Nano-composite (Ti3Mo3Zr2Sn25Nb)-xHA biological material and preparation method thereof
A nanocomposite and biomaterial technology, applied in the field of nanocomposite-χHA biomaterial and its preparation, can solve the problems of anisotropy of microstructure and mechanical properties of sintered body, difficult to achieve good sintering, poor biocompatibility, etc. Achieve the effect of reducing reaction activation energy, avoiding component segregation and stable performance
- Summary
- Abstract
- Description
- Claims
- Application Information
AI Technical Summary
Problems solved by technology
Method used
Image
Examples
preparation example Construction
[0035] A preparation method of a biological material of the present embodiment includes the following steps:
[0036] Step 1: Weigh Ti, Mo, Zr, Sn, Nb powder raw materials;
[0037] Step 2: Put the weighed powder and stainless steel balls into the stainless steel ball milling tank for the first ball milling, and the mixing ball milling time is 8-12h;
[0038] Step 3: Weigh the HA powder according to the proportion, put it in the nano-scale HA powder, and then extract the vacuum again to carry out the second mechanical ball milling and powder mixing. The rotating speed is 300r / min, and the ball milling time is 2 hours. The ball-milled mixed powder is taken out and placed in a vacuum drying oven for drying to obtain a series of composite powders;
[0039] Step 4: Put the dried (Ti3Mo3Zr2Sn25Nb)-χHA (χ=0,5,10,15,20) mixed powder into a special graphite mold for pre-pressing, and then use a spark plasma sintering system for rapid sintering.
[0040] The specific operation steps ...
Embodiment 1
[0055] A preparation method of a biological material of the present embodiment includes the following steps:
[0056] Step 1: Weigh Ti, Mo, Zr, Sn, Nb powder raw materials; high-purity Ti powder (99%), high-purity Mo powder (99%), high-purity Zr powder (99%), high-purity Sn powder (99%) %), high-purity Nb powder (99%), high-purity HA powder (99%);
[0057] Step 2: Put the weighed powder and stainless steel balls into the stainless steel ball mill tank for the first ball milling, and the mixing ball milling time is 8h;
[0058] Step 3: Weigh the HA powder according to the proportion, put it in the nano-scale HA powder, and then extract the vacuum again to carry out the second mechanical ball milling and powder mixing. The rotating speed is 300r / min, and the ball milling time is 2 hours. The ball-milled mixed powder is taken out and placed in a vacuum drying oven for drying to obtain a series of composite powders;
[0059] Step 4: Put the dried (Ti3Mo3Zr2Sn25Nb)-χHA (χ=0,5,10,...
Embodiment 2
[0075] A preparation method of a biological material of the present embodiment includes the following steps:
[0076] Step 1: Weigh Ti, Mo, Zr, Sn, Nb powder raw materials; high-purity Ti powder (99%), high-purity Mo powder (99%), high-purity Zr powder (99%), high-purity Sn powder (99%) %), high-purity Nb powder (99%), high-purity HA powder (99%);
[0077] Step 2: Put the weighed powder and stainless steel balls into the stainless steel ball milling tank for the first ball milling, and the mixing ball milling time is 12h;
[0078] Step 3: Weigh the HA powder according to the proportion, put it in the nano-scale HA powder, and then extract the vacuum again to carry out the second mechanical ball milling and powder mixing. The rotating speed is 300r / min, and the ball milling time is 2 hours. The ball-milled mixed powder is taken out and placed in a vacuum drying oven for drying to obtain a series of composite powders;
[0079] Step 4: Put the dried (Ti3Mo3Zr2Sn25Nb)-χHA (χ=0,5...
PUM
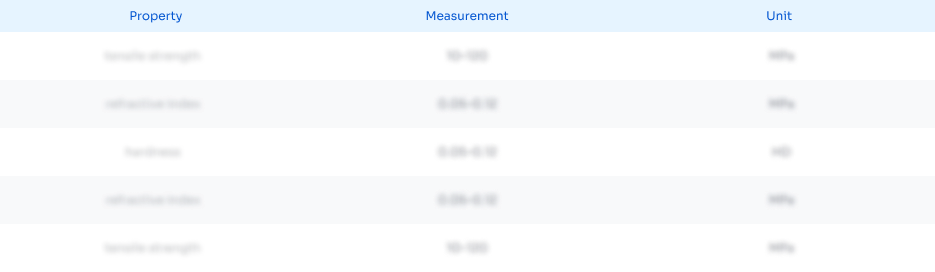
Abstract
Description
Claims
Application Information

- R&D Engineer
- R&D Manager
- IP Professional
- Industry Leading Data Capabilities
- Powerful AI technology
- Patent DNA Extraction
Browse by: Latest US Patents, China's latest patents, Technical Efficacy Thesaurus, Application Domain, Technology Topic, Popular Technical Reports.
© 2024 PatSnap. All rights reserved.Legal|Privacy policy|Modern Slavery Act Transparency Statement|Sitemap|About US| Contact US: help@patsnap.com