-material ratio of the planetary ball mill is 5:1, and the rotating speed is 300r / min;
[0025] Step 2. The raw material mixture described in step 1 is placed in a muffle furnace for roasting treatment, and after being cooled in the furnace, it is crushed and ground to obtain a roasted product; the temperature of the roasting treatment is 1100° C., and the time is 9 hours;
[0026] Step 3, placing the roasted product described in step 2 in a muffle furnace for secondary roasting, crushing and grinding after cooling with the furnace, to obtain a seco...
Embodiment 2
[0030] The preparation method of the present embodiment comprises the following steps:
[0031] Step 1. Mix 11.3g of yttrium oxide powder and 34.8g of tungsten trioxide powder evenly by wet ball milling, dry and grind to obtain a raw material mixture; the method of wet ball milling is: add yttrium oxide powder and tungsten trioxide After adding ethanol to the tungsten powder, wet mix it in a planetary ball mill for 4 hours, the ball-to-material ratio of the planetary ball mill is 4:1, and the rotating speed is 180r / min;
[0032] Step 2. The raw material mixture described in step 1 is placed in a muffle furnace for roasting treatment, and after being cooled in the furnace, it is crushed and ground to obtain a roasted product; the temperature of the roasting treatment is 1200° C., and the time is 10 hours;
[0033] Step 3, placing the roasted product described in step 2 in a muffle furnace for secondary roasting, crushing and grinding after cooling with the furnace, to obtain a ...
Embodiment 3
[0037] The preparation method of the present embodiment comprises the following steps:
[0038] Step 1. Mix 11.3g of yttrium oxide powder and 34.8g of tungsten trioxide powder evenly by wet ball milling, dry and grind to obtain a raw material mixture; the method of wet ball milling is: add yttrium oxide powder and tungsten trioxide After adding ethanol to the tungsten powder, wet mix it in a planetary ball mill for 2 hours, the ball-to-material ratio of the planetary ball mill is 6:1, and the speed is 400r / min;
[0039] Step 2. The raw material mixture described in step 1 is placed in a muffle furnace for roasting treatment, and after being cooled in the furnace, it is crushed and ground to obtain a roasted product; the temperature of the roasting treatment is 1050° C., and the time is 8 hours;
[0040] Step 3, placing the roasted product described in step 2 in a muffle furnace for secondary roasting, crushing and grinding after cooling with the furnace, to obtain a secondary ...
PUM
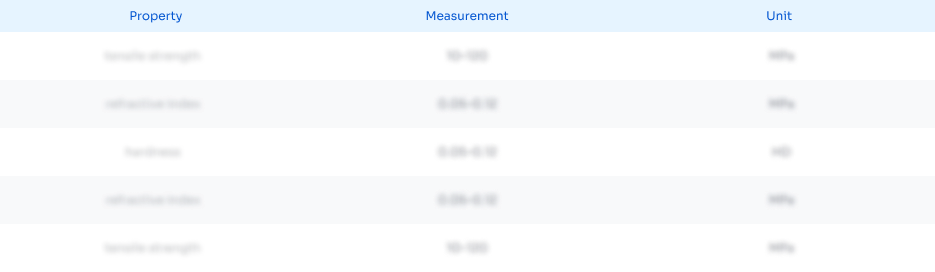
Abstract
Description
Claims
Application Information

- R&D Engineer
- R&D Manager
- IP Professional
- Industry Leading Data Capabilities
- Powerful AI technology
- Patent DNA Extraction
Browse by: Latest US Patents, China's latest patents, Technical Efficacy Thesaurus, Application Domain, Technology Topic, Popular Technical Reports.
© 2024 PatSnap. All rights reserved.Legal|Privacy policy|Modern Slavery Act Transparency Statement|Sitemap|About US| Contact US: help@patsnap.com