Method for producing high-quality copper sulfate through low-pressure oxygen leaching of copper slag
A low-pressure oxygen and copper sulfate technology, applied in the direction of copper sulfate, process efficiency improvement, etc., can solve the problems of complicated process and high production cost, and achieve the effect of high product purity
- Summary
- Abstract
- Description
- Claims
- Application Information
AI Technical Summary
Problems solved by technology
Method used
Image
Examples
Embodiment 1
[0031] (1) Copper slag produced by 1 ton of zinc hydrometallurgy is used as the raw material. Copper mainly exists in the form of cuprous oxide. The mass percentage of its main chemical components is Cu 25.0wt%, Pb 20.0wt%, Zn 4.8wt%, and Acid-containing 135g / l dilute sulfuric acid solution is 4m according to the liquid-solid ratio 3 / t mixed into 5m 3 Into a pressure vessel, at 80°C, oxygen with a volumetric oxygen content of 99.5% is blown into the pressure vessel to keep the partial pressure of oxygen in the pressure vessel at 0.2Mpa, the total pressure at 0.25MPa, the leaching time is 2 hours, and the final pH value is 2.0, and the leaching The feed liquid is filtered with a filter press at 80°C to obtain leaching liquid and leaching slag respectively, and the leaching slag is sent to other smelting processes to recover other valuable metals. The leaching rate is 95.6%.
[0032] (2) Add the leaching solution obtained in step (1) to 4m 3 Into the crystallization kettle, ...
Embodiment 2
[0035] (1) 100g of sponge copper slag is used as the material, copper mainly exists in the form of metallic copper, and the mass percentage of its main chemical components is Cu 75.4wt%, Zn 10.2wt%, Pb 1.5wt% and acid 160g / l dilute sulfuric acid The solution is 10m according to the liquid-solid ratio 3 / t mixed into a 2L pressure vessel, at 75°C, blow in oxygen-enriched air with a volume oxygen content of 30%, keep the oxygen partial pressure in the pressure vessel at 0.08Mpa, and the total pressure at 0.3MPa, leaching for 4 hours , the end point pH value is 1.5, and the leaching material liquid is obtained, which is vacuum filtered at 85°C to obtain the leaching liquid and leaching slag respectively, and the leaching slag is returned to other smelting processes to recover other valuable metals. The leaching rate is 95.8%.
[0036] (2) Put the leaching solution obtained in step (1) in an 800ml beaker, let it stand for cooling and crystallization, the final temperature of cool...
PUM
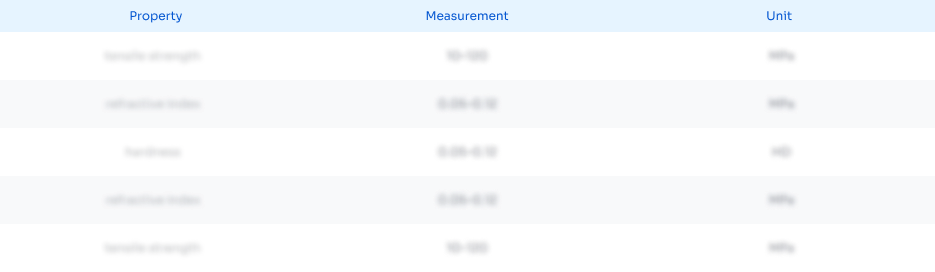
Abstract
Description
Claims
Application Information

- R&D
- Intellectual Property
- Life Sciences
- Materials
- Tech Scout
- Unparalleled Data Quality
- Higher Quality Content
- 60% Fewer Hallucinations
Browse by: Latest US Patents, China's latest patents, Technical Efficacy Thesaurus, Application Domain, Technology Topic, Popular Technical Reports.
© 2025 PatSnap. All rights reserved.Legal|Privacy policy|Modern Slavery Act Transparency Statement|Sitemap|About US| Contact US: help@patsnap.com