Integrated approach to enriching nickel from nickel oxide laterite ore
A technology of nickel oxide ore and comprehensive method, which is applied in the field of nickel metallurgy, can solve problems such as difficult control of temperature control technology, difficulty in effective use of magnesium sulfate, and difficulty in meeting environmental protection requirements, so as to avoid the material pelletizing process and reduce energy consumption And the consumption of various materials, the effect of improving production efficiency and product quality
- Summary
- Abstract
- Description
- Claims
- Application Information
AI Technical Summary
Problems solved by technology
Method used
Image
Examples
Embodiment 1
[0022] Embodiment 1: the chemical composition of magnesia laterite nickel oxide and ferrous laterite nickel oxide mixed ore raw material: Ni1.02~1.23%, Mg 12.01~16.02%, Fe 7.05~15.89%, Co 0.043~0.067%, Al3.21 ~ 4.88%, Si 2.01 ~ 15.96%.
[0023] A. Use a vertical mill to crush (after pretreatment) the raw ore (containing 15-20% structural water) containing surface water <5% to less than 0.5mm, and then add it to a multi-stage cyclone for drying, calcination and reduction, and spray it into The reduced coal powder accounting for 5% of the weight ratio of the raw ore is reduced and roasted, the temperature of the drying and calcining section is 700±50°C, the temperature of the reducing section is controlled at 950±50°C, and the reduction time is 0.5-1h.
[0024] B. The reduced material is quenched by water, and sent to a wet ball mill for grinding. The grinding concentration is controlled at 50-60%, and the grinding particle size reaches 200-320 mesh. A magnetic separator is use...
Embodiment 2
[0025] Embodiment 2: the chemical composition of magnesia laterite nickel oxide ore raw material: Ni 0.81~1.1%, Mg19.25~24.10%, Fe8.01~11.01%, Co0.021~0.03%, Al0.04~0.07%, Si15 .04~20.78%
[0026] A. Use a vertical mill to crush (after pretreatment) the raw ore (containing 15-20% structural water) containing surface water < 5% to less than 0.5mm, and then add it to a five-stage cyclone for drying, calcination and reduction, and spray it into The reduced coal powder accounting for 5% of the weight ratio of the raw ore is reduced and roasted, the temperature of the drying and calcining section is 750±50°C, the temperature of the reducing section is controlled at 900±50°C, and the reduction time is 0.5-1h.
[0027] B. The reduced material is quenched by water, and sent to a wet ball mill for grinding. The grinding concentration is controlled at 50-60%, and the grinding particle size reaches 200-320 mesh. A magnetic separator is used for sorting, and the magnetic field strength i...
Embodiment 3
[0030] Embodiment 3: the chemical composition of ferrous laterite nickel oxide ore raw material: Ni1.11~1.25%, Mg8.04~10.12%, Fe18.51~25.99%, Co0.061~0.081%, Al3.21~4.88%, Si2.01~15.96%.
[0031] A. Use a vertical mill to crush (after pretreatment) the raw ore (containing 15-20% structural water) containing surface water <5% to less than 0.5mm, and then add it to a multi-stage cyclone for drying, calcination and reduction, and spray into it at the same time The reduced coal powder accounting for 5% of the weight ratio of the raw ore is reduced and roasted, the temperature of the drying and calcining section is 700±50°C, the temperature of the reducing section is controlled at 950±50°C, and the reduction time is 0.5-1h.
[0032]B. The reduced material is quenched by water, and sent to a wet ball mill for grinding. The grinding concentration is controlled at 50-60%, and the grinding particle size reaches 200-320 mesh. A magnetic separator is used for sorting, and the magnetic f...
PUM
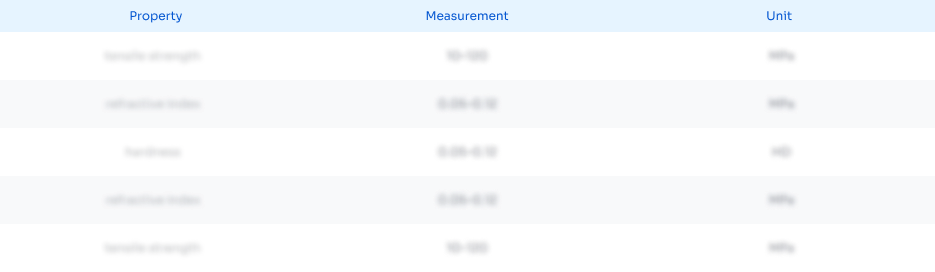
Abstract
Description
Claims
Application Information

- R&D
- Intellectual Property
- Life Sciences
- Materials
- Tech Scout
- Unparalleled Data Quality
- Higher Quality Content
- 60% Fewer Hallucinations
Browse by: Latest US Patents, China's latest patents, Technical Efficacy Thesaurus, Application Domain, Technology Topic, Popular Technical Reports.
© 2025 PatSnap. All rights reserved.Legal|Privacy policy|Modern Slavery Act Transparency Statement|Sitemap|About US| Contact US: help@patsnap.com