Method for manufacturing iron base alloy electromagnetic-interference-resistance
An anti-electromagnetic interference, iron-based alloy technology, applied in the field of magnetic materials, can solve the problems of unfavorable industrial cost control, difficult and precise control of components, long time, etc., to achieve the effects of good crystallinity, excellent performance, and reduced waste.
- Summary
- Abstract
- Description
- Claims
- Application Information
AI Technical Summary
Problems solved by technology
Method used
Examples
Embodiment 1
[0017] 1) Put the raw materials in the mass ratio: 85% iron, 9.6% silicon, and 5.4% aluminum for melting in an intermediate frequency vacuum induction furnace with alumina as the crucible, and vacuumize to 10 -1 Pa, and then send electricity to preheat the charge to remove the adsorbed gas, moisture and organic matter of the charge. At this time, the vacuum degree in the furnace drops, and then it is evacuated again to 10 -2 ~10 -3 Pa, filled with high-purity argon until the pressure in the furnace is 0.5×10 5 Pa, high-power transmission to completely melt the charge, and then low-power refining for 10 minutes before pouring.
[0018] 2) Put the smelted master alloy into the rapid quenching equipment, and the alloy ingot is remelted under the protection of high-purity argon, and then quickly poured onto the high-speed rotating roller to obtain a rapidly condensed thin strip. 15m / s;
[0019] 3) put the strip into a ball mill for flattening treatment to obtain a flat powder,...
Embodiment 2
[0023] 1) Put the raw materials in the mass ratio: iron 87%, silicon 8.6%, aluminum 4.4% into an intermediate frequency vacuum induction furnace with alumina as a crucible for melting, and vacuumize to 10 -1 Pa, and then send electricity to preheat the charge to remove the adsorbed gas, moisture and organic matter of the charge. At this time, the vacuum degree in the furnace drops, and then it is evacuated again to 10 -2 Above Pa, fill the furnace with high-purity argon until the pressure in the furnace is 0.5×10 5 Pa, high-power transmission to completely melt the charge, and then low-power refining for 10 minutes before pouring.
[0024] 2) The smelted master alloy is put into the rapid quenching equipment, and the alloy ingot is remelted under the protection of high-purity argon, and then quickly poured onto the high-speed rotating roller to obtain a rapidly condensed thin strip. The quenching speed is 27.5m / s;
[0025] 3) Put the strip into a ball mill for flattening tr...
Embodiment 3
[0029] 1) Put the raw materials in the mass ratio: 82% iron, 10% silicon, and 8% aluminum for melting in an intermediate frequency vacuum induction furnace with alumina as the crucible, and vacuumize to 10 -1Pa, and then send electricity to preheat the charge to remove the adsorbed gas, moisture and organic matter of the charge. At this time, the vacuum degree in the furnace drops, and then it is evacuated again to 10 -2 Above Pa, fill the furnace with high-purity argon until the pressure in the furnace is 0.5×10 5 Pa, high-power transmission to completely melt the charge, and then low-power refining for 10 minutes before pouring.
[0030] 2) The smelted master alloy is put into the rapid quenching equipment, and the alloy ingot is remelted under the protection of high-purity argon, and then quickly poured onto the high-speed rotating roller to obtain a rapidly condensed thin strip with a quenching speed of 15m / s;
[0031] 3) Put the strip or sheet into a ball mill for fla...
PUM
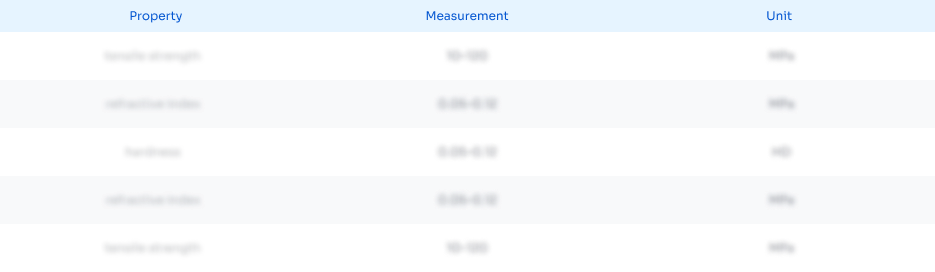
Abstract
Description
Claims
Application Information

- R&D
- Intellectual Property
- Life Sciences
- Materials
- Tech Scout
- Unparalleled Data Quality
- Higher Quality Content
- 60% Fewer Hallucinations
Browse by: Latest US Patents, China's latest patents, Technical Efficacy Thesaurus, Application Domain, Technology Topic, Popular Technical Reports.
© 2025 PatSnap. All rights reserved.Legal|Privacy policy|Modern Slavery Act Transparency Statement|Sitemap|About US| Contact US: help@patsnap.com