Method for recovering precious metal from electronic waste
A technology of electronic waste and precious metals, applied in the field of recycling precious metals, can solve the problems of low production efficiency, high product cost, easy to pollute the environment, etc., and achieve the effects of improving working conditions, high-efficiency enrichment, and simple process
- Summary
- Abstract
- Description
- Claims
- Application Information
AI Technical Summary
Problems solved by technology
Method used
Examples
Embodiment 1
[0023] The method includes the following steps:
[0024] (1) Pretreatment of electronic waste first: (a) take 1000g electronic waste, mechanically crush and sieve to obtain electronic waste powder; (b) take electronic waste powder, separate and remove rubber and plastic materials by electrostatic separation, and collect precious metal rich Collectively; (c) Take precious metal-enriched bodies, remove ferromagnetic metals by magnetic separation, and collect non-ferromagnetic metal-enriched bodies;
[0025] Then dry the pretreated electronic waste with 200g of iron powder, 50g of lime and 50g of carbon powder, grind them, and mix them evenly;
[0026] (2) Put the mixed material into a graphite crucible and place it in a box-type resistance furnace or an electric arc furnace, heat up and reduce at a temperature of 1100°C for 1 hour, protect with nitrogen gas, and cool with water after reduction to allow the precious metal to enter the alloy;
[0027] (3) Selectively leaching the...
Embodiment 2
[0030] The method includes the following steps:
[0031] (1) Pretreatment of electronic waste first: (a) take 1000g electronic waste, mechanically crush and sieve to obtain electronic waste powder; (b) take electronic waste powder, separate and remove rubber and plastic materials by electrostatic separation, and collect precious metal rich Collectively; (c) Take precious metal-enriched bodies, remove ferromagnetic metals by magnetic separation, and collect non-ferromagnetic metal-enriched bodies;
[0032] Then dry the pretreated electronic scrap with 250g of iron oxide, 80g of sodium sulfate and 80g of carbon powder, pulverize and mix evenly;
[0033] (2) Put the mixed material into a graphite crucible and place it in a box-type resistance furnace or an electric arc furnace, heat up and reduce at a temperature of 1200°C for 3 hours, pass nitrogen protection, and cool with water after reduction to allow the precious metal to enter the alloy;
[0034] (3) Selectively leaching t...
Embodiment 3
[0037] The method includes the following steps:
[0038] (1) Pretreatment of electronic waste first: (a) take 1000g electronic waste, mechanically crush and sieve to obtain electronic waste powder; (b) take electronic waste powder, separate and remove rubber and plastic materials by electrostatic separation, and collect precious metal rich Collectively; (c) Take precious metal-enriched bodies, remove ferromagnetic metals by magnetic separation, and collect non-ferromagnetic metal-enriched bodies;
[0039] Then dry the pretreated electronic waste with 300g of iron oxide, 100g of lime and 100g of carbon powder, pulverize them, and mix them evenly;
[0040] (2) Put the mixed material into a graphite crucible and place it in a box-type resistance furnace or an electric arc furnace, heat up and reduce at a temperature of 1350°C for 4 hours, protect with nitrogen gas, and cool with water after reduction to allow the precious metal to enter the alloy;
[0041] (3) Selectively leachi...
PUM
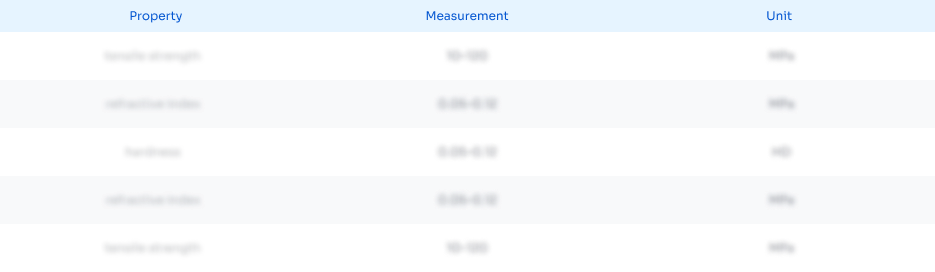
Abstract
Description
Claims
Application Information

- R&D
- Intellectual Property
- Life Sciences
- Materials
- Tech Scout
- Unparalleled Data Quality
- Higher Quality Content
- 60% Fewer Hallucinations
Browse by: Latest US Patents, China's latest patents, Technical Efficacy Thesaurus, Application Domain, Technology Topic, Popular Technical Reports.
© 2025 PatSnap. All rights reserved.Legal|Privacy policy|Modern Slavery Act Transparency Statement|Sitemap|About US| Contact US: help@patsnap.com