Low glue consumption method for making medium density fiberboard
A manufacturing method and fiberboard technology, which can be applied to flat products, household components, household appliances, etc., can solve problems such as environmental pollution, and achieve the effects of reducing the amount of glue applied, the cost of sheet manufacturing, and the amount of formaldehyde released.
- Summary
- Abstract
- Description
- Claims
- Application Information
AI Technical Summary
Problems solved by technology
Method used
Examples
Embodiment 1
[0024] The specific method is as follows:
[0025] 1. Prepare materials
[0026] Drum chippers are used to process raw materials such as small-diameter wood and branch wood into wood chips with specifications of length: 16-30mm, width: 15-30mm, and thickness: 3-6mm. Purify the wood chips through a roller screen to remove unqualified wood chips and bark in the wood chips;
[0027] 2. Fiber preparation
[0028] The qualified wood chips are sent to the wood chip cooking tank through the belt conveyor. Filter the papermaking waste liquid and introduce it into the boiler to prepare saturated steam with a steam pressure of 0.6MPa. Then, the saturated steam is introduced into the wood chip cooking tank to cook and soften the wood chips. The temperature in the cooking tank is 160° C., and the treatment time is 6 minutes. The wood chips after cooking and preheating are sent to the heat mill through the feeding screw for mechanical separation to prepare wood fibers. Before the wood...
Embodiment 2
[0038] The specific method is as follows:
[0039] 1. Prepare materials
[0040] Drum chippers are used to process raw materials such as small-diameter wood and branch wood into wood chips with specifications of length: 16-30mm, width: 15-30mm, and thickness: 3-6mm. Purify the wood chips through a roller screen to remove unqualified wood chips and bark in the wood chips;
[0041] 2. Fiber preparation
[0042] The qualified wood chips are sent to the wood chip cooking tank through the belt conveyor. Filter the papermaking waste liquid and introduce it into the boiler to prepare saturated steam with a steam pressure of 0.7MPa. Then, the saturated steam is introduced into the wood chip cooking tank to cook and soften the wood chips. The temperature in the cooking tank is 175° C., and the treatment time is 8 minutes. The wood chips after cooking and preheating are sent to the heat mill through the feeding screw for mechanical separation to prepare wood fibers. Before the wood...
PUM
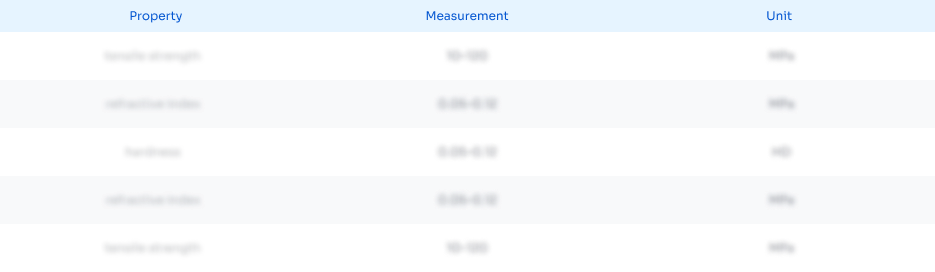
Abstract
Description
Claims
Application Information

- R&D
- Intellectual Property
- Life Sciences
- Materials
- Tech Scout
- Unparalleled Data Quality
- Higher Quality Content
- 60% Fewer Hallucinations
Browse by: Latest US Patents, China's latest patents, Technical Efficacy Thesaurus, Application Domain, Technology Topic, Popular Technical Reports.
© 2025 PatSnap. All rights reserved.Legal|Privacy policy|Modern Slavery Act Transparency Statement|Sitemap|About US| Contact US: help@patsnap.com