A kind of gel ultrasonic vibration forming method of metal parts
A technology of ultrasonic vibration and components, which is applied in the field of metal powder forming, can solve the problems of high requirements, and achieve the effect of increasing solid content, increasing bulk density and eliminating air bubbles
- Summary
- Abstract
- Description
- Claims
- Application Information
AI Technical Summary
Problems solved by technology
Method used
Examples
Embodiment 1
[0014] Implementation Example 1: Titanium products formed by gel ultrasonic vibration.
[0015] 1. Mix 90ml hydroxyethyl methacrylate and 270ml toluene, add 0.03g benzoyl peroxide;
[0016] 2. Add titanium hydride powder with an average particle size of 5 μm into the premix, then add 3.6ml of oleic acid and 3.6ml of polyethylene glycol-400, and stir evenly to obtain a stable slurry;
[0017] 3. Add 3.6ml of dimethylaniline, stir quickly and evenly, inject into the ultrasonic vibration mold, and vibrate continuously at 20KHz for 5 minutes;
[0018] 4. After the shaking, take out the green body from the mold, and dry it in an electric blast drying oven at 70°C for 1 hour. The finally obtained green body has no pore defects and has a solid content of 54vol.%.
Embodiment 2
[0019] Implementation example 2: gel ultrasonic vibration forming stainless steel products.
[0020] 1. Mix 158ml hydroxyethyl methacrylate and 40ml toluene, add 1.7g benzoyl peroxide;
[0021] 2. Add stainless steel powder with an average particle size of 20 μm to the premix, then add 1.98ml oleic acid and 0.99ml polyethylene glycol-400, and stir evenly to obtain a stable slurry;
[0022] 3. Add 1.98ml of dimethylaniline, stir quickly and evenly, inject it into the ultrasonic vibration mold, and vibrate continuously at 25KHz for 30 minutes;
[0023] 4. After the shaking, take out the green body from the mold, and dry it in an electric blast drying oven at 100°C for 5 hours. The finally obtained green body has no pore defects and has a solid content of 55vol.%.
Embodiment 3
[0024] Implementation example 3: Gel ultrasonic vibration forming YG8 cemented carbide products.
[0025] 1. Mix 120ml hydroxyethyl methacrylate and 120ml toluene, add 0.17g benzoyl peroxide;
[0026] 2. Add YG8 cemented carbide powder with an average particle size of 3.4 μm to the premix, then add 0.168ml oleic acid and 0.108ml polyethylene glycol-400, and stir evenly to obtain a stable slurry;
[0027] 3. Add 0.168ml of dimethylaniline, stir quickly and evenly, inject into the ultrasonic vibration mold, and vibrate continuously at 40KHz for 15 minutes;
[0028] 4. After the shaking, take out the green body from the mold, and dry it in an electric blast drying oven at 80°C for 3 hours. The finally obtained green body has no pore defects and has a solid content of 57vol.%.
PUM
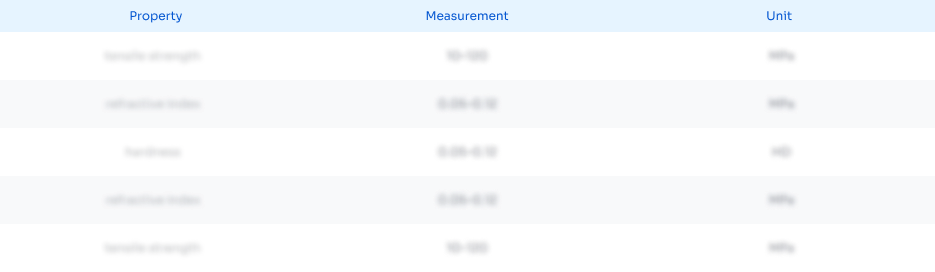
Abstract
Description
Claims
Application Information

- R&D
- Intellectual Property
- Life Sciences
- Materials
- Tech Scout
- Unparalleled Data Quality
- Higher Quality Content
- 60% Fewer Hallucinations
Browse by: Latest US Patents, China's latest patents, Technical Efficacy Thesaurus, Application Domain, Technology Topic, Popular Technical Reports.
© 2025 PatSnap. All rights reserved.Legal|Privacy policy|Modern Slavery Act Transparency Statement|Sitemap|About US| Contact US: help@patsnap.com