Method for manufacturing monochloroacetic acid based on continuous catalytic chlorination process
A technology of chloroacetic acid and chlorination method, which is applied in chemical instruments and methods, preparation of organic compounds, organic chemistry, etc., can solve the problems of lowering product grade, complicated preparation process, and many operation steps, and achieves mild reaction conditions and catalytic Concentrated performance and high product selectivity
- Summary
- Abstract
- Description
- Claims
- Application Information
AI Technical Summary
Problems solved by technology
Method used
Image
Examples
Embodiment 1
[0025] The acetic acid of 56.3Kg is charged in the chlorination reactor, and the low-temperature tank is cooled to the set temperature and then the pump is circulated. Simultaneously, after the reactor is heated to 100 DEG C with a temperature controller, add 3% catalyst acetic anhydride, co-catalyst concentrated sulfuric acid 0.8% (with acetic acid as the benchmark), start to feed chlorine, record the time of feeding and discharging, and regularly sample analyze. The unit consumption of chlorine gas is 71.2Kg, the content of chloroacetic acid is 99.22%, and the content of dichloroacetic acid is 0.42%. The finished product of chloroacetic acid can produce 1114kg per day, and the continuous operation of the device is normal.
Embodiment 2
[0027] In the same device as in Example 1, add the same amount of acetic acid as in Example 1 successively, and turn on the pump to circulate after the low temperature tank is cooled to the set temperature. Simultaneously, after the reactor is heated to 105° C. with a temperature controller, add 5% catalyzer, 0.8% co-catalyst concentrated sulfuric acid (taking acetic acid as a benchmark), start to feed chlorine, record the feeding and discharging time, and regularly sample and analyze. Among them, the unit consumption of chlorine gas is 79.1Kg, the content of chloroacetic acid is 99.10%, and the content of dichloroacetic acid is 0.47%. The finished product of chloroacetic acid can produce 1034kg per day, and the continuous operation of the device is normal.
Embodiment 3
[0029] In the same device of embodiment 1, add the acetic acid of 61.3kg and the catalyst of 8% successively, start logical chlorine, record the time of feeding and discharging, regular sampling analysis. The unit consumption of chlorine gas is 76.3Kg, the content of chloroacetic acid is 99.65%, and the content of dichloroacetic acid is 0.26%. The finished product of chloroacetic acid can produce 1100kg per day, and the continuous operation of the device is normal.
PUM
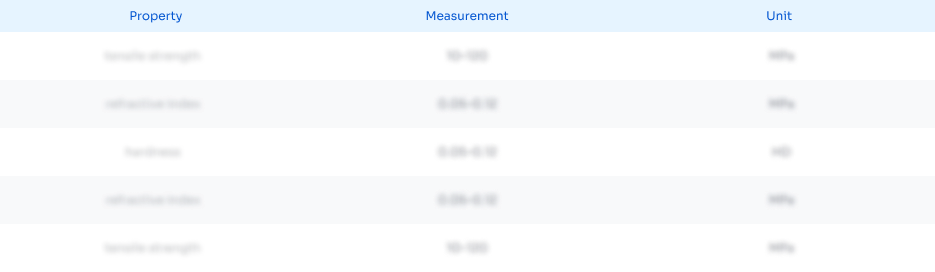
Abstract
Description
Claims
Application Information

- R&D Engineer
- R&D Manager
- IP Professional
- Industry Leading Data Capabilities
- Powerful AI technology
- Patent DNA Extraction
Browse by: Latest US Patents, China's latest patents, Technical Efficacy Thesaurus, Application Domain, Technology Topic, Popular Technical Reports.
© 2024 PatSnap. All rights reserved.Legal|Privacy policy|Modern Slavery Act Transparency Statement|Sitemap|About US| Contact US: help@patsnap.com