Inclusion control method for rod and wire alloy steel
A control method and alloy steel technology, applied in the field of metallurgy, can solve problems such as excessive inclusions in alloy steel rods and wires, and achieve the effect of improving fatigue performance
- Summary
- Abstract
- Description
- Claims
- Application Information
AI Technical Summary
Problems solved by technology
Method used
Image
Examples
Embodiment 1
[0024] Embodiment 1: the present embodiment is illustrated by producing rod and wire rod cold heading steel 35CrMo;
[0025] (1) The molten steel smelted in the converter is deoxidized by aluminum, so that the volume percentage of oxygen in the molten steel is less than 10×10 -4 %, carry out LF refining, and control the composition of the slag in the refining process to be CaO: 57wt%, Al 2 o 3 : 22.1wt%, SiO 2 : 15wt%, MgO: 5wt%, FeO: 0.9wt%, LF refining time 30min;
[0026] (2) At the end of LF refining, feed the iron-calcium wire with a diameter of 12.4mm into the molten steel, in which the iron content is 64wt%, the calcium content is 30wt%, and the balance is impurities; the wire feeding speed is 200m / min to control the calcium in the molten steel The mass percentage of aluminum is 0.16:1;
[0027] (3) After the wire feeding is completed, blow the molten steel with argon gas softly, the soft blowing time is 2min, and the soft blowing volume is controlled at 50NL / min; ...
Embodiment 2
[0033] The present embodiment is illustrated by producing rod and wire rod bearing steel GCr15;
[0034] (1) The molten steel smelted in the converter is deoxidized by aluminum, so that the volume percentage of oxygen in the molten steel is less than 10×10 -4 %, carry out LF refining, and control the composition of the slag in the refining process to be CaO: 45wt%, Al 2 o 3 : 30wt%, SiO 2: 15wt%, MgO: 9.5wt%, FeO: 0.5wt%, LF refining time 55min;
[0035] (2) At the end of LF refining, feed the silicon-calcium wire with a diameter of 13.6mm to the molten steel, in which the silicon content is 65wt%, the calcium content is 28wt%, and the balance is impurities; the feeding speed is 250m / min, and the control of the molten steel The mass percentage of calcium aluminum is 0.1:1;
[0036] (3) After the wire feeding is completed, blow argon softly to the molten steel, the soft blowing time is 10min, and the soft blowing volume is controlled at 20NL / min;
[0037] (4) Carry out RH ...
Embodiment 3
[0042] Present embodiment is described with the production wire spring steel 55SiCrA;
[0043] (1) The molten steel smelted in the converter is deoxidized by aluminum, so that the volume percentage of oxygen in the molten steel is less than 10×10 -4 %, carry out LF refining, and control the composition of the slag in the refining process to be CaO: 57wt%, Al 2 o 3 : 30wt%, SiO 2 : 3wt%, MgO: 9.9wt%, FeO: 0.1wt%, LF refining time 40min;
[0044] (2) At the end of LF refining, feed a solid calcium wire with a diameter of 10mm to the molten steel, in which the calcium content is 97%, and the remainder is impurities; the wire feeding speed is 50m / min, and the mass percentage of calcium and aluminum in the molten steel is controlled to be 0.08: 1;
[0045] (3) After the wire feeding is completed, blow argon softly to the molten steel, the soft blowing time is 6 minutes, and the soft blowing volume is controlled at 30NL / min;
[0046] (4) Carry out RH vacuum treatment on the mol...
PUM
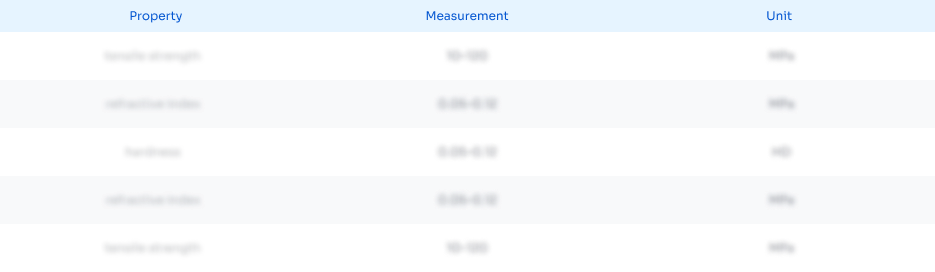
Abstract
Description
Claims
Application Information

- Generate Ideas
- Intellectual Property
- Life Sciences
- Materials
- Tech Scout
- Unparalleled Data Quality
- Higher Quality Content
- 60% Fewer Hallucinations
Browse by: Latest US Patents, China's latest patents, Technical Efficacy Thesaurus, Application Domain, Technology Topic, Popular Technical Reports.
© 2025 PatSnap. All rights reserved.Legal|Privacy policy|Modern Slavery Act Transparency Statement|Sitemap|About US| Contact US: help@patsnap.com