Compound semiconductor multilayer structure, hall device, and hall device manufacturing method
a multi-layer structure and compound semiconductor technology, applied in the direction of galvano-magnetic hall-effect devices, instruments, galvano-magnetic devices, etc., can solve the problems of large mismatching between crystal lattice spacings in substrates, degradation of crystallinity and mobility, etc., to achieve high mobility characteristics, ease the mismatch, and high resistance
- Summary
- Abstract
- Description
- Claims
- Application Information
AI Technical Summary
Benefits of technology
Problems solved by technology
Method used
Image
Examples
example 1
[0139] On a GaAs substrate two inches in diameter, are successively formed by the molecular beam epitaxy (MBE) 600 nm Al0.55Ga0.45AsSb as the first compound semiconductor layer, 50 nm InAs as the active layer, 60 nm Al0.55Ga0.45AsSb as the second compound semiconductor layer, and 6 nm GaAsSb as the third compound semiconductor layer.
[0140] The Sb composition was calculated, according to Vegard's law, from accurate lattice constants obtained by a high resolution X-ray diffraction method based on a 4-crystal method using Ge (220) single crystals. The electric characteristics such as the electron mobility were evaluated from the measurement of the Hall effect by van der Pauw method.
[0141] Table 2 summarizes the thus obtained lattice constant difference, electron mobility and sheet resistance in accordance with the Sb compositions.
TABLE 2latticeconstantelectronsheetdifferencemobilityresistanceSbx(%)(cm2 / Vs)(Ω)0.8850.10191125280.9020.23197054770.9180.35206014280.9290.43213043990.9380...
example 2
[0152] On a GaAs substrate two inches in diameter, are successively formed by the molecular beam epitaxy (MBE) 600 nm Al0.55Ga0.45AsSb as the first compound semiconductor layer, 70 nm InAs as the active layer, 60 nm Al0.55Ga0.45AsSb as the second compound semiconductor layer, and 6 nm GaAsSb as the third compound semiconductor layer.
[0153] The Sb composition was calculated, according to Vegard's law, from accurate lattice constants obtained by the high resolution X-ray diffraction method based on the 4-crystal method using Ge (220) single crystals. The electric characteristics such as the electron mobility were evaluated from the measurement of the Hall effect by van der Pauw method.
[0154] Table 4 summarizes the thus obtained lattice constant difference, electron mobility and sheet resistance in accordance with the Sb compositions.
TABLE 4latticeconstantelectronsheetdifferencemobilityresistanceSbx(%)(cm2 / Vs)(Ω)0.8860.11165695350.9010.22173524910.9190.36188094340.9370.49201043900....
example 3
[0157] On a GaAs substrate two inches in diameter, are successively formed by the molecular beam epitaxy (MBE) 600 nm Al0.55Ga0.45AsSb as the first compound semiconductor layer, 35 nm InAs as the active layer, 60 nm Al0.55Ga0.45AsSb as the second compound semiconductor layer, and 6 nm GaAsSb as the third compound semiconductor layer.
[0158] The Sb composition was calculated, according to Vegard's law, from accurate lattice constants obtained by the high resolution X-ray diffraction method based on the 4-crystal method using Ge (220) single crystals. The electric characteristics such as the electron mobility were evaluated from the measurement of the Hall effect by van der Pauw method.
[0159] Table 5 summarizes the thus obtained lattice constant difference, electron mobility and sheet resistance in accordance with the Sb compositions.
TABLE 5latticeconstantelectronsheetdifferencemobilityresistanceSbx(%)(cm2 / Vs)(Ω)0.8920.15196057430.9040.24205186560.9180.35216735900.9340.47228455210....
PUM
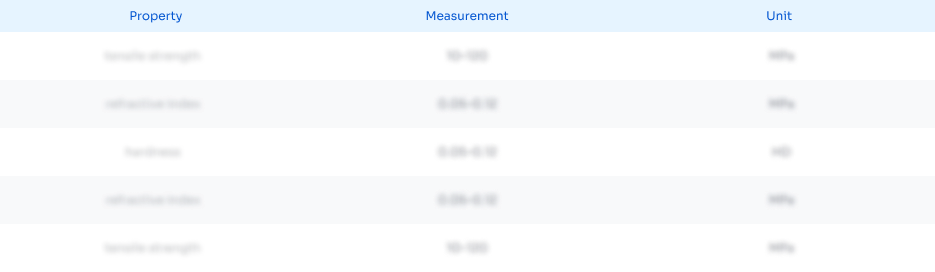
Abstract
Description
Claims
Application Information

- R&D
- Intellectual Property
- Life Sciences
- Materials
- Tech Scout
- Unparalleled Data Quality
- Higher Quality Content
- 60% Fewer Hallucinations
Browse by: Latest US Patents, China's latest patents, Technical Efficacy Thesaurus, Application Domain, Technology Topic, Popular Technical Reports.
© 2025 PatSnap. All rights reserved.Legal|Privacy policy|Modern Slavery Act Transparency Statement|Sitemap|About US| Contact US: help@patsnap.com