Manufacturing process of screw rod of ceramic-phase nanocrystalline composite coating injection molding machine
A technology of nanocrystalline composite and injection molding machine screw, which is applied in the direction of metal material coating process, coating, ion implantation plating, etc., can solve the problems of insufficient wear resistance and corrosion resistance, and achieve shortening of islanding time and friction The effect of low coefficient and good anti-corrosion effect
- Summary
- Abstract
- Description
- Claims
- Application Information
AI Technical Summary
Problems solved by technology
Method used
Examples
Embodiment 1
[0035]First polish the surface of the screw rod of conventional materials, clean it with ultrasonic degreasing and wax removal, and then dry it. After installing the fixture, put it in the cavity of the self-developed VAST-P800 coating equipment, and carry out vacuum heating. The heating temperature is set at 350 degree, when vacuumed to 5×10 -3 Pa, start to fill with argon gas, the partial pressure of argon gas is at 0.2Pa, and perform argon ion glow discharge cleaning for 30 minutes. After the argon gas cleaning is completed, use the cleaned screw as the base material, The temperature of the substrate is 350 degrees, under the bias voltage of -150V, deposit a 500nm thick Cr layer transition layer on the substrate, then turn off the argon gas, fill in nitrogen, the nitrogen partial pressure is 0.5Pa pressure, the temperature is 350 degrees, the substrate bias Open the Ti, Al, Si, and Cr targets under the condition of -250V, and deposit the TiAlCrN / Si crystal composite layer o...
Embodiment 2
[0037] First polish the surface of the screw rod of conventional materials, clean it with ultrasonic degreasing and wax removal, and then dry it. After installing the fixture, put it in the cavity of the self-developed VAST-P800 coating equipment, and carry out vacuum heating. The heating temperature is set at 300 degree, when vacuumed to 5×10 -3 Pa, start filling with argon gas, the partial pressure of argon gas is at 0.1Pa, and carry out argon ion glow discharge cleaning for 40 minutes. Partial pressure at 0.5Pa, substrate temperature 300 degrees, -200V bias, deposit a 500nm thick TiN transition layer on the substrate, then turn off argon, fill with nitrogen, nitrogen partial pressure at 0.6Pa pressure, temperature Open the Ti, Al, Zr, Cr, W targets under the condition of 300 degrees, substrate bias -200V, and deposit multi-element interlaced ceramic phase nanocrystalline structure composite layer TiAlCrZrN / W crystal as the main functional layer, the thickness of the main fu...
Embodiment 3
[0039] First polish the surface of the screw rod of conventional materials, clean it with ultrasonic degreasing and wax removal, and then dry it. After installing the fixture, put it in the cavity of the self-developed VAST-P800 coating equipment, and carry out vacuum heating. The heating temperature is set at 350 degree, when vacuumed to 5×10 -3 Pa, start filling with argon gas, the partial pressure of argon gas is at 0.15Pa, carry out argon ion glow discharge cleaning, the time is 30 minutes, after the argon gas cleaning is completed, use the cleaned screw as the base material, The temperature of the substrate is 350 degrees, under the bias voltage of -180V, deposit a 500nm thick Cr layer transition layer on the substrate, then turn off the argon gas, fill in nitrogen, the partial pressure of nitrogen is 0.55Pa pressure, the temperature is 350 degrees, the substrate bias Open the Ti, Al, Si, and Cr targets under the condition of -230V, and deposit TiAlCrN / Si crystal composit...
PUM
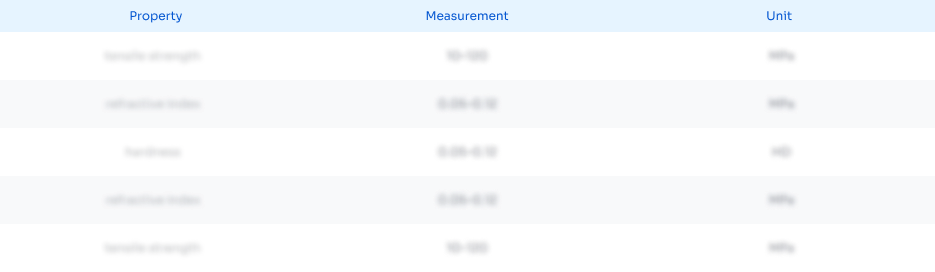
Abstract
Description
Claims
Application Information

- R&D
- Intellectual Property
- Life Sciences
- Materials
- Tech Scout
- Unparalleled Data Quality
- Higher Quality Content
- 60% Fewer Hallucinations
Browse by: Latest US Patents, China's latest patents, Technical Efficacy Thesaurus, Application Domain, Technology Topic, Popular Technical Reports.
© 2025 PatSnap. All rights reserved.Legal|Privacy policy|Modern Slavery Act Transparency Statement|Sitemap|About US| Contact US: help@patsnap.com