Method for producing martensitic stainless steel seamless steel pipe
A martensitic stainless steel, seamless steel pipe technology, used in forming tools, rolling mill control devices, metal rolling, etc., can solve the problems of poor surface quality, difficult processing, rough surface, etc., and achieve small tolerances on outer diameter and wall thickness , to prevent uneven deformation, the effect of good surface quality
- Summary
- Abstract
- Description
- Claims
- Application Information
AI Technical Summary
Problems solved by technology
Method used
Examples
Embodiment 1
[0027] The piercing step of the present invention is a continuous, equal-diameter hot piercing process, and the plug in the hot piercing process is a non-wearing plug, and immediately enters the cold rolling step after the hot piercing, and the cold rolling step adopts a large deformation Amount, single pass is 1.4 ~ 1.6mm, at the same time requires the amount of wall reduction of waste tube: the amount of diameter reduction is greater than 1:3.
[0028] The inventor used a 90×7.5mm waste pipe to roll it into a 73×6mm seamless steel pipe, and the sample size was 5 pieces. The specific data are shown in the table below: Unit: mm
[0029] serial number Size before rolling Rolled products Outer diameter size (four points) Wall thickness tolerance (four points) 1 90×7.5 73×6 73.32,73.1,72.7,72.9 6.25,6.35,6.28,6.05 2 90×7.5 73×6 73.28,73.14,72.7,72.85 6.4,6.31,6.11,5.68 3 90×7.5 73×6 73.35,73.2,73.01,72.9 6.3,6.02,5.92,5.73 4 90×7.5 73...
Embodiment 2
[0031] The main difference between this embodiment and the above embodiments lies in the pickling step in the production process of seamless steel pipes. In the production method of the present invention, the pickling solution used in the pickling step is 20-30% sulfuric acid solution, and , 0.5-5% NaCl and 1-10% NaNO are also added to the pickling solution 3 As a sustained release agent, in addition, in the pickling step, the pickling solution is heated to a temperature of 50-80°C. This cleans the scale surface and leaves it smooth without over-pickling.
Embodiment approach
[0032] For this specific implementation, the applicant of the present invention has also carried out multiple tests and obtained the following data to prove the beneficial effect of the present invention.
[0033] Pickling record of L8013Cr
[0034] time Steel pipe size mm Solution composition temperature °C time Effect
PUM
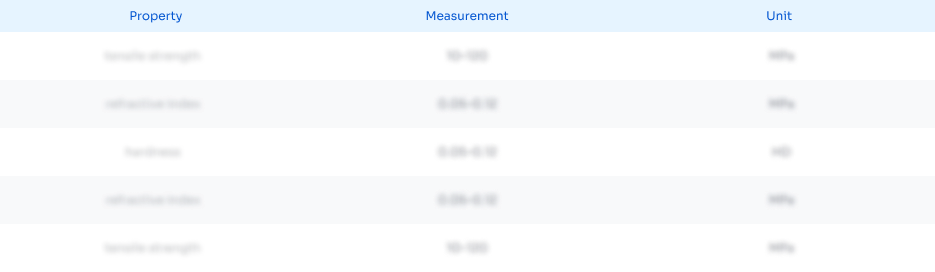
Abstract
Description
Claims
Application Information

- Generate Ideas
- Intellectual Property
- Life Sciences
- Materials
- Tech Scout
- Unparalleled Data Quality
- Higher Quality Content
- 60% Fewer Hallucinations
Browse by: Latest US Patents, China's latest patents, Technical Efficacy Thesaurus, Application Domain, Technology Topic, Popular Technical Reports.
© 2025 PatSnap. All rights reserved.Legal|Privacy policy|Modern Slavery Act Transparency Statement|Sitemap|About US| Contact US: help@patsnap.com