Method for preparing acrylics-protein-copper salt composite antistatic fiber
An antistatic fiber and a manufacturing method technology are applied in the manufacturing field of acrylic fiber-protein-copper salt composite antistatic fiber, which can solve the problems of increased production cost and high particle fineness requirements, and achieves low production cost, good antistatic performance, high value-added effects
- Summary
- Abstract
- Description
- Claims
- Application Information
AI Technical Summary
Problems solved by technology
Method used
Examples
Embodiment 1
[0023] Add gelatin and cuprous iodide to a NaSCN aqueous solution with a concentration of 51.3% in a mass ratio of 4.5:1, and continue stirring for about 1 hour until the system turns into a lavender paste substance; add the prepared paste substance to a concentration of 51.3% % NaSCN aqueous solution, stirred in a 70°C constant temperature water bath for about 30 minutes until all solid substances were completely dissolved; added PAN powder with a viscosity average molecular weight of 90,000 to the above solution, and kept stirring in a 60°C constant temperature water bath for 4 hours to make the protein-copper The weight ratio of the salt complex to polyacrylonitrile is 11:89, the content of PAN accounts for 13% (percentage by gravity) of the spinning solution, then the temperature of the solution is lowered to 60°C and left to stand at constant temperature for 8h for defoaming;
[0024] The spinning slurry enters the spinneret hole and is sprayed out through a metering pump,...
Embodiment 2
[0026] Add gelatin and cuprous iodide to a NaSCN aqueous solution with a concentration of 51.3% in a mass ratio of 2.5:1, and continue stirring for about 1 hour until the system turns into a lavender paste substance; add the prepared paste substance to a concentration of 51.3% % NaSCN aqueous solution, stirred in a constant temperature water bath at 70°C for about 30 minutes until all solid substances were completely dissolved; added PAN powder with a viscosity average molecular weight of 120,000 to the above solution, and continued to stir in a constant temperature water bath at 60°C for 4 hours to make the protein-copper The weight ratio of the salt complex to polyacrylonitrile is 7:93, and the content of PAN accounts for 13% (percentage by gravity) of the spinning solution, then the temperature of the solution is lowered to 60° C. and left at a constant temperature for 8 hours for defoaming;
[0027]The spinning slurry enters the spinneret hole through the metering pump and ...
Embodiment 3
[0029] Add gelatin and cuprous iodide to a NaSCN aqueous solution with a concentration of 51.3% in a mass ratio of 1:1, and continue stirring for about 1 hour until the system turns into a lavender paste substance; add the prepared paste substance to a concentration of 51.3% % NaSCN aqueous solution, stirred in a constant temperature water bath at 70°C for about 30 minutes until all solid substances were completely dissolved; added PAN powder with a viscosity average molecular weight of 800,000 to the above solution, and kept stirring in a constant temperature oil bath at 180°C for 4 hours to make the protein- The weight ratio of the copper salt complex to polyacrylonitrile is 9:91, and the content of PAN accounts for 5% (percentage by gravity) of the spinning solution, then the temperature of the solution is reduced to 140°C and left to stand at constant temperature for 12h for defoaming;
[0030] The spinning slurry enters the spinneret hole through the metering pump and is e...
PUM
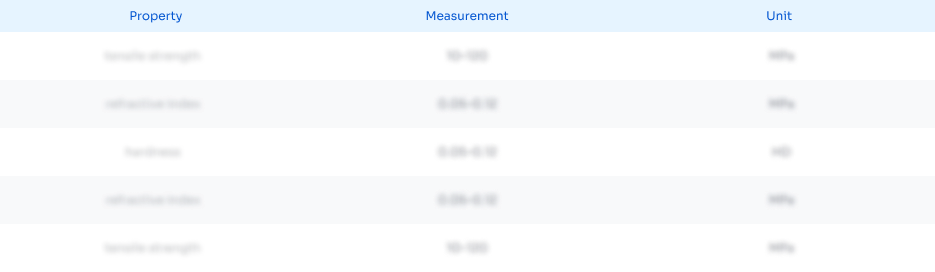
Abstract
Description
Claims
Application Information

- R&D
- Intellectual Property
- Life Sciences
- Materials
- Tech Scout
- Unparalleled Data Quality
- Higher Quality Content
- 60% Fewer Hallucinations
Browse by: Latest US Patents, China's latest patents, Technical Efficacy Thesaurus, Application Domain, Technology Topic, Popular Technical Reports.
© 2025 PatSnap. All rights reserved.Legal|Privacy policy|Modern Slavery Act Transparency Statement|Sitemap|About US| Contact US: help@patsnap.com