Method for extracting molybdenum and nickel and enriching precious metals from nickel and molybdenum ores
A technology for nickel-molybdenum ore and precious metals, which is applied in the field of high-efficiency extraction of molybdenum and nickel and enrichment of precious metals, can solve the problems of limited use, reduced yield of molybdenum and nickel, and small processing capacity, achieves high comprehensive utilization rate, and is beneficial to The effect of extracting and reducing nickel content in slag
- Summary
- Abstract
- Description
- Claims
- Application Information
AI Technical Summary
Problems solved by technology
Method used
Examples
Embodiment 1
[0034] The nickel-molybdenum ore used contains 3.0% molybdenum, 4.2% nickel, 21.5% sulfur, 10% carbon, 12.6% iron, 16.5% SiO2, 6.5% CaO, Ag20g / t, Au+Pd+Pt3g / t.
[0035] The nickel-molybdenum ore is ground to a particle size of ≤1mm, and oxidized and roasted at 600°C, and the obtained roasted clinker contains 9% S. The flue gas produced by oxidation roasting is used to make sulfuric acid.
[0036] Grind the agglomerated roasted clinker to a particle size of ≤1mm, and then add sodium carbonate and coke powder with a particle size of ≤1mm (fixed carbon content>80% ) and mix thoroughly, and then make the mixture into pellets of about Ф30. After the pellets are dried (moisture content below 2%), they are sent to an electric furnace for melting at 1280°C, and the furnace is kept warm for 20 minutes after all the furnace materials are melted. Under the condition of heat preservation, the reaction mixture is layered due to different densities, the upper layer is alkali slag, and the...
Embodiment 2
[0039] The nickel-molybdenum ore used contains 3.0% molybdenum, 4.2% nickel, 21.5% sulfur, 10% carbon, 12.6% iron, SiO 2 16.5%, CaO6.5%, Ag20g / t, Au+Pd+Pt3g / t.
[0040] The nickel-molybdenum ore is ground to a particle size of ≤1mm, and oxidized and roasted at 800°C, and the obtained roasted clinker contains 3% S. The flue gas produced by oxidation roasting is used to make sulfuric acid.
[0041] Grind the agglomerated roasted clinker to a particle size of ≤1mm, and then add sodium carbonate and coke powder with a particle size of ≤1mm (fixed carbon content >80% ) and mix thoroughly, and then make the mixture into pellets of about Ф30. After the pellets are dried, the water content is less than 2%, and they are sent to the electric furnace for melting at 1550°C, and the heat preservation is kept for 40 minutes after the furnace materials are completely melted. The obtained smelted nickel matte contains 31% nickel, 6% sulfur, 55% Fe, 0.3% Mo, 126g / t Ag, and 18g / t Au+Pd+Pt. ...
Embodiment 3
[0044] The nickel-molybdenum ore used contains 3.0% molybdenum, 4.2% nickel, 21.5% sulfur, 10% carbon, 12.6% iron, 16.5% SiO2, 6.5% CaO, Ag20g / t, Au+Pd+Pt3g / t.
[0045] The nickel-molybdenum ore is ground to a particle size of ≤1mm, oxidized and roasted at 700°C, and the obtained roasted clinker contains 7% S. The flue gas produced by oxidation roasting is used to make sulfuric acid.
[0046] Grind the agglomerated roasted clinker to a particle size of ≤1mm, and then add sodium carbonate and coke powder with a particle size of ≤1mm (fixed carbon content>80% ) and mix thoroughly, and then make the mixture into pellets of about Ф30. After the pellets are dried, they are sent to an electric furnace for melting at 1400°C, and the heat is kept for 30 minutes after all the furnace materials are melted. The obtained smelted nickel matte contains 35% nickel, 30% sulfur, 28% Fe, 0.2% Mo, 140g / t Ag, and 20g / t Au+Pd+Pt.
[0047] The obtained alkali slag was leached twice with water at...
PUM
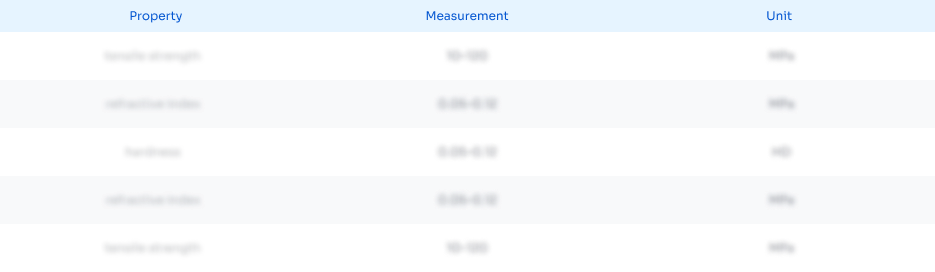
Abstract
Description
Claims
Application Information

- R&D
- Intellectual Property
- Life Sciences
- Materials
- Tech Scout
- Unparalleled Data Quality
- Higher Quality Content
- 60% Fewer Hallucinations
Browse by: Latest US Patents, China's latest patents, Technical Efficacy Thesaurus, Application Domain, Technology Topic, Popular Technical Reports.
© 2025 PatSnap. All rights reserved.Legal|Privacy policy|Modern Slavery Act Transparency Statement|Sitemap|About US| Contact US: help@patsnap.com