Big thickness BFe30-1-1/35CrMo explosive welding high intensity high corrosion resistance composite board
An explosive welding, large-thickness technology, applied in welding equipment, non-electric welding equipment, manufacturing tools, etc., can solve the problems of long non-bonding area of the detonating end composite plate, low impact toughness, excessive melting of the composite plate and welding recombination rate.
- Summary
- Abstract
- Description
- Claims
- Application Information
AI Technical Summary
Problems solved by technology
Method used
Image
Examples
Embodiment Construction
[0016] BFe30-1-1 / 35CrMo explosion welding of high strength and high corrosion resistance composite plate explosion welding.
[0017] 1. Specifications and properties of base-complex board materials. BFe30-1-1 is a composite board with strong corrosion resistance, with a thickness of 15mm, a length of 2080mm and a width of 2060mm. The base plate is made of 35CrMo alloy structural steel with high lasting strength and creep strength at high temperature, its thickness is 70mm, and its length and width are both 2000mm.
[0018] Chemical composition of BFe30-1-1:
[0019]
[0020] 2. Explosive welding explosive formula. The present invention adopts emulsion explosive as the main raw material, and adds 30% salt, 5% perlite, 2% sawdust and other substances, and the explosive detonation speed is about 1000m / s.
[0021] 3. Determination of charge thickness and gap. The gap between the compound plate and the base plate is 12mm, and the thickness of the charge is about 8cm.
[002...
PUM
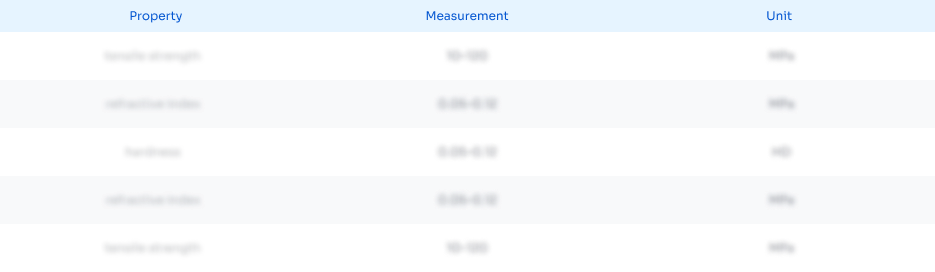
Abstract
Description
Claims
Application Information

- R&D
- Intellectual Property
- Life Sciences
- Materials
- Tech Scout
- Unparalleled Data Quality
- Higher Quality Content
- 60% Fewer Hallucinations
Browse by: Latest US Patents, China's latest patents, Technical Efficacy Thesaurus, Application Domain, Technology Topic, Popular Technical Reports.
© 2025 PatSnap. All rights reserved.Legal|Privacy policy|Modern Slavery Act Transparency Statement|Sitemap|About US| Contact US: help@patsnap.com