Organic silicon acrylic acid modified waterborne epoxy emulsion and preparation method thereof
A water-based epoxy emulsion, acrylic technology, applied in the direction of coating, can solve the problems of short pot life, unsatisfactory comprehensive mechanical properties, environmental pollution, etc., to improve impact resistance, excellent comprehensive performance, fine and uniform particle size Effect
- Summary
- Abstract
- Description
- Claims
- Application Information
AI Technical Summary
Problems solved by technology
Method used
Examples
experiment example 1
[0030] (1) Preparation of nuclear layer emulsion
[0031] 292kg of deionized water, reactive emulsifier (among them: 12kg of allyl polyether sulfate, 12kg of acrylamide isopropyl sodium sulfonate, 8kg of 2-allyl ether 3-hydroxypropane-1-sulfonate ), additives (A E100 allyl polyether) 3.5kg, initiator (sodium persulfate) 1.2kg, epoxy resin E-51 285kg, epoxy silane (3-glycidyl propyl trimethoxy silane) 11.5kg, reactive diluent (butyl glycidyl ether) 15kg, acrylic acid monomer (9.5kg of styrene, 5kg of methyl methacrylate, 14.5kg of butyl acrylate, and 0.75kg of acrylic acid) were added to the reaction under stirring conditions Kettle, heat up to 85-90°C and react for 1.5-2 hours to form a core layer organosilicon acrylic acid modified water-based epoxy emulsion.
[0032] (2) Preparation of core-shell structure organosilicon acrylic acid modified waterborne epoxy emulsion
[0033] Core layer organosilicon acrylic acid modified water-based epoxy emulsion 669.95kg, add 327.55kg s...
experiment example 2
[0035] (1) Preparation of nuclear layer emulsion
[0036] 292kg of deionized water, reactive emulsifier (among them: 12kg of allyl polyether sulfate, 12kg of acrylamide isopropyl sodium sulfonate, 8kg of 2-allyl ether 3-hydroxypropane-1-sulfonate ), additives (allyl polyether) 3.5kg, epoxy resin E-44 270kg, reactive diluent (butyl glycidyl ether) 30kg, epoxy silane (3-glycidyl propyl trimethoxysilane) 11.5kg, initiator (potassium persulfate) 1.2kg, acrylate monomer (9.5kg of styrene, 5kg of methyl methacrylate, 14.5kg of butyl acrylate, and 0.75kg of acrylic acid) were added to the reactor in turn under stirring conditions, Raise the temperature to 85-90°C and react for 1.5-2 hours to form a silicone acrylic modified water-based epoxy emulsion for the core layer.
[0037] (2) Preparation of core-shell structure organosilicon acrylic acid modified waterborne epoxy emulsion
[0038] 669.95 kg of silicone acrylic modified water-based epoxy emulsion for the core layer, 327.55 kg...
experiment example 3
[0040] (1) Preparation of nuclear layer emulsion
[0041] 311.9kg of deionized water, reactive emulsifier (among them: 13kg of allyl polyether sulfate, 13kg of acrylamide isopropyl sodium sulfonate, 9kg of 2-allyl 3-hydroxypropane-1-sulfonate , additive (allyl polyether) 3kg, epoxy silane (3-glycidyl propyltrimethoxysilane) 10kg, initiator (sodium persulfate) 1kg, epoxy resin E-51 392kg, isooctyl 58kg of glycidyl ether, acrylic acid monomer (including 6kg of styrene, 5kg of methyl methacrylate, 10kg of butyl acrylate, and 0.6kg of acrylic acid) were added to the reactor in turn under stirring conditions, and the temperature was raised to 85-90°C for 1.5-2 hours , forming a core layer silicone acrylic modified water-based epoxy emulsion.
[0042] (2) Preparation of core-shell structure organosilicon acrylic acid modified waterborne epoxy emulsion
[0043] Core layer organosilicon acrylic acid modified water-based epoxy emulsion 832.5kg, add shell layer pre-emulsion monomer 16...
PUM
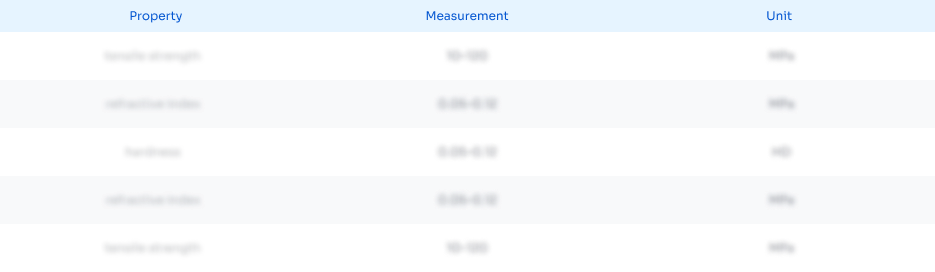
Abstract
Description
Claims
Application Information

- R&D
- Intellectual Property
- Life Sciences
- Materials
- Tech Scout
- Unparalleled Data Quality
- Higher Quality Content
- 60% Fewer Hallucinations
Browse by: Latest US Patents, China's latest patents, Technical Efficacy Thesaurus, Application Domain, Technology Topic, Popular Technical Reports.
© 2025 PatSnap. All rights reserved.Legal|Privacy policy|Modern Slavery Act Transparency Statement|Sitemap|About US| Contact US: help@patsnap.com