Manufacturing method for scale breaking tension leveler working roll
A manufacturing method and technology of tension leveling machine, applied in the direction of manufacturing tools, furnaces, heat treatment equipment, etc., can solve the problems of failure to meet the toughness requirements of the core, poor roll grinding performance, and brittle rolls, etc., and achieve the goal of reducing microcracks The effect of occurrence, improvement of wear resistance and reasonable stress distribution
- Summary
- Abstract
- Description
- Claims
- Application Information
AI Technical Summary
Problems solved by technology
Method used
Image
Examples
Embodiment 1
[0016] A working roll of a scale breaking and leveling machine, using Cr12MoVCo die steel as the material, the alloy components and weight percentages of Cr12MoVCo die steel are C: 1.40%, Si: 0.60%, Mn: 0.60%, P: 0.025%, S: 0.025%, Cr: 11.00%, Mo: 1.00%, V: 0.70%, Co: 0.30%, and the rest are Fe and unavoidable impurities.
[0017] The manufacturing method includes the following: rough turning—tempering—semi-finishing turning—setting treatment—rough grinding roller surface—preheating—intermediate frequency spray quenching—isothermal treatment—tempering—finishing to finished product; among them, the quenching and tempering process is: 650°C Preheating → 950°C well furnace heating for 50 minutes, oil quenching → 700°C high temperature tempering; preheating temperature is 400°C; intermediate frequency spray quenching is carried out at 1150°C, the workpiece is cooled to 250°C and sent to an oven for isothermal treatment at 250°C 3 hours; tempering at 500°C for 8 hours.
Embodiment 2
[0019] A working roll of a scale breaking and leveling machine, using Cr12MoVCo die steel as the material, the alloy components and weight percentages of Cr12MoVCo die steel are C: 1.48%, Si: 0.56%, Mn: 0.48%, P: 0.020%, S: 0.017%, Cr: 13.00%, Mo: 0.85%, V: 0.78%, Co: 0.43%, and the rest are Fe and unavoidable impurities.
[0020] The manufacturing method includes the following: rough turning - quenching and tempering - semi-finishing turning - shaping treatment - rough grinding roller surface - preheating - intermediate frequency spray quenching - isothermal treatment - tempering - finishing to finished product; wherein, the quenching and tempering process is: 600 ° C Preheating→heating at 950°C for 65 minutes and then oil quenching→730°C high temperature tempering; preheating temperature is 400°C; intermediate frequency spray quenching is carried out at 1150°C, after quenching, the workpiece is cooled to 200°C and sent to an oven for isothermal at 250°C Treat for 3 hours; te...
Embodiment 3
[0022] A working roll of a scale breaking and leveling machine, using Cr12MoVCo die steel as the material, the alloy components and weight percentages of Cr12MoVCo die steel are C: 1.60%, Si: 0.60%, Mn: 0.58%, P: 0.020%, S: 0.015%, Cr: 11.75%, Mo: 0.80%, V: 1.00%, Co: 0.50%, and the rest are Fe and unavoidable impurities.
[0023] The manufacturing method includes the following: rough turning—tempering—semi-finishing turning—setting treatment—rough grinding of roll surface—preheating—medium frequency spray quenching—isothermal treatment—tempering—finishing to finished product; among them, the quenching and tempering process is: 620°C Preheating→heating at 950°C for 70 minutes and then oil quenching→710°C high temperature tempering; preheating temperature is 400°C; intermediate frequency spray quenching is carried out at 1160°C, after quenching, the workpiece is cooled to 250°C and sent to an oven for isothermal at 250°C Treat for 3 hours; temper at 510°C for 9 hours.
[0024]...
PUM
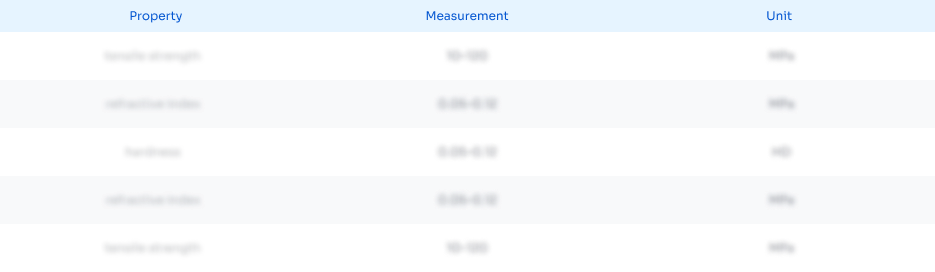
Abstract
Description
Claims
Application Information

- R&D
- Intellectual Property
- Life Sciences
- Materials
- Tech Scout
- Unparalleled Data Quality
- Higher Quality Content
- 60% Fewer Hallucinations
Browse by: Latest US Patents, China's latest patents, Technical Efficacy Thesaurus, Application Domain, Technology Topic, Popular Technical Reports.
© 2025 PatSnap. All rights reserved.Legal|Privacy policy|Modern Slavery Act Transparency Statement|Sitemap|About US| Contact US: help@patsnap.com