Reversed phase lithium inserting process of preparing poly crystal LiFePO4 nano powder material
A nano-powder, NH4H2PO4 technology, applied in chemical instruments and methods, active material electrodes, inorganic chemistry, etc., can solve problems such as low purity, uneven distribution, high carbon content of materials, and achieve stable precipitation and rapid formation Effect
- Summary
- Abstract
- Description
- Claims
- Application Information
AI Technical Summary
Problems solved by technology
Method used
Image
Examples
Embodiment 1
[0034] Measure 500ml of n-heptane and put it in a beaker, and slowly add 120g of surfactant ST with electromagnetic stirring. Measure 1.5M FeCl 3 40ml of aqueous solution, 1.5mL of glacial acetic acid was added dropwise, and then the mixed liquid was added dropwise into the oil phase liquid of n-heptane, and the uniform solution was an orange-red turbid liquid. Measure 13ml of n-butanol, add dropwise to the turbid liquid, then the liquid becomes clear and transparent, and finally forms a W / O microemulsion liquid. 60ml, 1.5M NH 4 h 2 PO 4Mix with 15ml, 0.5M sodium acetate solution evenly, add evenly and slowly with a burette, the solution system gradually changes from orange-red transparent to orange-red turbid, and finally becomes a white milky dispersion solution system. Heat the solution system to 70°C and keep it warm for 10 minutes, and the oil and water of the solution system are separated. Wash with acetone, soak the aqueous phase, and collect the precipitate. Dry ...
Embodiment 2
[0036] Measure 500ml of n-heptane and put it in a beaker, and slowly add 120g of surfactant ST with electromagnetic stirring. Measure 0.1M FeCl 3 40ml of aqueous solution, 2.5mL of glacial acetic acid was added dropwise, and then the mixed system was added dropwise into the oil phase liquid of n-heptane, and the solution became an orange-red turbid liquid after being uniform. Measure 5ml of n-butanol, add dropwise to the turbid liquid, then the system becomes clear and transparent, and finally forms a W / O microemulsion liquid. 80ml of 0.8M NH 4 h 2 PO 4 Mix evenly with 20ml 0.8M lithium acetate solution, add evenly and slowly with a burette, the solution gradually changes from orange-red transparent to orange-red turbid, and finally becomes a white milky dispersed solution system. Heat the system to 70°C and keep it warm for 10 minutes, and the oil and water of the solution system are separated. Wash with acetone, soak the aqueous phase, then collect the precipitate, and ...
Embodiment 3
[0038] Measure 500ml of n-heptane and put it in a beaker, and slowly add 120g of surfactant ST with electromagnetic stirring. Measure 0.05M FeCl 3 40ml of aqueous solution, 4mL of glacial acetic acid was added dropwise, and then the mixed liquid was added dropwise to the oil phase liquid of n-heptane, the liquid gradually became clear and transparent, and finally directly formed a W / O microemulsion liquid. 60ml 1M NH 4 h 2 PO 4 Mix evenly with 30ml 1M potassium acetate solution, add evenly and slowly with a burette, the solution gradually changes from orange-red transparent to orange-red turbid, and finally becomes a white milky dispersion system. Heat the liquid to 70°C and keep it warm for 10 minutes. The oil and water in the system are separated. Wash with absolute ethanol, soak the water phase, then collect the precipitate, and dry the precipitate at 300°C for 12 hours. The material was then soaked in 1M LiI for 24 hours, filtered, washed and the precipitate collected...
PUM
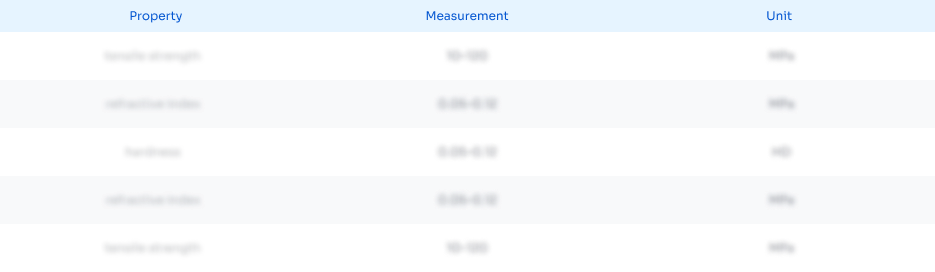
Abstract
Description
Claims
Application Information

- R&D Engineer
- R&D Manager
- IP Professional
- Industry Leading Data Capabilities
- Powerful AI technology
- Patent DNA Extraction
Browse by: Latest US Patents, China's latest patents, Technical Efficacy Thesaurus, Application Domain, Technology Topic, Popular Technical Reports.
© 2024 PatSnap. All rights reserved.Legal|Privacy policy|Modern Slavery Act Transparency Statement|Sitemap|About US| Contact US: help@patsnap.com