Method for preparing silicate nano-clay/urea resin composite adhesive
A composite adhesive and silicate clay technology, applied in adhesives, adhesive types, non-polymer adhesive additives, etc., can solve the problems of reducing the bonding strength of urea-formaldehyde resin, complicated pre-treatment, and prolonged production cycle, etc., to achieve Improve dispersibility and reactivity, reduce free formaldehyde content, and enhance surface activity
- Summary
- Abstract
- Description
- Claims
- Application Information
AI Technical Summary
Problems solved by technology
Method used
Examples
Embodiment 1
[0027] 1. Thermally activate 50 kg of kaolin at 400°C for 1 hour, immediately add 167 kg of sulfuric acid solution with a mass percent concentration of 15% for quenching, mechanically stir for 5 hours, and let stand for 2 days to remove the lower layer of impurities , to prepare nano-kaolin acidic dispersion;
[0028] 2. While stirring, add a sodium silicate solution with a mass percent concentration of 20% to the acid dispersion of nano-kaolin until the pH of the system is 2, filter, and wash until the conductivity of the filtrate is 300 μS / cm to prepare nano-kaolin / Silica composite filter cake;
[0029] 3. Add deionized water to the nano-kaolin / silicon oxide composite filter cake obtained in step 2, mechanically stir, and be mixed with a nano-kaolin / silicon oxide composite slurry, wherein the quality of the nano-kaolin / silicon oxide composite and deionized water The ratio is 0.1, weigh 110 kg of this slurry, adjust the pH value to 10 with a sodium silicate solution with a...
Embodiment 2
[0032] 1. Thermally activate 50 kg of sepiolite clay at 300°C for 10 hours, immediately add it to 500 kg of hydrochloric acid solution with a concentration of 5% by mass for quenching, ultrasonically disperse it for 1 hour, and let it stand for 6 days. Impurities are precipitated and removed to prepare nano sepiolite acidic dispersion;
[0033] 2. While stirring, add a potassium silicate solution with a mass percent concentration of 10% to the acidic dispersion of the nano sepiolite until the pH of the system is 2.7, filter, and wash until the conductivity of the filtrate is 200 μS / cm to obtain a nanometer sepiolite. Sepiolite / silica composite filter cake;
[0034] 3. Add deionized water to the nano-sepiolite / silicon oxide composite filter cake obtained in step 2, stir mechanically, and prepare a nano-sepiolite / silicon oxide composite slurry, wherein the nano-sepiolite / silicon oxide composite The mass ratio to deionized water is 0.25, weigh 50 kg of this slurry, adjust the pH...
Embodiment 3
[0037] 1. Thermally activate 50 kg of montmorillonite clay at 370°C for 2 hours, immediately add 333 kg of 8% nitric acid solution to quench, mechanically stir for 4 hours, let stand for 3 days, put the lower layer Impurities are precipitated and removed to obtain an acidic dispersion of nano-montmorillonite;
[0038] 2. While stirring, add a sodium silicate solution with a mass percent concentration of 17% to the nano-montmorillonite acidic dispersion until the pH of the system is 3, filter, wash until the conductivity of the filtrate is 275 μS / cm, and obtain Nano-montmorillonite / silica composite filter cake;
[0039] 3. Add deionized water to the nano-montmorillonite / silicon oxide composite filter cake obtained in step 2, stir mechanically, and prepare a nano-montmorillonite / silicon oxide composite slurry, wherein the nano-montmorillonite / silicon oxide composite The mass ratio to deionized water is 0.15, weigh 115 kg of this slurry, adjust the pH value to 9.5 with a sodium ...
PUM
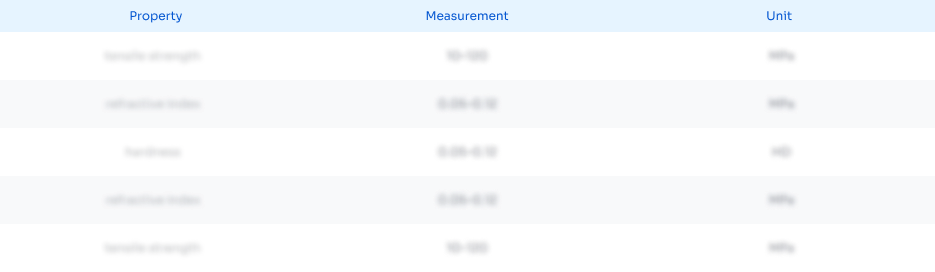
Abstract
Description
Claims
Application Information

- Generate Ideas
- Intellectual Property
- Life Sciences
- Materials
- Tech Scout
- Unparalleled Data Quality
- Higher Quality Content
- 60% Fewer Hallucinations
Browse by: Latest US Patents, China's latest patents, Technical Efficacy Thesaurus, Application Domain, Technology Topic, Popular Technical Reports.
© 2025 PatSnap. All rights reserved.Legal|Privacy policy|Modern Slavery Act Transparency Statement|Sitemap|About US| Contact US: help@patsnap.com