Heat conductive insulation material and preparation method thereof
A technology of thermally conductive insulating material and thermally conductive insulating filler, which is applied in the field of engineering plastics, can solve the problems of high price, does not consider whether the material is conductive, and the material is not insulating, etc., and achieves a low gas content, easy to form a conductive network, and increased thermal conductivity. Effect
- Summary
- Abstract
- Description
- Claims
- Application Information
AI Technical Summary
Problems solved by technology
Method used
Examples
Embodiment 1
[0035] Thermally conductive and insulating plastics for injection molding, the percentages of each component are liquid crystal polymer (LCP) 30%, 30μm alumina 41%, 5μm aluminum nitride 15%, glass fiber 10%, silane coupling agent 2%, hard Zinc fatty acid 2%.
[0036] Add the silane coupling agent, zinc stearate and LCP into the high-speed mixer, mix evenly, add some thermally conductive fillers alumina and aluminum nitride, continue to stir evenly, and then feed the evenly mixed material into the extruder through the main feeding port In the extruder, part of the heat-conducting filler alumina and aluminum nitride is fed into the extruder through the side feeding port, extruded and granulated to obtain a primary granulated material, and finally the obtained primary granulated material is added to the extruder from the main feeding port. In the extruder, the glass fiber is fed into the extruder from the side feeding port, extruded and granulated at 350°C to obtain thermally con...
Embodiment 2
[0039] Thermally conductive and insulating plastics for injection molding, the percentages of each component are polyphenylene sulfide (PPS) 50%, 40μm boron nitride 30%, 3μm calcium fluoride 5%, potassium titanate fiber 13%, silane coupling agent 1%, calcium stearate 1%.
[0040] Add the silane coupling agent, calcium stearate and PPS into the high-speed mixer, mix evenly, add some thermally conductive fillers boron nitride and calcium fluoride, continue to stir evenly, and then add the evenly mixed material through the main feeding port In the extruder, part of the heat-conducting filler boron nitride and calcium fluoride are fed into the extruder through the side feeding port, extruded and granulated to obtain primary pellets, and finally the obtained primary pellets are added from the main feed port Into the extruder, the potassium titanate fiber is fed into the extruder from the side feeding port, extruded and granulated at 290°C to obtain thermally conductive and insulati...
Embodiment 3
[0043] Thermally conductive and insulating plastics for injection molding, the percentages of each component are PA66 30%, 50μm silicon carbide 40%, 2μm zinc oxide 10%, glass fiber 17%, silane coupling agent 1.5%, stearic acid amide 1.5%.
[0044] Add the silane coupling agent, stearic acid amide and PPS into the high-speed mixer, mix evenly, add part of the thermal conductive filler silicon carbide and zinc oxide, continue to stir evenly, and then feed the mixed material through the main feeding port to extrude In the extruder, part of the thermally conductive filler silicon carbide and zinc oxide is fed into the extruder through the side feeding port, extruded and granulated to obtain primary pellets, and finally the obtained primary pellets are fed into the extruder from the main feed port In the process, the glass fiber is fed into the extruder from the side feeding port, extruded and granulated at 260°C to obtain thermally conductive and insulating plastics for injection m...
PUM
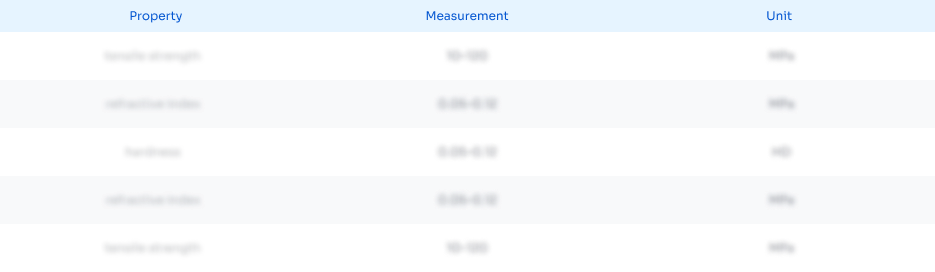
Abstract
Description
Claims
Application Information

- Generate Ideas
- Intellectual Property
- Life Sciences
- Materials
- Tech Scout
- Unparalleled Data Quality
- Higher Quality Content
- 60% Fewer Hallucinations
Browse by: Latest US Patents, China's latest patents, Technical Efficacy Thesaurus, Application Domain, Technology Topic, Popular Technical Reports.
© 2025 PatSnap. All rights reserved.Legal|Privacy policy|Modern Slavery Act Transparency Statement|Sitemap|About US| Contact US: help@patsnap.com