Mechanical alloyed method for manufacturing CrW alloy powder
A technology of mechanical alloying and alloy powder, applied in the field of mechanical alloying to manufacture CrW alloy powder, to achieve the effect of high solid solubility
- Summary
- Abstract
- Description
- Claims
- Application Information
AI Technical Summary
Problems solved by technology
Method used
Image
Examples
Embodiment 1
[0025] After mixing 91% tungsten powder and 9% chromium powder, put it into a horizontal nylon ball mill; add anhydrous ethanol according to 2% of the total mass of tungsten powder and chromium powder in the ball mill, and press tungsten powder and chromium powder into the ball mill. Add cemented carbide grinding balls to 50 times the total mass; use nitrogen to remove the air in the ball mill tank, seal the ball mill tank, open the circulating cooling water in the ball mill tank, and ball mill for 100 hours; after the ball mill is over, let it stand for cooling and take out the powder material. The morphology of the alloy powder and its X-ray diffraction (XRD) analysis results are shown in Figure 1. It can be seen from the figure that the morphology of the original powder particles has changed a lot, and the particle shape has become an irregular flat shape, and the particles are finely dispersed. From the diffraction analysis results, it is known that chromium has been comp...
Embodiment 2
[0027] After mixing 80% of tungsten powder and 20% of chromium powder, put it into a horizontal nylon ball mill; in the ball mill, add analytical pure acetone according to 4% of the total mass of the powder, and add stainless steel according to 80 times of the total mass of the powder. Grinding balls, the diameters of different grinding balls are arranged at 1:1; use argon to remove the air in the ball mill tank, and seal the ball mill tank; open the circulating cooling water of the ball mill tank, and ball mill for 80 hours; after the ball mill, let stand for cooling Then remove the powder. The morphology of the alloy powder and its XRD analysis results are shown in Figure 2. It can be seen from the figure that the morphology of the original powder particles has changed a lot, and the particle shape has become an irregular flat shape, and the particles are finely dispersed. From the diffraction analysis results, it is known that chromium has been completely dissolved into tu...
Embodiment 3
[0029] After mixing 87.5% of tungsten powder and 12.5% of chromium powder, put it into a vertical stainless steel ball mill; add absolute ethanol according to 5% of the total mass of the powder, and add it according to 100 times of the total mass of the powder. Agate grinding ball, the diameter of different grinding balls is 1:1; slowly vacuumize the ball mill to 10 -1 Pa, open the cooling water of the ball mill tank, and mill the ball for 60 hours; after the ball mill is over, let it stand for cooling and take out the powder. The morphology of the alloy powder and its XRD analysis results are shown in Figure 3. It can be seen from the figure that the morphology of the original powder particles has changed a lot, and the particle shape has become an irregular flat shape, and the particles are finely dispersed. From the diffraction analysis results, it is known that chromium has been completely dissolved into tungsten to form tungsten-chromium alloy powder.
PUM
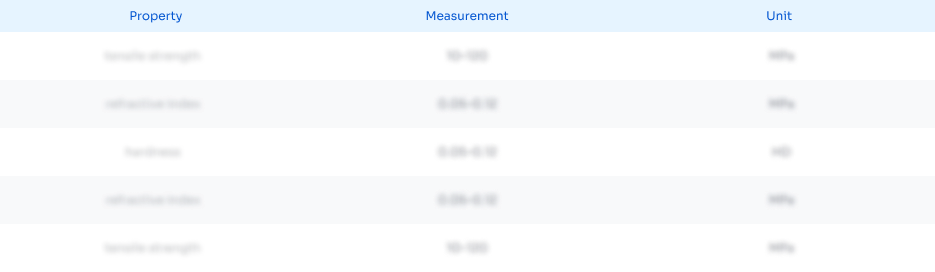
Abstract
Description
Claims
Application Information

- R&D
- Intellectual Property
- Life Sciences
- Materials
- Tech Scout
- Unparalleled Data Quality
- Higher Quality Content
- 60% Fewer Hallucinations
Browse by: Latest US Patents, China's latest patents, Technical Efficacy Thesaurus, Application Domain, Technology Topic, Popular Technical Reports.
© 2025 PatSnap. All rights reserved.Legal|Privacy policy|Modern Slavery Act Transparency Statement|Sitemap|About US| Contact US: help@patsnap.com