Method for preparing silica through coal gangue aluminum extraction waste slag
A technology for coal gangue and white carbon black, which is applied in the field of preparing white carbon black, can solve the problems of difficult industrial production, different aluminum content of aluminum extraction waste residues, and difficult control of reaction conditions, and achieves high product purity and easy control of reaction conditions. Effect
- Summary
- Abstract
- Description
- Claims
- Application Information
AI Technical Summary
Problems solved by technology
Method used
Image
Examples
Embodiment 1
[0021] Take by weighing 100g waste residue 1, 90g quartz sand mix, make SiO 2 The total content is 91.6%, Al 2 o 3 The content is 5%, then according to SiO 2 :Na 2 O molar ratio = 1:0.43 Add 132g of sodium carbonate, mix and grind into a powder mixture of about 100μm with a ball mill. Weigh 100 g of the mixed sample and put it into a rotary furnace, set the temperature at 820° C. for 3 hours, and obtain coarse sodium silicate solid particles after the reaction is completed. Put the above crude sodium silicate particles in a 1L autoclave, add 250mL of distilled water according to the solid-to-liquid ratio of 1:3, heat up to 200°C, stir and dissolve for 3 hours, then cool down to room temperature, filter and separate to obtain colorless and transparent silicic acid Sodium solution and filter residue, calculate the sodium silicate dissolution rate. Dilute the sodium silicate solution to 10Bé and place it in a 2L four-necked flask. When the water bath is heated to 80°C, CO 2...
Embodiment 2
[0025] Take by weighing 100g waste residue 2, 45g quartz sand mix, make SiO 2 The total content is 90.4%, Al 2 o 3 The content is 5%, then according to SiO 2 :Na 2 O molar ratio = 1:0.43 Add 99.1g of sodium carbonate, mix and grind into a powder mixture of about 100μm with a ball mill. Weigh 100 g of the mixed sample and put it into a rotary furnace, set the temperature at 820° C. for 3 hours, and obtain coarse sodium silicate solid particles after the reaction is completed. Put the above crude sodium silicate particles in a 1L autoclave, add 250mL of distilled water according to the solid-to-liquid ratio of 1:3, heat up to 200°C, stir and dissolve for 3 hours, then cool down to room temperature, filter and separate to obtain colorless and transparent silicic acid Sodium solution and filter residue, calculate the sodium silicate dissolution rate. Dilute the sodium silicate solution to 10Bé and place it in a 2L four-necked flask. When the water bath is heated to 80°C, CO ...
Embodiment 3
[0029] Weigh 100g waste residue 3, according to SiO 2 :Na 2O molar ratio = 1:0.43 Add 70g of sodium carbonate, mix and grind into a powder mixture of about 100μm with a ball mill. Weigh 100 g of the mixed sample and put it into a rotary furnace, set the temperature at 820° C. for 3 hours, and obtain coarse sodium silicate solid particles after the reaction is completed. Put the above crude sodium silicate particles in a 1L autoclave, add 250mL of distilled water according to the solid-to-liquid ratio of 1:3, heat up to 200°C, stir and dissolve for 3 hours, then cool down to room temperature, and filter to obtain colorless and transparent silicic acid Sodium solution and filter residue, calculate the sodium silicate dissolution rate. Dilute the sodium silicate solution to 10Bé and place it in a 2L four-necked flask. When the water bath is heated to 80°C, CO 2 . Keep the constant temperature when the temperature reaches 90°C, stop the reaction when the pH of the solution dro...
PUM
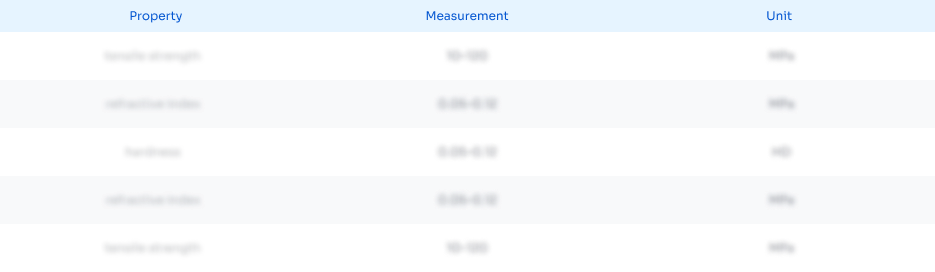
Abstract
Description
Claims
Application Information

- R&D
- Intellectual Property
- Life Sciences
- Materials
- Tech Scout
- Unparalleled Data Quality
- Higher Quality Content
- 60% Fewer Hallucinations
Browse by: Latest US Patents, China's latest patents, Technical Efficacy Thesaurus, Application Domain, Technology Topic, Popular Technical Reports.
© 2025 PatSnap. All rights reserved.Legal|Privacy policy|Modern Slavery Act Transparency Statement|Sitemap|About US| Contact US: help@patsnap.com