Preparation method of cationic dyeable halogen-free flame retardant polyester fiber
A flame-retardant polyester and cationic technology, applied in the direction of single-component copolyester artificial filaments, etc., can solve the problems of cationic dyeability decline, cost increase, and more by-products, and achieve significant flame retardancy and cationic dyeability. Dyeing effect, production cost reduction, product performance improvement effect
- Summary
- Abstract
- Description
- Claims
- Application Information
AI Technical Summary
Problems solved by technology
Method used
Examples
Embodiment 1
[0019] Step 1. Synthesis of Cationic Dyeable and Flame Retardant Compounding Agent
[0020] Sodium isophthalic acid sulfonate, 2-carboxyethyl hypophosphorous acid (CEPPA) and deionized water in a molar ratio of 1:1.5:10 were added into a glass reaction vessel, heated in a water bath to 50°C, and reacted for 1 hour. After the reaction is finished, the reaction product is filtered out, and dried at a temperature of 110-150° C. to obtain a cationic dyeable flame-retardant compound.
[0021] Step 2. Synthesis of cationic dyeable halogen-free flame retardant polyester chips
[0022] Add terephthalic acid (PTA), the product of step 1, and ethylene glycol (EG) in a molar ratio of 1:0.02:1.15 into the esterification tank, stir and raise the temperature of the esterification tank to 230°C, and control the temperature inside the esterification tank. When the pressure reaches 200kPa, react for 1 hour to make the esterification rate reach more than 90% to end the esterification, release ...
Embodiment 2
[0026] Step 1. Synthesis of Cationic Dyeable and Flame Retardant Compounding Agent
[0027] Sodium isophthalic acid sulfonate, 2-carboxyethyl hypophosphorous acid (CEPPA) and deionized water in a molar ratio of 1:2:20 were added into a glass reaction vessel, heated in a water bath to 60°C, and reacted for 3 hours. After the reaction is finished, the reaction product is filtered out, and dried at a temperature of 130° C. to obtain a cationic dyeable flame-retardant compound.
[0028] Step 2. Synthesis of cationic dyeable halogen-free flame retardant polyester chips
[0029] Add terephthalic acid (PTA), the product of step 1, and ethylene glycol (EG) in a molar ratio of 1:0.04:1.2 into the esterification tank, stir and raise the temperature of the esterification tank to 240°C, and control the temperature inside the esterification tank. When the pressure reaches 300kPa, react for 1.5 hours to make the esterification rate reach more than 95% to end the esterification, release the...
Embodiment 3
[0033] Step 1. Synthesis of Cationic Dyeable and Flame Retardant Compounding Agent
[0034] Sodium isophthalic acid sulfonate, 2-carboxyethyl hypophosphorous acid (CEPPA) and deionized water in a molar ratio of 1:2.5:30 were added into a glass reaction vessel, heated in a water bath to 80°C, and reacted for 5 hours. After the reaction is finished, the reaction product is filtered out, and dried at a temperature of 150° C. to obtain a cationic dyeable flame-retardant compound.
[0035] Step 2. Synthesis of cationic dyeable halogen-free flame retardant polyester chips
[0036]Add terephthalic acid (PTA), the product of step 1, and ethylene glycol (EG) in a molar ratio of 1:0.08:1.25 into the esterification tank, stir and raise the temperature of the esterification tank to 250°C, and control the temperature inside the esterification tank. When the pressure reaches 400kPa, react for 2 hours to make the esterification rate reach more than 99% to end the esterification, release the...
PUM
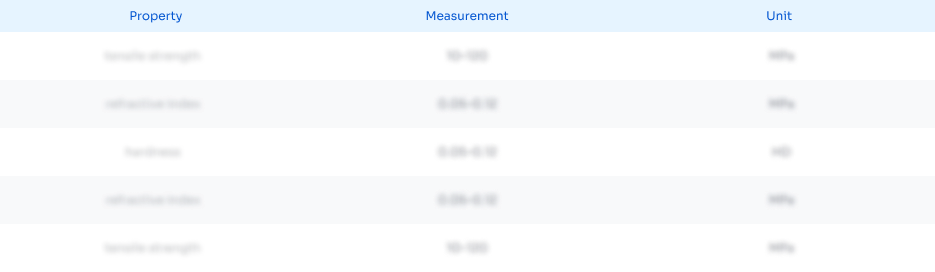
Abstract
Description
Claims
Application Information

- Generate Ideas
- Intellectual Property
- Life Sciences
- Materials
- Tech Scout
- Unparalleled Data Quality
- Higher Quality Content
- 60% Fewer Hallucinations
Browse by: Latest US Patents, China's latest patents, Technical Efficacy Thesaurus, Application Domain, Technology Topic, Popular Technical Reports.
© 2025 PatSnap. All rights reserved.Legal|Privacy policy|Modern Slavery Act Transparency Statement|Sitemap|About US| Contact US: help@patsnap.com