Non-silicone magnesium alloy pressure casting mould release agent
A release agent and magnesium alloy technology, applied in the field of magnesium alloy die-casting, can solve the problems of difficult transportation and management, high product cost, and affecting the surface treatment of parts, so as to reduce the number of times of mold wiping, reduce production costs, and prolong the service life. Effect
- Summary
- Abstract
- Description
- Claims
- Application Information
AI Technical Summary
Problems solved by technology
Method used
Examples
example 1
[0041] 1) In this implementation case, the mass percentages of the following components are taken as:
[0042] Saturated polyol 16%
[0043] Polyisobutylene 6%
[0045] Alkyl alcohol polyoxyethylene ether 4%
[0046] Alkylphenol Ethoxylate 7%
[0047] Triethanolamine 8%
[0048] C11~C14 dibasic acid 6%
[0049] Water-soluble special corrosion inhibitor for magnesium alloy 3%
[0050] Diethylene glycol 2%
[0051] Deionized demineralized water 43%
[0052] 2) Preparation steps:
[0053] In the blending tank A, add saturated polyol ester and polyisobutylene according to the amount, raise the temperature to 100°C under stirring, keep the temperature constant for 20 minutes until the material is evenly stirred, and stop heating;
[0054] In the blending tank B, add deionized water, diethylene glycol, magnesium alloy water-soluble special corrosion inhibitor, C11-C14 dibasic acid, triethanolamine according to the amount, and stir at room tempe...
example 2
[0057] 1) In this implementation case, the mass percentages of the following components are taken as:
[0058] Trimethylolpropane complex ester 15%
[0059] Ethylene propylene copolymer 7%
[0060] Alkyl alcohol polyoxyethylene ether 4%
[0061] Alkylphenol Ethoxylate 6%
[0062] Polyethylene Glycol Oleate 5%
[0063] Triethanolamine 6%
[0064]Sebacic acid 4%
[0065] Water-soluble special corrosion inhibitor for magnesium alloy 3%
[0066] Diethylene glycol 4%
[0067] Deionized demineralized water 46%
[0068] 2) Preparation steps:
[0069] In the blending tank A, add trimethylolpropane compound ester and ethylene-propylene copolymer according to the amount, raise the temperature to 100°C under stirring, keep the temperature constant for 30 minutes until the material is evenly stirred, and stop heating;
[0070] In the blending tank B, add deionized water, diethylene glycol, magnesium alloy water-soluble special corrosion inhibitor, decanedicarbon, triethanolamine ...
example 3
[0073] 1) In this implementation case, the mass percentages of the following components are taken as:
[0074] Pentaerythritol complex ester 13%
[0075] Polyacrylate 6%
[0076] Alkyl alcohol polyoxyethylene ether 5%
[0077] Alkylphenol Ethoxylate 7%
[0078] Polyethylene glycol laurate 8%
[0079] Triisopropanolamine 8%
[0080] Sebacic acid 5%
[0081] Water-soluble corrosion inhibitor for magnesium alloy 5%
[0082] Glycerol 5%
[0083] Deionized demineralized water 38%
[0084] 2) Preparation process
[0085] In the blending tank A, add pentaerythritol complex ester and polyacrylate according to the amount, heat up to 100 ℃ under stirring, keep the temperature for 30 minutes until the material is evenly stirred, and stop heating;
[0086] In the blending tank B, add deionized water, glycerol, magnesium alloy water-soluble special corrosion inhibitor, sebacic acid, triisopropanolamine according to the amount, and stir at room temperature for 30 minutes until the ...
PUM
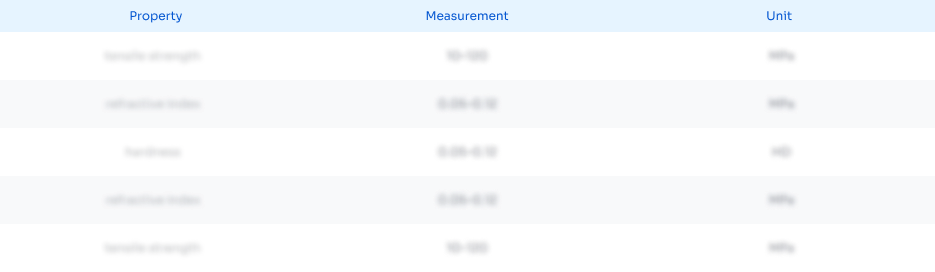
Abstract
Description
Claims
Application Information

- R&D
- Intellectual Property
- Life Sciences
- Materials
- Tech Scout
- Unparalleled Data Quality
- Higher Quality Content
- 60% Fewer Hallucinations
Browse by: Latest US Patents, China's latest patents, Technical Efficacy Thesaurus, Application Domain, Technology Topic, Popular Technical Reports.
© 2025 PatSnap. All rights reserved.Legal|Privacy policy|Modern Slavery Act Transparency Statement|Sitemap|About US| Contact US: help@patsnap.com