Aluminum-erbium alloy welding wire and preparation method thereof
An alloy welding wire and alloy technology, which is applied in welding equipment, metal processing equipment, manufacturing tools, etc., can solve the problems of low corrosion resistance and self-quality stability of alloy welding wire, insufficient performance and quality of welding joints, and complicated processing process. Achieve the effect of high yield, high corrosion resistance and simple processing technology
- Summary
- Abstract
- Description
- Claims
- Application Information
AI Technical Summary
Problems solved by technology
Method used
Examples
Embodiment 1
[0024] First, the corresponding mass fractions of Cu: 10%, Fe: 0.1%, Ti: 1.0%, Mg: 0.8%, Zr: 10%, Cr: 0.01%, Sc: 0.1%, Er: 0.6%, Zn: 2%, and 0.1% of other impurities, and the balance is Al. First, the bulk metal in the alloy composition is processed into powder or chip form, and the Al and intermediate alloy in the alloy composition are in the order of melting point from high to low. Put it into the smelting furnace for smelting, and add a refining agent with a mass of 0.03% of the total alloy at a constant rate, heat it up to 900 ° C, and use electromagnetic stirring to accelerate the dissolution at a power of 200 kw to obtain an aluminum-erbium alloy liquid, and then aluminum The erbium alloy liquid is poured into a holding furnace with a set temperature of 700 °C for heat preservation, and a rotary degasser is used to pass chlorine and argon into the alloy liquid for refining and degassing. When the temperature of the aluminum-erbium alloy liquid is 680 °C, Use a slag remov...
Embodiment 2
[0026] First, weigh the corresponding mass fractions of Cu: 15%, Fe: 0.2%, Ti: 2%, Mg: 1.4%, Zr: 13%, Cr: 0.03%, Sc: 0.3%, Er: 0.8%, Zn: 3%, and 0.1% of other impurities, and the balance is Al. First, the bulk metal in the alloy composition is processed into powder or chip form, and the Al and intermediate alloy in the alloy composition are in the order of melting point from high to low. Put it into a melting furnace for melting, and add a refining agent with a mass of 0.04% of the total alloy at a constant rate, heat it up to 925 ° C, and use electromagnetic stirring to accelerate dissolution at a power of 225 kw to obtain aluminum-erbium alloy liquid, and then aluminum The erbium alloy liquid is poured into a holding furnace with a set temperature of 725 °C for heat preservation, and a rotary degasser is used to pass chlorine and argon into the alloy liquid for refining and degassing. When the temperature of the aluminum-erbium alloy liquid is 695 °C, Use a slag removal truc...
Embodiment 3
[0028] First, weigh the corresponding mass fractions of Cu: 25%, Fe: 0.3%, Ti: 3.0%, Mg: 2%, Zr: 15%, Cr: 0.05%, Sc: 0.5%, Er: 1%, Zn: 4%, and 0.1% of other impurities, the balance is Al, first process the bulk metal in the alloy composition into powder or chip form, and the Al in the alloy composition and the intermediate alloy in the order of melting point from high to low. Put it into a melting furnace for melting, and add a refining agent with a mass of 0.05% of the total alloy at a constant rate, heat it up to 950 ° C, and use electromagnetic stirring to accelerate the dissolution at a power of 250 kw to obtain an aluminum-erbium alloy liquid, and then aluminum The erbium alloy liquid is poured into a holding furnace with a set temperature of 750 °C for heat preservation, and a rotary degasser is used to pass chlorine and argon gas into the alloy liquid for refining and degassing. When the temperature of the aluminum-erbium alloy liquid is 720 °C, Use a slag removal truck...
PUM
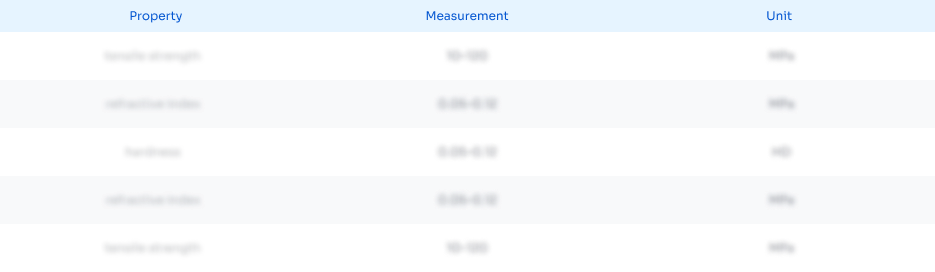
Abstract
Description
Claims
Application Information

- Generate Ideas
- Intellectual Property
- Life Sciences
- Materials
- Tech Scout
- Unparalleled Data Quality
- Higher Quality Content
- 60% Fewer Hallucinations
Browse by: Latest US Patents, China's latest patents, Technical Efficacy Thesaurus, Application Domain, Technology Topic, Popular Technical Reports.
© 2025 PatSnap. All rights reserved.Legal|Privacy policy|Modern Slavery Act Transparency Statement|Sitemap|About US| Contact US: help@patsnap.com