Special copper alloy powder for laser-sensing composite fusion-covering high-strength high-conductivity copper alloy coating
A technology of copper alloy and powder, which is applied in the field of copper alloy powder for laser-induction composite cladding high-strength and high-conductivity copper alloy coating, which can solve the problem of large difference in thermophysical properties, large temperature gradient, and uneven distribution of alloy elements and particle sizes. Uniformity and other issues to achieve the effect of improving high temperature oxidation resistance, hardness and wear resistance, strength and hardness
- Summary
- Abstract
- Description
- Claims
- Application Information
AI Technical Summary
Problems solved by technology
Method used
Examples
Embodiment Construction
[0011] The chemical composition of the special copper alloy powder of the present invention is (mass percentage): Ti 3.2%; Mg 2.5%; Zr 0.32%; B 0.5%; Al 7.5%; Ni 10%; Nb 1.6%; W 5%; Hf 0.45 %; Sc 0.35; the balance is Cu.
[0012] The preparation process of the present invention is: vacuum high-frequency induction smelting-atomization-screening-activation-water washing-drying-electroless nickel plating-filtration-water washing-drying to form special copper alloy powder with a particle size of 30-50 μm. In addition, the special copper alloy powder of the present invention undergoes electroless nickel plating to form a core-shell structure during the preparation process, thereby improving the high-temperature oxidation resistance during the laser-induction composite cladding process. In addition, the addition of alloying elements Ti, Mg, Zr, B, Al, Ni, Nb, and W can improve the strength, hardness, and wear resistance of copper alloys, and the addition of rare earth elements Hf an...
PUM
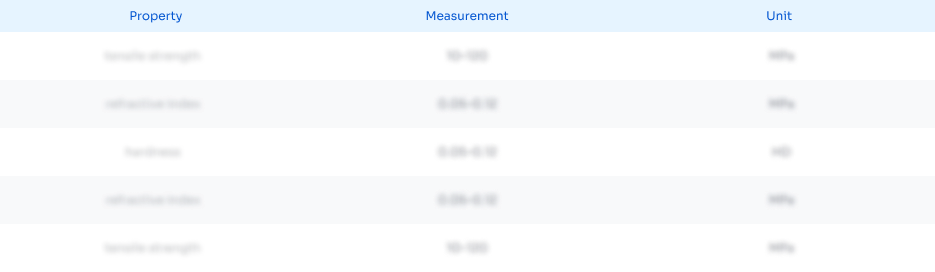
Abstract
Description
Claims
Application Information

- R&D Engineer
- R&D Manager
- IP Professional
- Industry Leading Data Capabilities
- Powerful AI technology
- Patent DNA Extraction
Browse by: Latest US Patents, China's latest patents, Technical Efficacy Thesaurus, Application Domain, Technology Topic, Popular Technical Reports.
© 2024 PatSnap. All rights reserved.Legal|Privacy policy|Modern Slavery Act Transparency Statement|Sitemap|About US| Contact US: help@patsnap.com