Soluble thermokalite polyester fibre preparation
A polyester fiber and soluble technology, which is used in the manufacture of modified polyester fibers, can solve the problems of high-speed spinning, serious chip bonding, and low polyester softening point.
- Summary
- Abstract
- Description
- Claims
- Application Information
AI Technical Summary
Problems solved by technology
Method used
Examples
Embodiment 1
[0026] The preparation of easy alkali hydrolysis polyester: 1000kg purified terephthalic acid (PTA), 60kg (5.67% mole) isophthalic acid (IPA), 500kg ethylene glycol (EG), polymerization catalyst antimony trioxide 0.32kg input Beating in the beating tank, after beating evenly, enter the esterification tank continuously, and esterify at a temperature of 250--260°C under normal pressure, after the esterification effluent is 220kg, move it into the polymerization tank, add 140kg (6.0% mole) of 5-sodium sulfonate- Ethylene glycol isophthalate (SIPE), stirring for 30 minutes, adding 120kg (9.0%) of polyethylene glycol (PEG) with an average molecular weight of 4000 and adding tetrakis[β-(3,5-di-tert-butyl -4-hydroxyphenyl) propionic acid] pentaerythritol ester (antioxidant 1010): 0.4kg (0.03%), cobalt acetate 0.2kg (0.015%), trimethyl phosphate 0.2kg (0.015%), stirred for 30 minutes, In low vacuum, the temperature is 240--270 ℃ for pre-condensation, and in high vacuum (less than 100P...
Embodiment 2
[0032] Embodiment 2: As described in Embodiment 1, the difference is that,
[0033] The preparation of the fiber is: under the spinning conditions of screw temperature 286°C, spinning speed 2800 m / min, and wind speed 0.5 m / s, a POY fiber with a fineness of 210dtex / 36f, a strength of 1.19CN / dtex, and an elongation of 145% was obtained. .
[0034] The above-mentioned POY fiber is a DT fiber with a fineness of 105dtex / 36f, a strength of 2.1CN / dtex, and an elongation of 20% under the conditions of a spinning speed of 600 m / min, a drafting temperature of 80°C, a draft ratio of 1.75 times, and a heat setting temperature of 186°C. .
[0035] The DT fiber was subjected to an alkali dissolution experiment with 1.5% sodium hydroxide aqueous solution (bath ratio 50, temperature 100° C.), and it could be completely dissolved within 8 minutes.
Embodiment 3
[0036] Embodiment 3: As described in Example 1, the difference is that the preparation of the fiber is: the spinning condition is that the screw temperature is 286 ° C, the spinning speed is 2800 m / min, and the fineness 210dtex is obtained under the condition of wind speed 0.5 m / s / 36f, POY fiber with strength of 1.19CN / dtex and elongation of 145%.
[0037] The above-mentioned POY fiber is 110dtex / 36f in fineness, 1.80CN / dtex in strength, elongation 24% DTY fibers. The DTY fiber was subjected to an alkali dissolution experiment with 1.5% sodium hydroxide aqueous solution (bath ratio 50, temperature 100° C.), and it could be completely dissolved within 10 minutes.
PUM
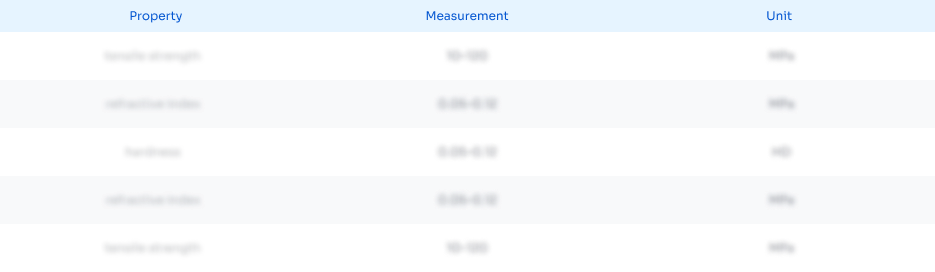
Abstract
Description
Claims
Application Information

- R&D
- Intellectual Property
- Life Sciences
- Materials
- Tech Scout
- Unparalleled Data Quality
- Higher Quality Content
- 60% Fewer Hallucinations
Browse by: Latest US Patents, China's latest patents, Technical Efficacy Thesaurus, Application Domain, Technology Topic, Popular Technical Reports.
© 2025 PatSnap. All rights reserved.Legal|Privacy policy|Modern Slavery Act Transparency Statement|Sitemap|About US| Contact US: help@patsnap.com