Method for preparing Ti3 AlC2 powder
A technology of powder and process method, which is applied in the field of chemical synthesis material preparation, and can solve the problems of restricting widespread use and high preparation cost
- Summary
- Abstract
- Description
- Claims
- Application Information
AI Technical Summary
Problems solved by technology
Method used
Image
Examples
Embodiment 1
[0013] Weigh 6.9434g of Ti powder with a purity greater than 99wt% and 1.6954g of Al powder with a purity greater than 99.99wt% in a molar ratio of 3:1.3:2; Al powder has been included in the 30mol% portion of Al as an additive; % C powder 1.1611g. Then add WC balls according to the ball-to-material ratio of 20:1, and put them into a stainless steel ball mill jar; then seal it, fill it with argon gas, and carry out mechanical alloying; the ball milling time is 60 hours, and the rotation speed is 225rpm. Then put the mechanically alloyed powder into a crucible, and anneal it under the protection of argon. The annealing temperature is 950°C, and the annealing time is 2 hours; 3 AlC 2 Powder.
Embodiment 2
[0015] Weigh 7.0294 g of Ti powder with a purity greater than 99 wt%, 1.3203 g of Al powder with a purity greater than 99.99 wt%, 1.1755 g of C powder with a purity greater than 99.99% in a molar ratio of 3:1:2, and then add Si powder with a purity greater than 99 wt%. Powder 0.2748g. Then add WC balls according to the ball-to-material ratio of 20:1, and put them into a stainless steel ball mill tank; then seal it, fill it with argon gas, and carry out mechanical alloying; the ball milling time is 60 hours, and the rotation speed is 250 rpm. Then transfer the mechanically alloyed powder into a crucible, and perform annealing treatment under the protection of argon. The annealing temperature is 950°C, and the annealing time is 2 hours; then it is cooled to room temperature with the furnace, and the obtained product is Ti 3 AlC 2 Powder.
Embodiment 3
[0017] Weigh 6.7462g of Ti powder with a purity greater than 99wt% and 1.9007g of Al powder with a purity greater than 99.99wt% in a molar ratio of 3:1.5:2; Al powder has been included in the 50mol% portion of Al as an additive; there is also a purity greater than 99.99g % C powder 1.1281g. Then add WC balls according to the ball-to-material ratio of 30:1, and put them into a stainless steel ball mill jar; then seal it, fill it with argon gas, and carry out mechanical alloying; the ball milling time is 60 hours, and the rotation speed is 250rpm. Then put the mechanically alloyed powder into a crucible, and anneal it under the protection of argon. The annealing temperature is 900°C, and the annealing time is 2 hours; then it is cooled to room temperature with the furnace, and the obtained product is Ti 3 AlC 2 Powder.
[0018] The resulting product is detected by X-ray diffraction analysis, in the X-ray diffraction spectrum, see figure 1 , it was found that a characteristic ...
PUM
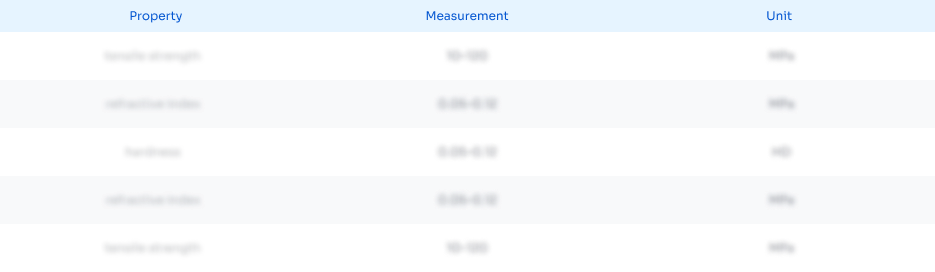
Abstract
Description
Claims
Application Information

- R&D Engineer
- R&D Manager
- IP Professional
- Industry Leading Data Capabilities
- Powerful AI technology
- Patent DNA Extraction
Browse by: Latest US Patents, China's latest patents, Technical Efficacy Thesaurus, Application Domain, Technology Topic, Popular Technical Reports.
© 2024 PatSnap. All rights reserved.Legal|Privacy policy|Modern Slavery Act Transparency Statement|Sitemap|About US| Contact US: help@patsnap.com