Smelting technique for cast of wind energy apparatus
A technology for wind energy equipment and castings, which is applied in the field of smelting process of wind energy equipment castings, can solve the problems that the chemical composition and internal microscopic structure of the castings do not meet the requirements, it is difficult to meet the mechanical properties of the wind energy equipment, and the dimensional accuracy is affected. The effect of aging heat treatment, increasing the number, and reducing the process
- Summary
- Abstract
- Description
- Claims
- Application Information
AI Technical Summary
Problems solved by technology
Method used
Image
Examples
Embodiment Construction
[0011] according to figure 1 In the smelting process shown in the following examples, ingredients are smelted according to the maximum capacity of 12 tons of a 10-ton melting electric furnace.
[0012] name
new iron
scrap steel
Carburizer
Grade
Q8
20
Si75
Mn65
Proportion
85%
15%
0.22%
Adjustment after desulfurization
Adjustment after desulfurization
[0013] Among them, the mass percentage of C element contained in new iron is 4.4%, the mass percentage of Si element is 0.75%, the mass percentage of Mn element is 0.09%, the mass percentage of P element is 0.025%, and the mass percentage of S element is 0.018%. , the rest is Fe element, the mass percentage of C element contained in scrap steel is 0.22%, the mass percentage of Si element is 0.18%, the mass percentage of Mn element is 0.27%, the mass percentage of P element is 0.025%, the mass perce...
PUM
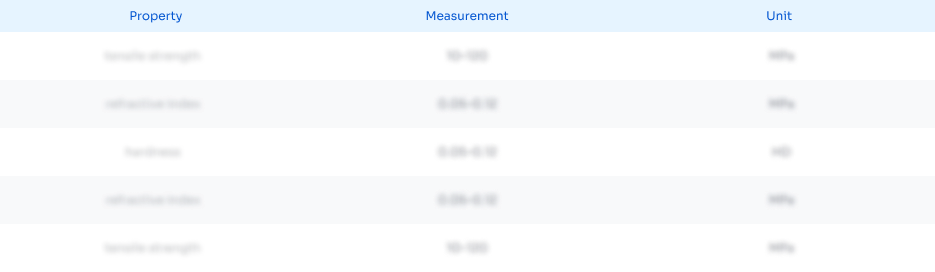
Abstract
Description
Claims
Application Information

- R&D
- Intellectual Property
- Life Sciences
- Materials
- Tech Scout
- Unparalleled Data Quality
- Higher Quality Content
- 60% Fewer Hallucinations
Browse by: Latest US Patents, China's latest patents, Technical Efficacy Thesaurus, Application Domain, Technology Topic, Popular Technical Reports.
© 2025 PatSnap. All rights reserved.Legal|Privacy policy|Modern Slavery Act Transparency Statement|Sitemap|About US| Contact US: help@patsnap.com