Method for forming high-frequency IC wire and inductive coil pack
A technology of inductance coils and wires, which is applied in the direction of electrical components, semiconductor/solid-state device manufacturing, circuits, etc., and can solve problems such as process defects, wires cannot provide current carrying function, and limit the application of copper metal.
- Summary
- Abstract
- Description
- Claims
- Application Information
AI Technical Summary
Problems solved by technology
Method used
Image
Examples
Embodiment Construction
[0012] see Figure 2A First, a substrate 10 is provided, and a component layer 12 is formed on the substrate 10. The component layer 12 is different depending on different semiconductor structures. The component layer 12 includes active regions, isolation structures and passive components, etc., such as in gold In an oxygen-semiconductor field-effect transistor (MOSFET), the component layer 12 can be a gate oxide layer, a gate stack structure of a polysilicon layer, and source / drain structures; Resist 14, the photoresist 14 formed here is a negative photoresist, that is, the exposed part will become cross-linked and polymerized due to photochemical reaction, and harden after development. Remains on the surface of the substrate, the unexposed part is dissolved by the developer.
[0013] see next Figure 2B A masking layer 16 is covered on the photoresist 14, and after the alignment and exposure steps, a postexposure bake (postexposure bake) of ammonia gas is performed to redu...
PUM
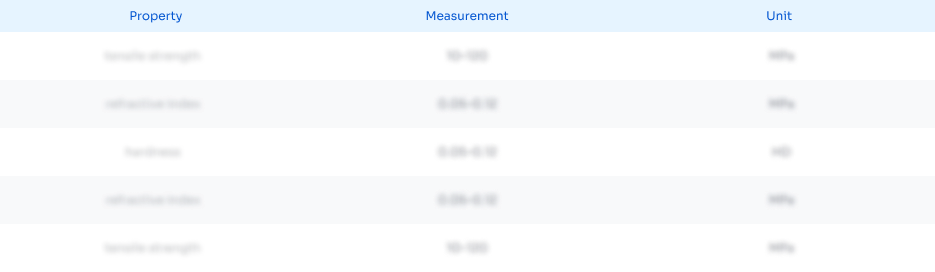
Abstract
Description
Claims
Application Information

- R&D
- Intellectual Property
- Life Sciences
- Materials
- Tech Scout
- Unparalleled Data Quality
- Higher Quality Content
- 60% Fewer Hallucinations
Browse by: Latest US Patents, China's latest patents, Technical Efficacy Thesaurus, Application Domain, Technology Topic, Popular Technical Reports.
© 2025 PatSnap. All rights reserved.Legal|Privacy policy|Modern Slavery Act Transparency Statement|Sitemap|About US| Contact US: help@patsnap.com