Production method of automobile interior trim panels made of natural fiber/thermoplastic resin composite materials
A thermoplastic resin and automotive interior panel technology, which is applied in synthetic resin layered products, chemical instruments and methods, layered products, etc. Lack of integrated planning of composite material preparation and molding processing to achieve the effect of automation and good rheological properties
- Summary
- Abstract
- Description
- Claims
- Application Information
AI Technical Summary
Problems solved by technology
Method used
Examples
Embodiment 1
[0024] Step 1: Prepare the surface layer
[0025] 30kg of polyester fiber, 20kg of spandex fiber, 30kg of polypropylene fiber, and 408020kg of hot melt fiber are controlled and fed, and the mixed fiber is opened in the opener. The mixed and opened fibers are combined by the screen and the laying curtain to form a fiber web with a certain thickness. After laying the curtain and forming a net, the fiber enters the oven, and there is a linear reciprocating spraying device at the entrance of the oven and the second layer of the oven. The spraying method is used to spray the phosphorus-nitrogen flame retardant guanidine phosphate and the organic silicon quaternary ammonium salt antibacterial agent on the fiber mat DC-5700 mixed liquid. Afterwards, the fiber mat is shaped by hot pressing rollers and finally cut and reeled.
[0026] Step 2: Prepare the core layer
[0027] Dissolve maleic anhydride as an esterification reagent in xylene solvent, weigh a certain amount of hemp fiber into t...
Embodiment 2
[0031] Step 1: Prepare the surface layer
[0032] 40kg of polyester fiber, 20kg of spandex fiber, 22kg of polypropylene fiber, and 408016kg of hot melt fiber are controlled and fed, and the mixed fiber is opened in the opener. The mixed and opened fibers are combined with a screen and a curtain to form a fiber web with a certain thickness. The fibers that are made into a net by the laying machine enter the needle punching machine, and the up and down reciprocating cloud tops of the needle punch of the needle punching machine make the fibers entangled. After the needle punching machine, it enters the oven. There is a linear reciprocating spraying device at the entrance of the oven and the second layer of the oven. The fiber mat is sprayed with the phosphorus-nitrogen flame retardant guanidine phosphate and the organic silicon quaternary ammonium salt antibacterial agent DC-5700. Mixture. Finally cut and rewind.
[0033] Step 2: Prepare the core layer
[0034] Dissolve maleic anhyd...
PUM
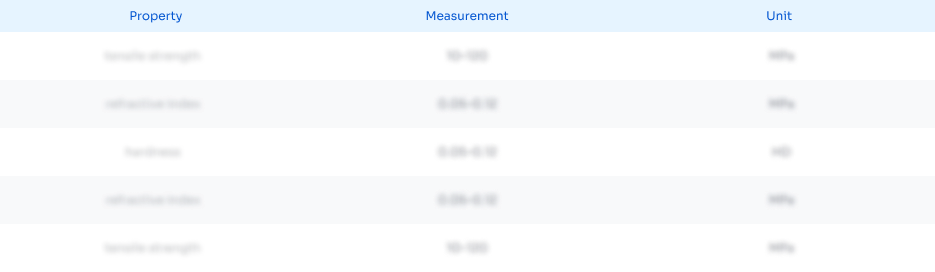
Abstract
Description
Claims
Application Information

- R&D Engineer
- R&D Manager
- IP Professional
- Industry Leading Data Capabilities
- Powerful AI technology
- Patent DNA Extraction
Browse by: Latest US Patents, China's latest patents, Technical Efficacy Thesaurus, Application Domain, Technology Topic, Popular Technical Reports.
© 2024 PatSnap. All rights reserved.Legal|Privacy policy|Modern Slavery Act Transparency Statement|Sitemap|About US| Contact US: help@patsnap.com