Method for rapidly reducing nickel slag to produce iron-nickel-copper alloy powder in kiln under reducing atmosphere
An iron-nickel-copper and kiln technology, which is applied in the field of comprehensive utilization of resources, can solve the problems that do not involve the reuse of weakly reducing tail gas, etc., and achieve the effects of shortening the reduction time, improving utilization efficiency, and improving efficiency
- Summary
- Abstract
- Description
- Claims
- Application Information
AI Technical Summary
Problems solved by technology
Method used
Image
Examples
Embodiment 1
[0036] The process flow of this embodiment consists of four parts: kiln control, batching, section making, deep reduction roasting and crushing wet grinding-wet magnetic separation.
[0037] In order to control the strong reducing atmosphere inside the kiln, the air supply during the kiln combustion is 50% of the total air required for the complete combustion of the supplied fuel. The above-mentioned air required for complete combustion refers to the conversion of 100% of various carbon-containing compounds in the fuel into CO 2 The amount of theoretical calculations required.
[0038] In order to maintain a strong reducing atmosphere in the kiln and achieve the high temperature of 1350°C required for rapid and deep reduction in the kiln, both fuel gas and air need to be preheated at high temperature. The fuel gas used is natural gas. The preheating of natural gas adopts the tube heat exchanger to exchange heat with the high-temperature waste gas discharged from the deep red...
Embodiment 2
[0042] The main chemical components of the nickel waste slag used are: TFe40.21%, SiO 2 34.61%, Al 2 o 3 2.26%, MgO8.86%, CaO3.37%, Ni0.23%, Cu0.16%, other 2.6%. The reducing agent used is lignite, the additive used is lime, and the binder used is sodium carboxymethylcellulose (CMC). Mix and grind the above nickel waste slag, lignite and lime in proportion to 20% of the remaining 200 mesh sieve, add binder and water accounting for 9% of the dry basis of all materials, and use a section machine to make the diameter and height after mixing. They are all small cylinders of 20mm, and they are laid flat on the bottom of the kiln after drying. The thickness of the material layer is 30mm. The iron-nickel-copper alloy powder with an iron recovery rate of 97.51% was obtained by magnetic separation. The iron content of the obtained product is 91.97%, the nickel content is 0.47%, the copper content is 0.28%, and the particle size is 5-70um. It can be used as a raw material for smeltin...
Embodiment 3
[0044] The proportion of nickel waste slag, reducing agent, additive and binder used in the batching of this embodiment is, nickel waste slag:reducing agent:additive:binding agent=100:14:5.4:5. The main chemical components of the nickel waste slag used are: TFe42.31%, SiO 2 35.60%, Al 2 o 3 2.37%, MgO5.77%, CaO3.26%, Ni0.22%, Cu0.16%, other 2.55%. The reducing agent used is coke powder, the additive used is lime, and the binder used is sodium carboxymethylcellulose (CMC).
[0045] Mix and grind the above-mentioned nickel waste slag, coke powder and lime in proportion to the remaining 20% of the 200 mesh sieve, add binder and water accounting for 10% of the dry basis of all materials, and use a section machine to make diameter and Small cylinders with a height of 20mm are laid flat on the bottom of the kiln after drying. The thickness of the material layer is 30mm. The reduction temperature of the material layer is 1350°C and the reduction time is 20min. The reduced materi...
PUM
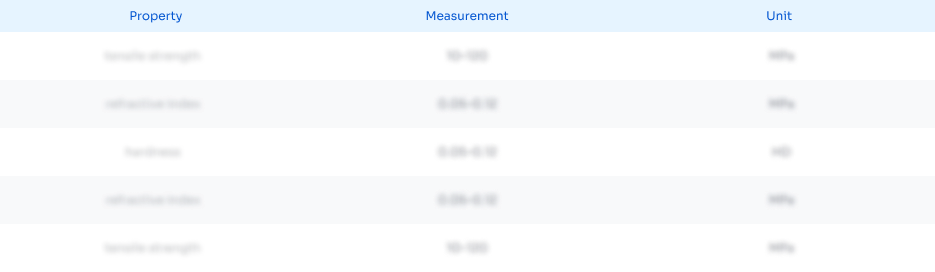
Abstract
Description
Claims
Application Information

- R&D
- Intellectual Property
- Life Sciences
- Materials
- Tech Scout
- Unparalleled Data Quality
- Higher Quality Content
- 60% Fewer Hallucinations
Browse by: Latest US Patents, China's latest patents, Technical Efficacy Thesaurus, Application Domain, Technology Topic, Popular Technical Reports.
© 2025 PatSnap. All rights reserved.Legal|Privacy policy|Modern Slavery Act Transparency Statement|Sitemap|About US| Contact US: help@patsnap.com