Manufacturing method of low-temperature polysilicon thin film
A thin film manufacturing method and low-temperature polysilicon technology are applied in the growth of polycrystalline materials, chemical instruments and methods, crystal growth, etc., which can solve the problems of polysilicon thin film inhomogeneity, reduce defect state density, high uniformity, and improve quality. Effect
- Summary
- Abstract
- Description
- Claims
- Application Information
AI Technical Summary
Problems solved by technology
Method used
Image
Examples
Embodiment 1
[0032] A specific embodiment of a low-temperature polysilicon thin film manufacturing method described in the present invention is given below, a low-temperature polysilicon thin film manufacturing method, on the basis of maintaining the solid phase crystallization ambient temperature at 550-700 degrees Celsius, one or more Light source with photon energy in the range of 2.5-5.0eV. The low-temperature polysilicon film manufacturing method comprises the following three steps:
[0033] In the first step, the local polysilicon forms crystal nuclei with a diameter larger than the critical dimension under the action of thermal fluctuations;
[0034] In the second step, the crystal nuclei grow to form crystal grains;
[0035] In the third step, the adjacent grain boundaries are closed to complete the transition from amorphous silicon to polysilicon, and the internal defect states of the polysilicon are gradually repaired to form a polysilicon film.
[0036] In this embodiment, in ...
Embodiment 2
[0039] The light source is only added in the first step, the photon energy is 2.0eV, the irradiation time is 8 minutes, and the number of light sources is two ultraviolet light sources. As other convertible implementations, the energy of the photons added in the first step can also be selected to be 3.0eV, the heating time is 10 minutes, and the number of light sources is three; or a 4.0eV light source is added, and the heating time is 15 minutes. The number is 1. The function of adding a light source in the first step is to assist the formation of crystal nuclei and increase the temperature of the amorphous silicon film. The photon energy is selected from 2.0-4.0eV, and amorphous silicon has good absorption in this band. The heating time is about 5-15 minutes.
Embodiment 3
[0041] The light source is only added in the second step, the photon energy is 4.0eV, the irradiation time is 120 minutes, and the number of light sources is three ultraviolet light sources. As other convertible implementations, the energy of the photons added in the second step can also be selected as 4.5eV, the heating time is 20 minutes, and the number of light sources is two; or a 4.2eV light source is added, and the heating time is 60 minutes. The number is one. The role of adding light source in the second step is to increase the grain growth rate and inhibit the formation of new crystal nuclei in the amorphous silicon region. The photon energy range is 4.0-4.5eV. In this band, only the crystal grains will have strong absorption. , the absorption of amorphous silicon is not strong. Therefore, the growing crystal grains will be heated to increase their growth rate; on the other hand, amorphous silicon will not be heated, so that too many crystal nuclei will not be formed...
PUM
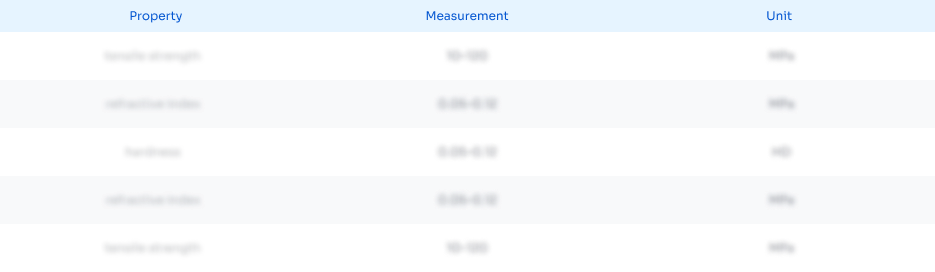
Abstract
Description
Claims
Application Information

- R&D
- Intellectual Property
- Life Sciences
- Materials
- Tech Scout
- Unparalleled Data Quality
- Higher Quality Content
- 60% Fewer Hallucinations
Browse by: Latest US Patents, China's latest patents, Technical Efficacy Thesaurus, Application Domain, Technology Topic, Popular Technical Reports.
© 2025 PatSnap. All rights reserved.Legal|Privacy policy|Modern Slavery Act Transparency Statement|Sitemap|About US| Contact US: help@patsnap.com