Composition solution for electric nickel-plating on surface of magnesium alloy
A technology of electroplating nickel and magnesium alloys, applied in the field of electroplating, can solve problems such as complex process, poor repeatability, and environmental pollution, and achieve the effects of high corrosion resistance, beautiful appearance, and high bonding force
- Summary
- Abstract
- Description
- Claims
- Application Information
AI Technical Summary
Problems solved by technology
Method used
Examples
Embodiment 1
[0012] A combined solution for electroplating nickel on the surface of magnesium alloy. The combined solution includes a zinc immersion bath, an electrogalvanizing bath and an electroplating nickel bath. The composition of the zinc immersion bath is 32 g / L zinc sulfate, 210 g / L potassium pyrophosphate, and carbonic acid. Sodium 8g / L, potassium fluoride 5g / L; ammonium bifluoride 2g / L, the balance is water; the composition of the electrogalvanizing bath: ZnSO 4 ·7H 2 O32g / L, K 4 P 2 O 7 ·3H 2 O168g / L, KF18g / L, C 6 H 17 O 7 N 3 32g / L, phytic acid 0.6g / L, H 2 CSNH 2 :4g / L, the balance is water; the composition of the nickel electroplating bath is: nickel sulfate 250g / L, nickel chloride 35g / L, boric acid 52g / L, potassium sulfate 26g / L, sodium lauryl sulfonate 0.5g / L, anhydrous sodium acetate 40g / L, ethoxylated butynediol 30mg / L, propionic acid 4g / L, the balance is water.
Embodiment 2
[0014] A combined solution for electroplating nickel on the surface of magnesium alloy. The combined solution includes a zinc dipping solution, an electro-galvanizing solution and an electro-nickel plating solution. The composition of the zinc dipping solution is 36 g / L zinc sulfate, 200 g / L potassium pyrophosphate, and carbonic acid. Sodium 10g / L, potassium fluoride 3g / L; ammonium bifluoride 3g / L, the balance is water; the composition of the electro-galvanizing bath: ZnSO 4 ·7H 2 O36g / L, K 4 P 2 O 7 ·3H 2 O164g / L, KF20g / L, C 6 H 17 O 7 N 3 32g / L, phytic acid 0.6g / L, H 2 CSNH 2 :4g / L, the balance is water; the composition of the electroplating nickel plating solution is: nickel sulfate 270g / L, nickel chloride 25g / L, boric acid 56g / L, potassium sulfate 20g / L, sodium lauryl sulfonate 1.5g / L, anhydrous sodium acetate 36g / L, ethoxylated butynediol 40mg / L, propionic acid 3g / L, the balance is water.
Embodiment 3
[0016] A combined solution for electroplating nickel on the surface of magnesium alloy. The combined solution includes a zinc dipping solution, an electro-galvanizing solution and an electro-nickel plating solution. The zinc dipping solution consists of 34 g / L zinc sulfate, 205 g / L potassium pyrophosphate, and carbonic acid. Sodium 9g / L, potassium fluoride 4g / L; ammonium bifluoride 2.5g / L, the balance is water; the composition of the electrogalvanizing bath: ZnSO 4 ·7H 2 O34g / L, K 4 P 2 O 7 ·3H 2 O166g / L, KF19g / L, C 6 H 17 O 7 N 3 33g / L, phytic acid 0.5g / L, H 2 CSNH 2 :5g / L, the balance is water; the composition of the nickel electroplating bath is: nickel sulfate 260g / L, nickel chloride 30g / L, boric acid 54g / L, potassium sulfate 23g / L, sodium lauryl sulfonate 1.0g / L, anhydrous sodium acetate 38g / L, ethoxylated butynediol 35mg / L, propionic acid 3.5g / L, the balance is water.
PUM
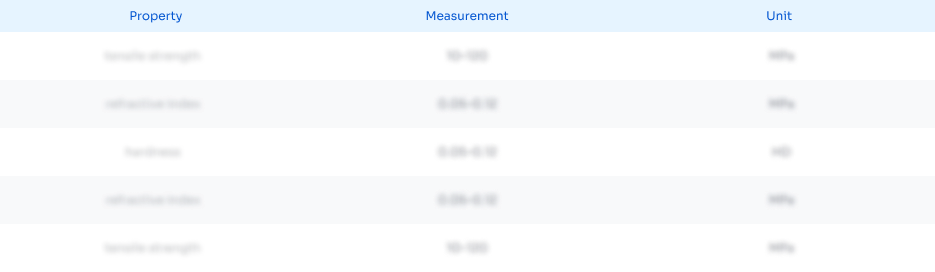
Abstract
Description
Claims
Application Information

- Generate Ideas
- Intellectual Property
- Life Sciences
- Materials
- Tech Scout
- Unparalleled Data Quality
- Higher Quality Content
- 60% Fewer Hallucinations
Browse by: Latest US Patents, China's latest patents, Technical Efficacy Thesaurus, Application Domain, Technology Topic, Popular Technical Reports.
© 2025 PatSnap. All rights reserved.Legal|Privacy policy|Modern Slavery Act Transparency Statement|Sitemap|About US| Contact US: help@patsnap.com