Method for extracting alumina and gallium oxide from pulverized fuel ash to prepare aluminum oxide nanometer and polymeric ferric silicate sulfate
A technology of polysilicate ferric sulfate and nano-alumina, which is applied in the fields of alumina/aluminum hydroxide, chemical instruments and methods, and inorganic chemistry, and can solve problems such as low income, poor economic benefits, and low utilization of equipment
- Summary
- Abstract
- Description
- Claims
- Application Information
AI Technical Summary
Problems solved by technology
Method used
Image
Examples
Embodiment 1
[0025] Embodiment 1 extracts alumina or manufactures nano-alumina with extracted alumina
[0026] According to 85% Al 2 o 3 Dissolution rate calculates the dosage of sulfuric acid, fly ash (Al 2 o 3 Content 45.3 wt%, SiO 2 content of 37.66wt%) and sulfuric acid with a concentration of 40wt% to make fly ash slurry, the ratio of fly ash to sulfuric acid is 1:0.4~0.5, (first adjust the ratio of fly ash and water to 1:1 Slurry, then add sulfuric acid) into the autoclave, react at 230-240°C, 2.8-4.8Mpa for 40-60 minutes, and turn on the mixer to make it fully react, put the reaction-dissolved slurry into the sedimentation tank and dilute and settle , the red mud acid slag flowing from the bottom of the settling tank enters the washing tank, and is reversely washed with hot water at 80-90°C for 4-6 times. , the last washing liquid is returned to the fly ash and sulfuric acid batching. After the last washing, the red mud acid residue is filtered through the filter, the filtrate...
Embodiment 2
[0032] Embodiment 2 extracts gallium oxide
[0033]After adding sodium carbonate to the aluminum sulfate solution for neutralization and decomposition, the gallium in the decomposed mother liquor is concentrated for three cycles and the ion exchange is performed when the concentration of Ga reaches 40 mg / L. LSC600 resin is used for adsorption, the resin is pretreated first, and then the decomposed mother liquor is passed through the resin column at 5ml per minute. When the test outlet concentration reaches 90% of the import value, it is in a saturated state. Stop feeding and elute, and use 4% vulcanization The sodium solution was used for elution and analysis, and the precipitated gallium sulfide was precipitated. The precipitated gallium sulfide was washed three times and filtered, dissolved in 10% NaOH solution and then filtered to obtain a clear solution. Ammonium bicarbonate is dissolved and cooled. At this time, gallium carbonate is precipitated, filtered and washed three...
Embodiment 3
[0034] Embodiment 3 prepares ferric sulfate polysilicate
[0035] The ferrosilicon slag after ferrosilicon removal is sent to the polymerization reaction tank and injected with ferric sulfate solution for polymerization reaction. The temperature is controlled at 40-55°C, and the ferric sulfate solution is added under stirring. The pH value is controlled at 3.5-4, and the polymerization reaction time is 24 Hours, stop stirring when the reaction is over, use a high-pressure pump to send it into a spray dryer, and get polysilicate ferric sulfate flocculant through the spray dryer.
PUM
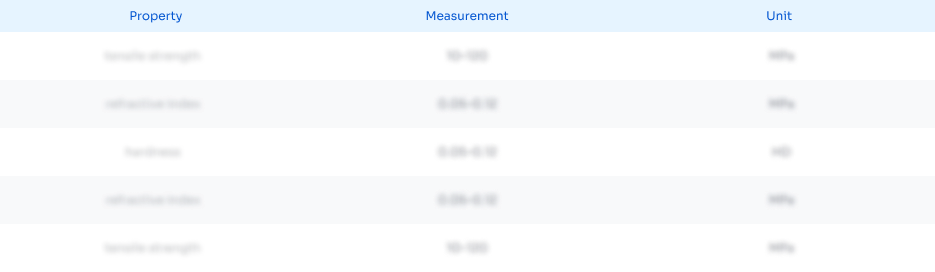
Abstract
Description
Claims
Application Information

- R&D
- Intellectual Property
- Life Sciences
- Materials
- Tech Scout
- Unparalleled Data Quality
- Higher Quality Content
- 60% Fewer Hallucinations
Browse by: Latest US Patents, China's latest patents, Technical Efficacy Thesaurus, Application Domain, Technology Topic, Popular Technical Reports.
© 2025 PatSnap. All rights reserved.Legal|Privacy policy|Modern Slavery Act Transparency Statement|Sitemap|About US| Contact US: help@patsnap.com