Method for processing limonite lateritic nickel
A technology of lateritic nickel ore and limonite, which is applied in the field of processing limonite-type lateritic nickel ore to recover iron, nickel and cobalt, and can solve the problems of high impurity content in leachate, no mention of iron recycling, poor control of process operation, etc. Achieve high iron comprehensive utilization rate, reduce the loss of nickel and cobalt, and reduce the consumption of reagents
- Summary
- Abstract
- Description
- Claims
- Application Information
AI Technical Summary
Problems solved by technology
Method used
Image
Examples
Embodiment 1
[0048] See attached figure 1 . After the original ore is crushed and dry-milled, 80% of the laterite ore with a particle size of less than 74 μm is obtained, and 20% of water is added, and concentrated sulfuric acid with a mass fraction of 98% is added according to the acid amount of 200 kg / t ore, so that the acid and ore After fully mixing, it was aged and roasted at 450°C for 1 h; the cured material was directly soaked in water under normal pressure at a temperature of 60°C for 5 h, a liquid-solid ratio of 3:1 (ml / g), and a stirring speed of 200 rpm. The leaching rate of nickel is 75.3%, the leaching rate of cobalt is 85.1%, and the leaching rate of iron is as low as 0.2%. After dense separation and 5-stage dense washing with a liquid-solid ratio of 4:1 (ml / g), the leaching residue, leaching liquid and washing liquid are obtained ; The leaching slag was mixed with 8% lignite, magnetized and roasted at 800 ℃ for 1 hour, and then water quenched. The water quenched slag was ba...
Embodiment 2
[0050] The raw ore is crushed and wet-milled to obtain a laterite ore with a particle size of less than 74 μm, accounting for 70%, and a water content of 28%. Add concentrated sulfuric acid with a mass fraction of 98% according to the acid content of 300 kg / t ore, so that the acid and ore are fully mixed. , aged and roasted at 600°C for 0.5 h; the cured material was directly soaked in atmospheric pressure water at a temperature of 75°C for 0.5 h, a liquid-solid ratio of 6:1 (ml / g), and a stirring speed of 300 rpm. The nickel leaching rate The leaching rate of cobalt is 75.6%, the leaching rate of cobalt is 85.4%, and the leaching rate of iron is as low as 0.4%. After dense separation and 6-stage dense washing with a liquid-solid ratio of 3:1 (ml / g), the leaching residue, leaching liquid and washing liquid are obtained; the leaching residue Add 5% lignite, magnetize and roast at 750°C for 1.5 h, then water quench, water quench slag ball mill for 30 min, and then perform magnetic...
Embodiment 3
[0052] The raw ore is crushed and wet-milled to obtain laterite ore with a particle size of less than 74 μm, which accounts for 85% and contains 30% water. Add concentrated sulfuric acid with a mass fraction of 98% according to the acid amount of 180 kg / t ore, so that the acid and ore are fully mixed. , aged and roasted at 300°C for 3 h; the cooked material was directly soaked in atmospheric pressure water at a temperature of 90°C for 2 h, a liquid-solid ratio of 1:1 (ml / g), and a stirring speed of 500 rpm. The nickel leaching rate The leaching rate of cobalt is 75.1%, the leaching rate of cobalt is 84.9%, and the leaching rate of iron is as low as 0.1%. After dense separation and 8-stage dense washing with a liquid-solid ratio of 2:1 (ml / g), the leaching residue, leaching liquid and washing liquid are obtained; the leaching residue Add 10% bituminous coal, magnetize and roast at 700°C for 0.5 h, then water quench, water quench slag ball milled for 10 min, then perform magnetic...
PUM
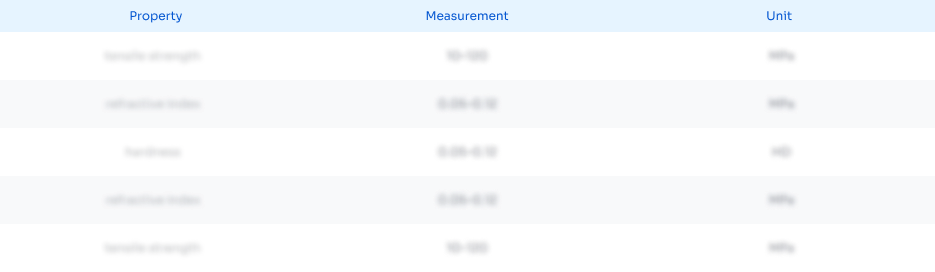
Abstract
Description
Claims
Application Information

- R&D
- Intellectual Property
- Life Sciences
- Materials
- Tech Scout
- Unparalleled Data Quality
- Higher Quality Content
- 60% Fewer Hallucinations
Browse by: Latest US Patents, China's latest patents, Technical Efficacy Thesaurus, Application Domain, Technology Topic, Popular Technical Reports.
© 2025 PatSnap. All rights reserved.Legal|Privacy policy|Modern Slavery Act Transparency Statement|Sitemap|About US| Contact US: help@patsnap.com