Preparation method Fe/ZSM-5 catalyst for directly decomposing N2O
A ZSM-5 catalyst technology, applied in the field of Fe/ZSM-5 catalyst preparation, can solve the problems of limited iron content, easy precipitation of iron species, poor reproducibility, etc., to reduce iron loss, increase activity, and reduce formation Effect
- Summary
- Abstract
- Description
- Claims
- Application Information
AI Technical Summary
Problems solved by technology
Method used
Image
Examples
Embodiment 1—10
[0039] The catalytic experiments in Examples 1-10 described below were carried out in a U-shaped quartz reaction tube with an inner diameter of 4 mm in the furnace. The reaction takes place in a constant temperature zone in the furnace. The amount of the catalyst is about 50 mg, and the two ends of the catalyst are respectively filled with quartz wool to prevent the loss of the catalyst. The tail gas after the reaction was analyzed by an online quadrupole mass spectrometer.
[0040] Description of the catalyst used
Embodiment 1
[0042] Weigh 2.0 g NH 4 -ZSM-5 type zeolite (Nankai University Catalyst Factory, Si / Al=25, Fe content is lower than 400ppm) is put into U-shaped tube, puts into muffle furnace again and bakes at 550 ℃ for 6 hours, seals, and cools. Put it in a dry box, and 0.0714 grams of FeCl 3 Ball mill for 30 minutes. Seal it, remove it, put it into a tube furnace, heat it to 320° C. in an Ar atmosphere, and keep it for 2 hours. After cooling, the temperature was raised to 200° C. for 1 hour in an Ar atmosphere containing 0.5 vol.% water vapor for hydrolysis. and then in O 2 The temperature was raised to 550° C. in the atmosphere and kept for two hours to obtain a zeolite catalyst with Fe / Al=0.33. The sample number is A.
Embodiment 2
[0044] A part of the catalyst A obtained in Example 1 was taken out, put into a U-shaped tube, and heated to 900° C. in an Ar atmosphere, and kept for 2 hours. The sample number is B.
PUM
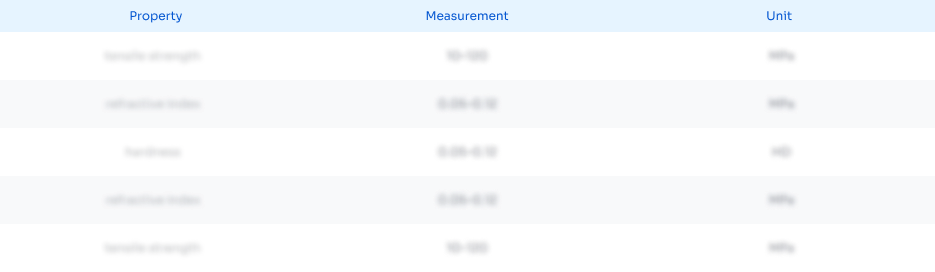
Abstract
Description
Claims
Application Information

- R&D Engineer
- R&D Manager
- IP Professional
- Industry Leading Data Capabilities
- Powerful AI technology
- Patent DNA Extraction
Browse by: Latest US Patents, China's latest patents, Technical Efficacy Thesaurus, Application Domain, Technology Topic, Popular Technical Reports.
© 2024 PatSnap. All rights reserved.Legal|Privacy policy|Modern Slavery Act Transparency Statement|Sitemap|About US| Contact US: help@patsnap.com